Are you looking to streamline your logistics operations but unsure where to start? Coordinating logistics can be a complex task, involving multiple stakeholders and intricate processes; however, a well-structured approach can make all the difference. In this article, weâll guide you through essential strategies for effective logistics coordination that can save time and resources. So, grab a cup of coffee and dive in to discover how you can enhance your logistics efficiency!
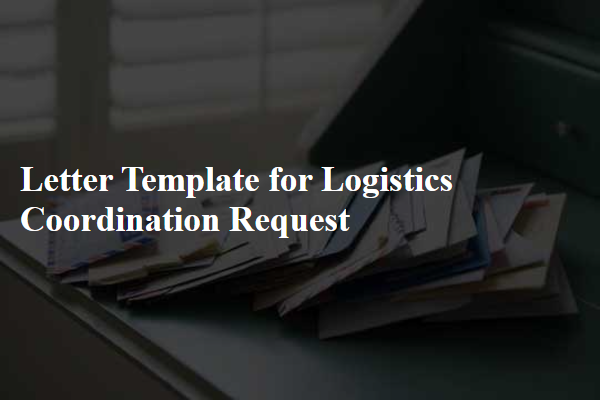
Sender and Receiver Information
In a logistics coordination context, timely and accurate information exchange facilitates seamless supply chain operations. Essential elements include sender information, such as the name of the logistics coordinator or department, contact number (which typically begins with the country code, e.g., +1 for the United States), and email address. Receiver information encompasses the recipient's name, company name (often indicating their sector, like warehousing or transportation), delivery address (including city, state/province, and zip/postal code), and preferred contact method. This structured communication ensures clarity among parties, reducing the chances of delays or errors in shipments. Effective logistics coordination requires these data points for tracking shipments, managing schedules, and optimizing delivery routes.
Purpose of the Request
The logistics coordination request aims to streamline the transportation process for an upcoming shipment from the manufacturer in Guangdong Province, China, to the distribution center in Los Angeles, California. Key elements include managing the timeline to ensure delivery by the end of November 2023, coordinating with freight forwarders, and securing necessary customs documentation for efficient clearance at the Port of Los Angeles. Furthermore, adequate communication with local warehousing partners is essential to prepare for the incoming goods and optimize inventory management. Proper coordination will mitigate delays and ensure alignment with the supply chain schedule, thus maintaining operational efficiency.
Detailed Requirements
Logistics coordination in supply chain management involves multiple critical aspects, including inventory levels, transportation schedules, and order fulfillment processes. Timely and efficient transportation options, such as freight shipping (often exceeding 30% of overall costs in some sectors), can influence project deadlines significantly. Precise inventory tracking methods, utilizing technologies like RFID and barcode scanning, ensure that stock availability matches demand forecasts. Effective communication between stakeholders, such as suppliers in China and distributors in the United States, is crucial for minimizing delays and optimizing operations. In addition, adhering to industry regulations, including international customs procedures and local shipping laws, establishes compliance and reduces the risk of penalties or shipment delays.
Timeline and Deadlines
In logistics coordination, establishing a clear timeline is essential for successful operations. A typical deadline is set for three weeks prior to the event or shipment date, allowing ample time for planning and adjustments. Key milestones include the initial inventory assessment, scheduled for week one, followed by procurement of materials in week two, ensuring that all items comply with shipping regulations of countries involved, such as the United States and Canada. Transportation arrangements, including freight forwarding, may need confirmation by week two to avoid delays. Final delivery schedules require verification one week before the deadline to accommodate any unforeseen issues, such as customs inspections or weather-related disruptions. Keeping all stakeholders informed through regular updates fosters transparency and efficient problem-solving as challenges arise.
Contact Information and Follow-up Plan
Logistics coordination is essential for streamlining supply chain processes within companies like FedEx and UPS. Proper contact information must include key individuals such as logistics managers, warehouse supervisors, and shipment coordinators (ensuring smooth communication across different departments). A follow-up plan should outline specific timelines for updates (like weekly check-ins) and designate responsible persons for each task to guarantee accountability. It's vital to incorporate shipping details such as tracking numbers, delivery locations like distribution centers, and any expected delays due to unforeseen events (like weather disruptions or customs clearance).
Letter Template For Logistics Coordination Request Samples
Letter template of logistics coordination request for event materials delivery.
