Welcome to our guide on vendor subcontractor management policies! As businesses grow and evolve, effectively managing subcontractors becomes crucial to ensuring seamless operations and maintaining quality standards. In this article, we will explore best practices for creating a comprehensive policy that not only aligns with your company's goals but also fosters strong relationships with your partners. So, if you're ready to optimize your subcontractor management strategy, keep reading to discover valuable insights and tips!
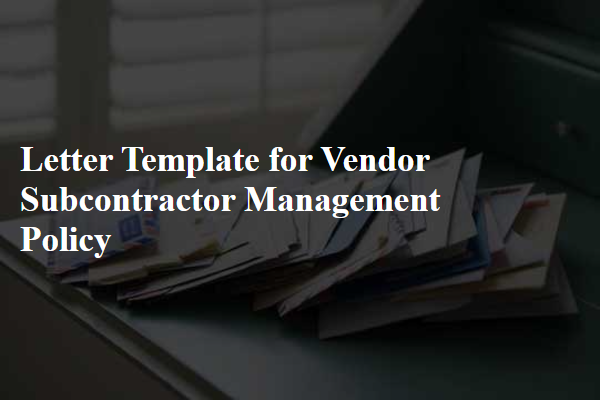
Purpose and Scope
A vendor subcontractor management policy is crucial for organizations, such as manufacturing companies, to establish guidelines for effective oversight of third-party contractors. This policy aims to ensure compliance with industry standards, such as ISO 9001, providing clear criteria for selecting, evaluating, and monitoring subcontractors. The scope encompasses all types of subcontractors involved in service delivery and production processes, including local suppliers in regions like the Midwest and international vendors from Asia. Key aspects include defining roles and responsibilities, ensuring documentation of agreements, and maintaining performance metrics to assess quality, timeliness, and adherence to safety regulations. The ultimate goal remains to mitigate risks, enhance collaboration, and uphold organizational integrity throughout all subcontractor engagements.
Roles and Responsibilities
Vendor subcontractor management policy outlines key roles and responsibilities essential for effective oversight and collaboration. The primary stakeholders typically include the procurement department, responsible for selecting and negotiating contracts with subcontractors, ensuring compliance with company standards. Project managers oversee the implementation of subcontractor tasks, ensuring alignment with project timelines and quality criteria. Compliance officers monitor regulatory adherence, mitigating risks associated with subcontractor practices. Additionally, financial analysts manage budget allocations and expenditures related to subcontracting services, ensuring fiscal responsibility. Each role plays a crucial part in fostering a transparent and efficient subcontracting process that aligns with organizational goals.
Vendor Selection and Evaluation Process
The vendor selection and evaluation process ensures that organizations engage with reliable subcontractors for project execution. Initial criteria involve assessing vendor qualifications, such as industry certifications like ISO 9001 for quality management systems and operational experience, which may include a minimum of five years in the relevant sector. Comprehensive evaluations consider financial stability metrics, including credit ratings and bank references, to confirm the vendor's ability to fulfill contractual obligations. Additionally, performance history reviews encompass previous client feedback and project timelines adhered to, with specific attention to any penalties faced for lateness. Finally, the due diligence phase includes site visits to verify capabilities and resource availability, as well as a risk assessment focusing on potential issues that could affect service delivery. This structured approach establishes robust partnerships and mitigates risks associated with subcontractor involvement in projects.
Contract Terms and Compliance
A robust vendor subcontractor management policy is vital for ensuring compliance with contractual obligations across all partnerships, particularly within regulated industries such as construction or healthcare. This policy outlines key components related to ensuring that subcontractors adhere to the initial contract terms established at the onset of the agreement. Those terms may include deliverables such as project milestones defined within the original contract (often benchmarked against specific dates and quantities), quality standards (often dictated by industry regulations or client specifications), and financial commitments (which include payment schedules tied to milestones). Regular audits, typically conducted quarterly, assess the compliance level of subcontractors, ensuring alignment with client expectations and legal requirements. Essential documentation, such as certificates of insurance or licenses, must be verified and maintained throughout the relationship to mitigate risks associated with non-compliance and liability issues. Clear communication channels and documentation practices are critical for addressing any deviations from agreed terms, encompassing immediate reporting protocols and corrective actions that can be implemented to align subcontractor performance with contractual expectations.
Performance Monitoring and Reporting
Effective vendor subcontractor management is essential for ensuring quality service delivery. Performance monitoring (systematic assessment of subcontractor activities) should be conducted through regular evaluations to guarantee adherence to contract specifications. Metrics such as key performance indicators (KPIs) (quantifiable measures of performance), response times, and customer satisfaction ratings must be utilized to assess subcontractor effectiveness. Reporting mechanisms must be established, including monthly performance reports (detailed analysis of performance data), where subcontractors provide updates on their progress and challenges. Regular meetings (structured discussions) between primary contractors and subcontractors enhance communication, promote accountability, and facilitate continuous improvement in service delivery standards. Additionally, compliance with industry regulations (specific legal and safety standards) must be reviewed and documented to ensure overall operational integrity and risk mitigation.
