Are you a subcontractor looking to elevate your quality standards? In todayâs competitive landscape, ensuring exceptional quality in your work isn't just a goal; it's a necessity. This article will explore effective strategies that can help you enhance the quality of your services, ultimately leading to greater client satisfaction and stronger partnerships. So, letâs dive in and discover how quality improvement can transform your subcontractor journey!
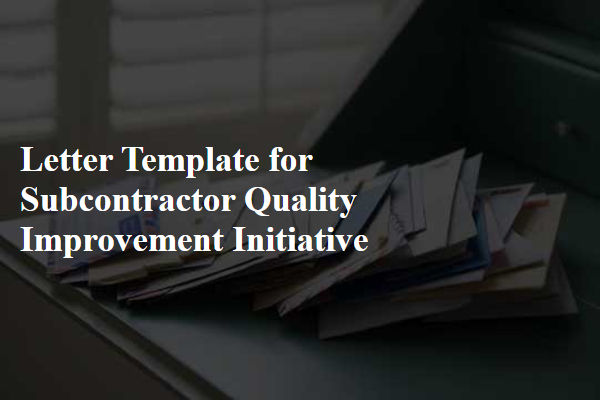
Clear Objective Statement
The subcontractor quality improvement initiative aims to enhance the overall performance of contracted services by implementing standardized quality control measures and fostering effective communication channels. This initiative focuses on reducing defects in workmanship, ensuring compliance with the latest industry standards, and aligning subcontractor practices with our core business objectives. Key performance indicators will be established to measure success, including a target reduction of defect rates by 25% within the next fiscal year. Regular training sessions and audits of subcontractor operations will contribute to building a consistent quality culture across all projects. In collaboration with subcontractors, continuous feedback mechanisms will be employed to facilitate ongoing improvements and address areas of concern promptly. This collaborative approach will strengthen partnerships while delivering superior results for our clients and stakeholders.
Defined Quality Standards
Implementing defined quality standards is essential for subcontractors in the construction industry to enhance project outcomes. Clear benchmarks, such as adherence to ISO 9001:2015 quality management systems, ensure consistent performance across all tasks. Regular training sessions (conducted quarterly) on specific quality protocols can improve the skillset of workers, increasing efficiency and reducing the margin for error. Documentation practices, including daily logs and inspection checklists, foster accountability and traceability, illustrating a commitment to excellence. Moreover, periodic quality audits by third-party organizations can assess compliance with established guidelines, highlighting areas for improvement and ensuring adherence to client specifications. Elevating the quality framework ultimately leads to superior project delivery and greater client satisfaction.
Detailed Action Plan
A subcontractor quality improvement initiative involves implementing a structured action plan to enhance performance in construction and manufacturing processes. This detailed action plan should include key components such as specific quality objectives, measurable criteria, and targeted timelines to ensure compliance. Key performance indicators (KPIs) like defect rates, customer satisfaction scores, and on-time delivery percentages should be established to track improvements. Training sessions for subcontractor teams should cover industry standards (such as ISO 9001) and best practices to elevate overall quality. Regular audits and assessments (conducted bi-annually) will monitor progress and identify areas for continued improvement. Collaboration between primary contractors and subcontractors should be fostered through open communication channels, promoting a culture of accountability and shared quality goals. The initiative should also outline reward mechanisms for notable improvements to motivate subcontractors in achieving excellence.
Milestones and Deadlines
The quality improvement initiative for subcontractors emphasizes crucial milestones and deadlines to enhance performance and compliance within project frameworks, specifically focusing on sectors such as construction (with adherence to safety standards) and manufacturing (ensuring quality control measures). Initial assessments must be completed by the end of the first quarter, specifically March 31, 2024, involving comprehensive evaluations of current practices, identifying key performance indicators (KPIs). By June 30, 2024, a strategic plan aimed at addressing gaps must be implemented, covering training sessions for subcontractors that incorporate quality improvement methodologies (such as Six Sigma or Total Quality Management). Final evaluations, including feedback from stakeholders, are expected by September 15, 2024, producing insights into the effectiveness of the initiatives and adjustments to future contracts. Compliance audits will occur quarterly, beginning April 2024, to ensure ongoing adherence to quality standards.
Contact Information and Support
Subcontractor quality improvement initiatives require effective communication and support structures. Essential elements include designated contact points for specific issues, ensuring clarity regarding roles and responsibilities within the project management framework. Primary contact personnel should include a Quality Assurance Manager, whose expertise in construction standards ensures compliance with regulatory requirements. Furthermore, a dedicated support hotline facilitates immediate assistance, addressing quality-related concerns swiftly. Regular training sessions are also essential, focusing on best practices in workmanship and material usage. These initiatives aim to enhance overall project outcomes, foster collaboration among subcontractors, and maintain high-quality standards throughout various construction phases.
Letter Template For Subcontractor Quality Improvement Initiative Samples
Letter template of subcontractor continuous quality improvement initiative
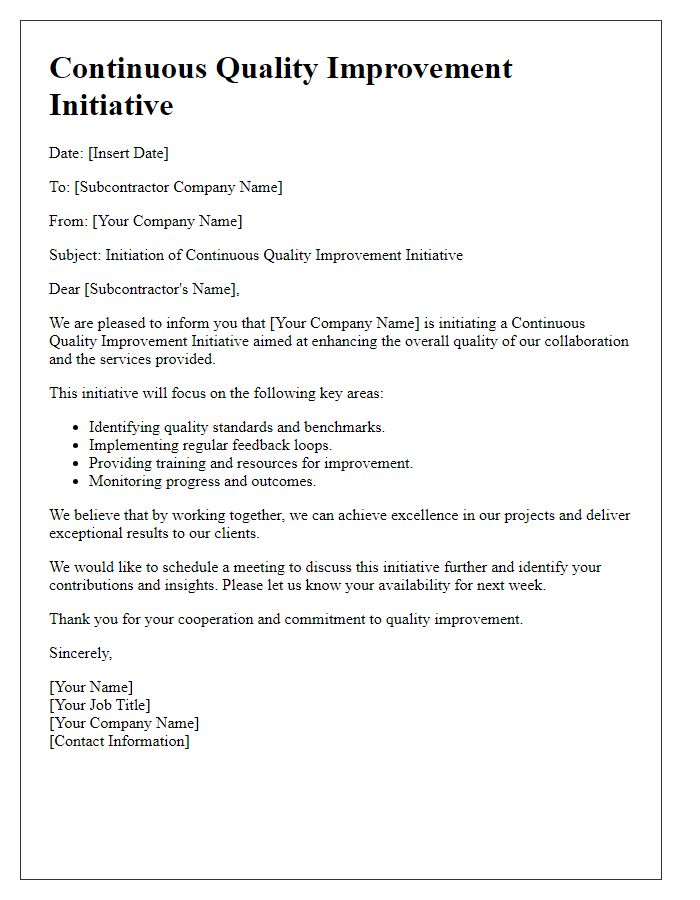
Comments