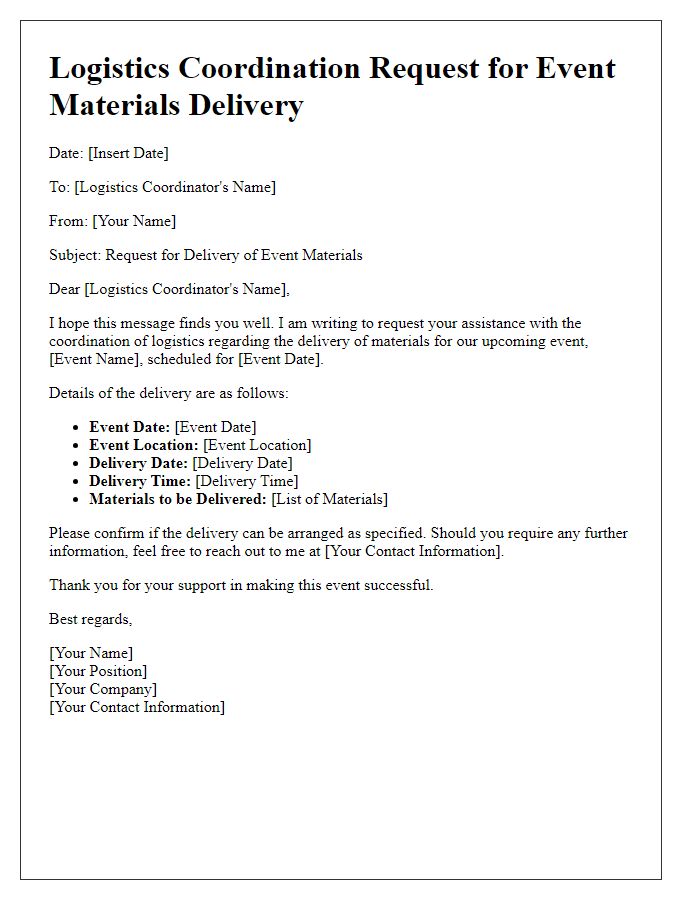
Letter template of logistics coordination request for inventory management.
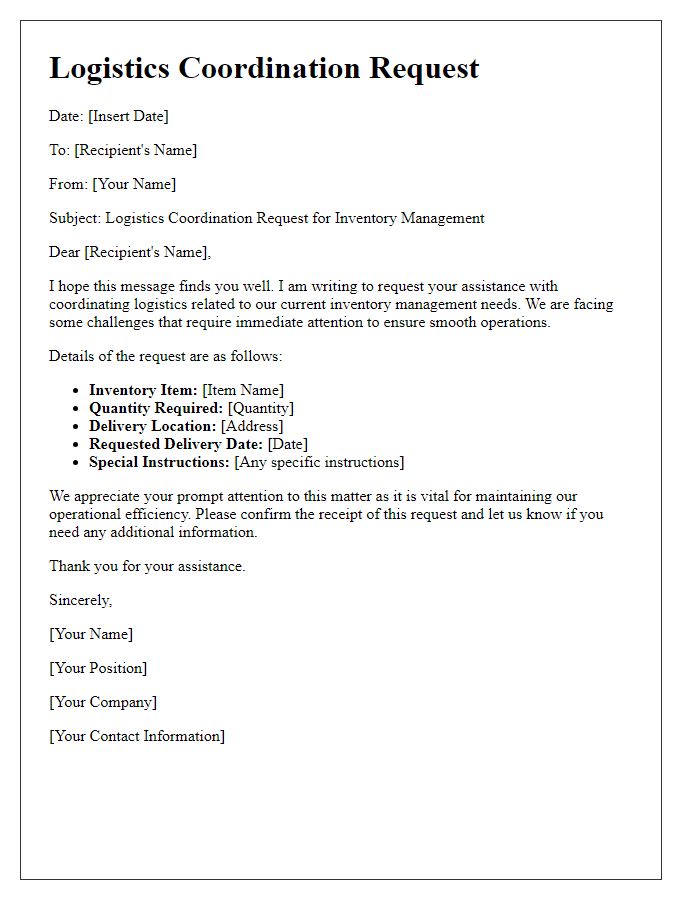
Letter template of logistics coordination request for cross-border transportation.