Letter Template For Vendor Subcontractor Management Policy Samples
Letter template of Vendor Subcontractor Relationship Management Protocol
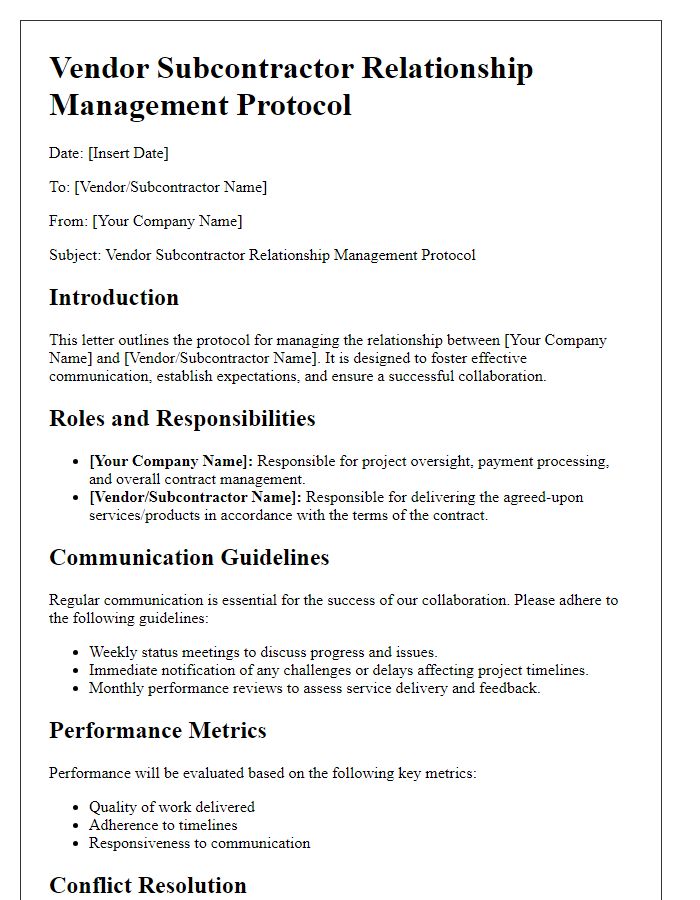
Letter template of Vendor/Subcontractor Collaboration and Accountability
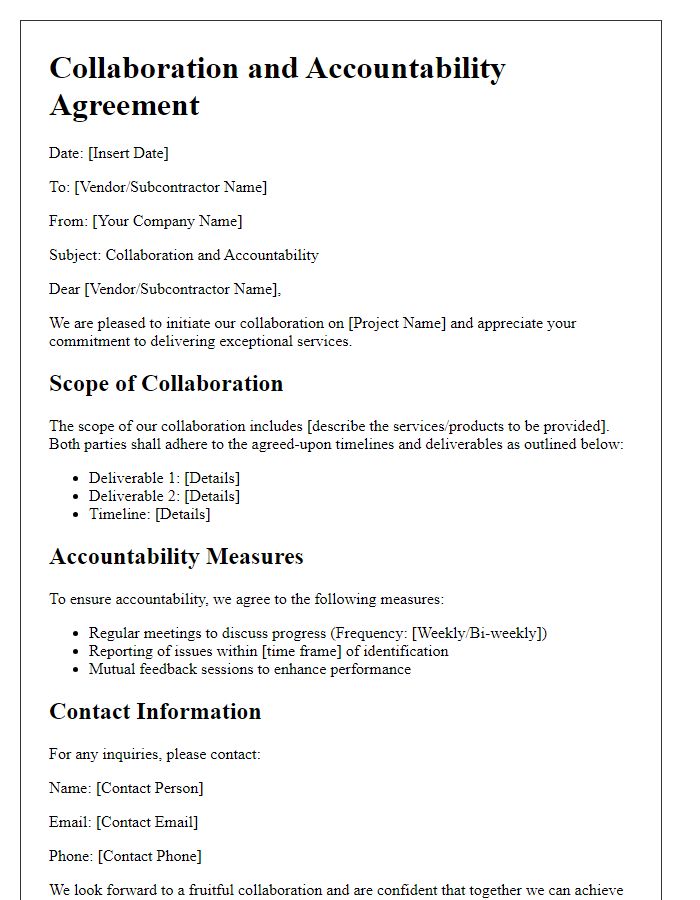
Comments