In today's fast-paced business world, effective collaboration within the supply chain is more crucial than ever. Whether you're a seasoned professional or new to the industry, understanding the nuances of partnership can significantly enhance efficiency and drive innovation. By synergizing efforts across various stakeholders, we can unlock new levels of productivity and customer satisfaction. So, if you're ready to delve deeper into the strategies for successful supply chain collaboration, keep reading!
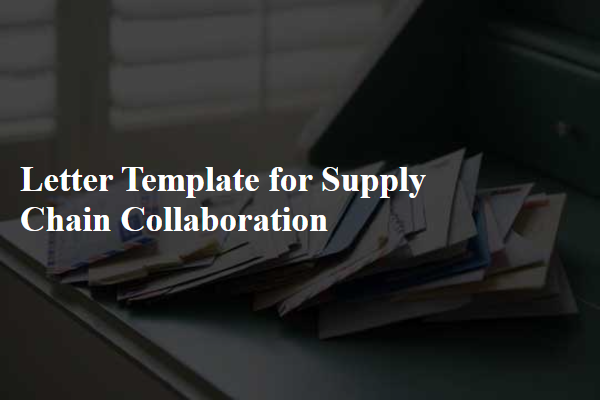
Introduction and Purpose
Supply chain collaboration is essential for optimizing efficiency and enhancing overall performance in logistics and resource management. Effective collaboration involves engaging multiple stakeholders, including manufacturers, distributors, and retailers, to share information, streamline processes, and reduce delays. The primary purpose of fostering collaboration within the supply chain is to create synergy, enabling partners to respond swiftly to market demands and ensure timely delivery of products. By adopting collaborative strategies such as joint planning, inventory sharing, and risk management, organizations can significantly decrease costs and improve customer satisfaction, ultimately leading to a more resilient supply chain ecosystem.
Roles and Responsibilities
In modern supply chain collaborations, defining roles and responsibilities is crucial for efficiency and accountability. The procurement team, tasked with sourcing materials, engages with suppliers to ensure quality products and timely deliveries, while the logistics department manages the transportation and warehousing of goods, utilizing technology like RFID for tracking shipments. Additionally, the production team coordinates with inventory management to maintain optimal stock levels, thereby minimizing costs associated with excess inventory, which, on average, can account for 20% of operational expenses. Quality assurance personnel conduct regular audits to ensure compliance with industry standards, particularly in manufacturing processes adopted by suppliers. Moreover, the sales and distribution teams work closely with marketing efforts to align demand forecasting strategies, ensuring that supply meets market requirements effectively. Clear documentation, such as Service Level Agreements (SLAs), outlines expectations and performance metrics for all parties involved, fostering a transparent and collaborative environment in the supply chain ecosystem.
Strategic Objectives and Goals
Strategic objectives in supply chain collaboration encompass enhancing operational efficiency, reducing costs, and improving customer satisfaction. Achieving these goals often involves implementing technology solutions, such as cloud-based platforms for real-time data sharing, which can streamline communication among partners. Supply chain integration aims to create seamless workflows across multiple entities, including suppliers, manufacturers, and distributors, facilitating quicker decision-making processes. Utilizing performance metrics, such as inventory turnover rates and on-time delivery percentages, allows organizations to assess progress towards their strategic initiatives. Regular synchronization of goals among partners promotes alignment and fosters a culture of continuous improvement, ultimately driving competitive advantage in a dynamic market.
Communication and Coordination
Effective communication and coordination in supply chain collaboration can significantly enhance operational efficiency and reduce delays. Timely information exchange between stakeholders, encompassing suppliers, manufacturers, and distributors, is essential for tracking inventory levels and forecasting demand. Advanced technologies such as cloud-based platforms facilitate real-time updates and promote transparency throughout the supply chain. Key performance indicators (KPIs) like order fulfillment rates, lead times, and inventory turnover provide measurable insights into collaboration effectiveness. Regular meetings and structured reporting enable proactive problem-solving, ensuring that all partners can respond swiftly to fluctuations in supply and demand. Establishing trust among participants fosters a collaborative culture, ultimately driving competitive advantages in the marketplace.
Performance Metrics and Evaluation
Performance metrics in supply chain collaboration play a critical role in measuring the efficiency and effectiveness of operations. Key performance indicators (KPIs), such as order fulfillment rate, inventory turnover ratio, and lead time, provide insight into the operational success at different points in the supply chain. Timely data analysis at intervals, such as quarterly or annually, allows for informed decision-making and continuous improvement. Geographic locations, like distribution centers in Atlanta and Los Angeles, can influence logistics performance, thus impacting transportation and overall cost. Collaborators should assess qualitative metrics, such as customer satisfaction scores, to ensure alignment with end-user expectations. Establishing clear benchmarks for success fosters accountability and enhances partnerships among stakeholders, ultimately driving collective growth within the supply chain ecosystem.
Comments