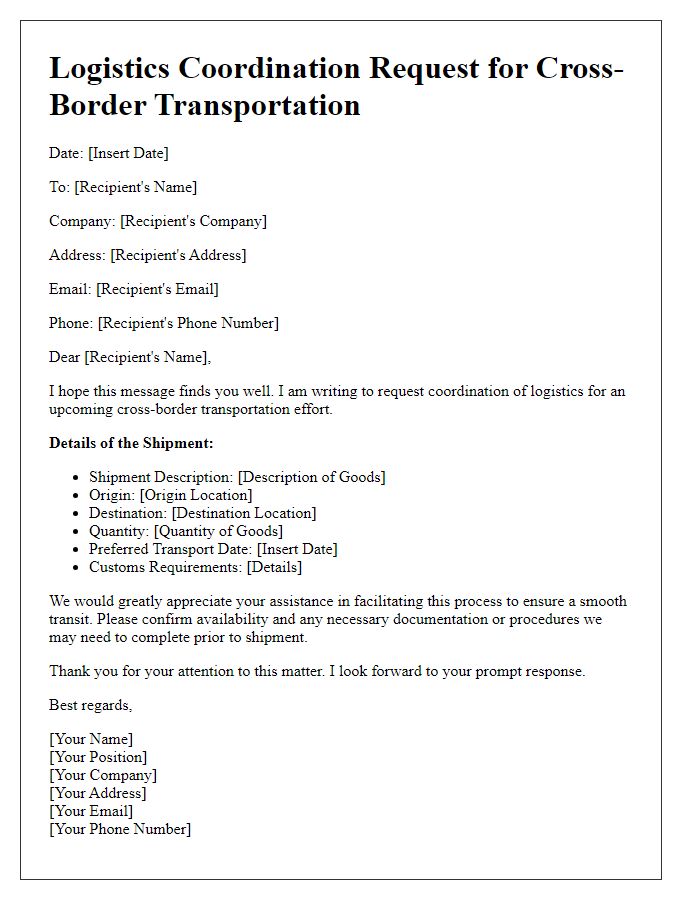
Letter template of logistics coordination request for freight scheduling.
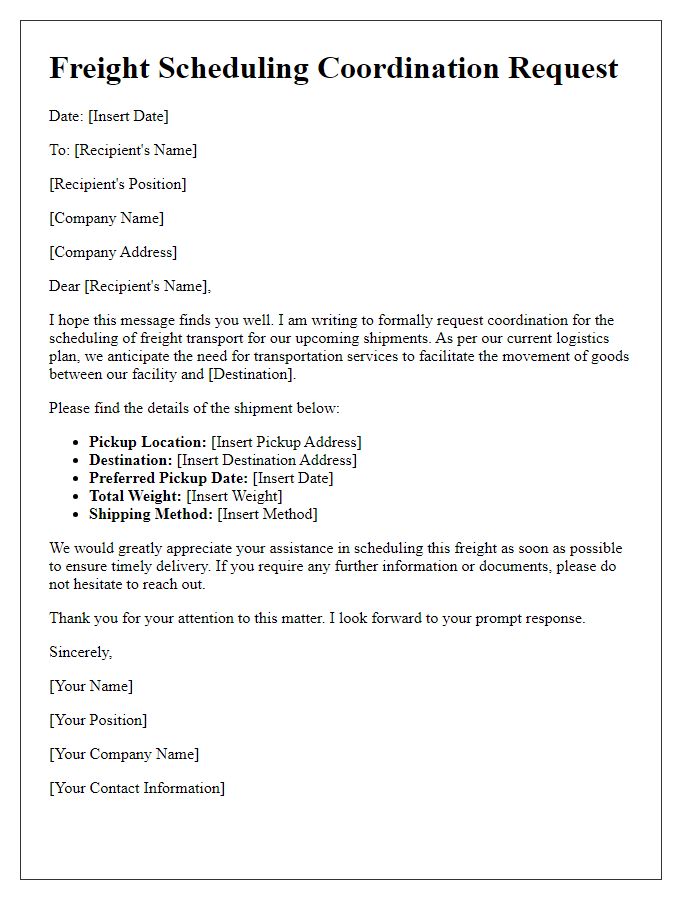
Letter template of logistics coordination request for supply chain optimization.
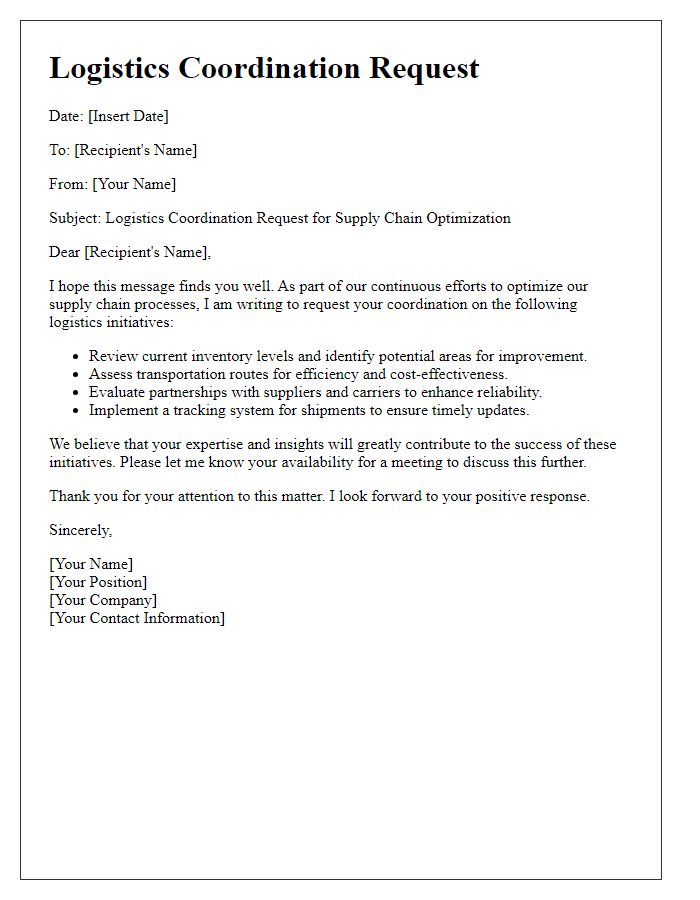
Letter template of logistics coordination request for on-site logistics support.
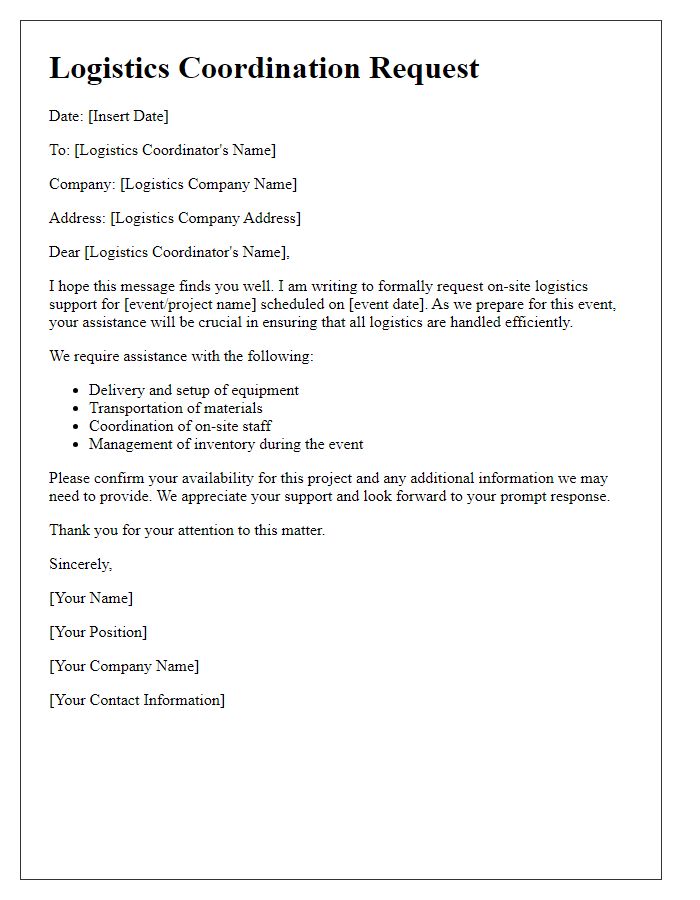
Letter template of logistics coordination request for distribution center operations.
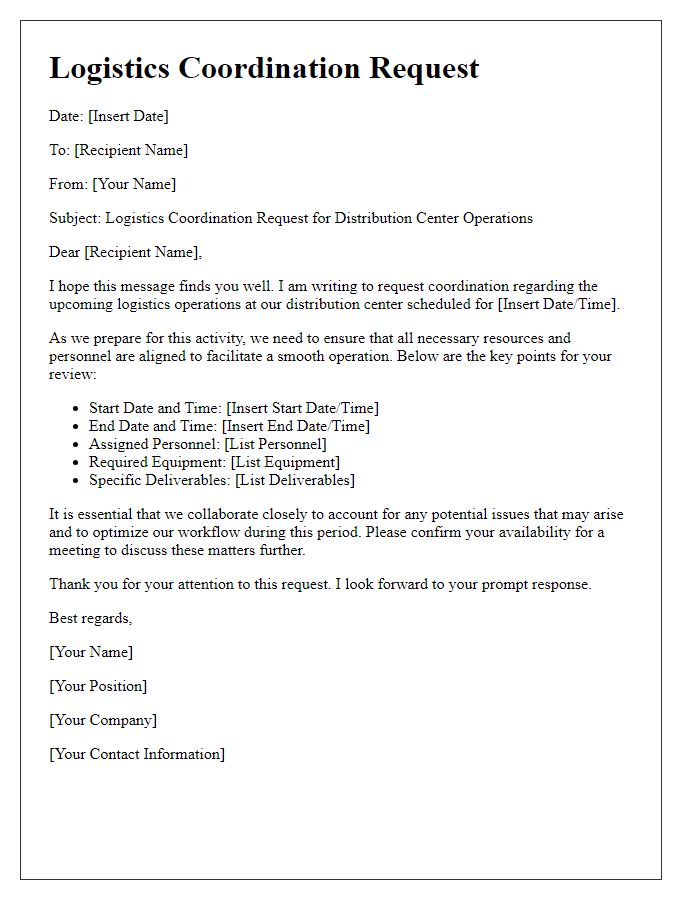
Letter template of logistics coordination request for emergency response logistics.
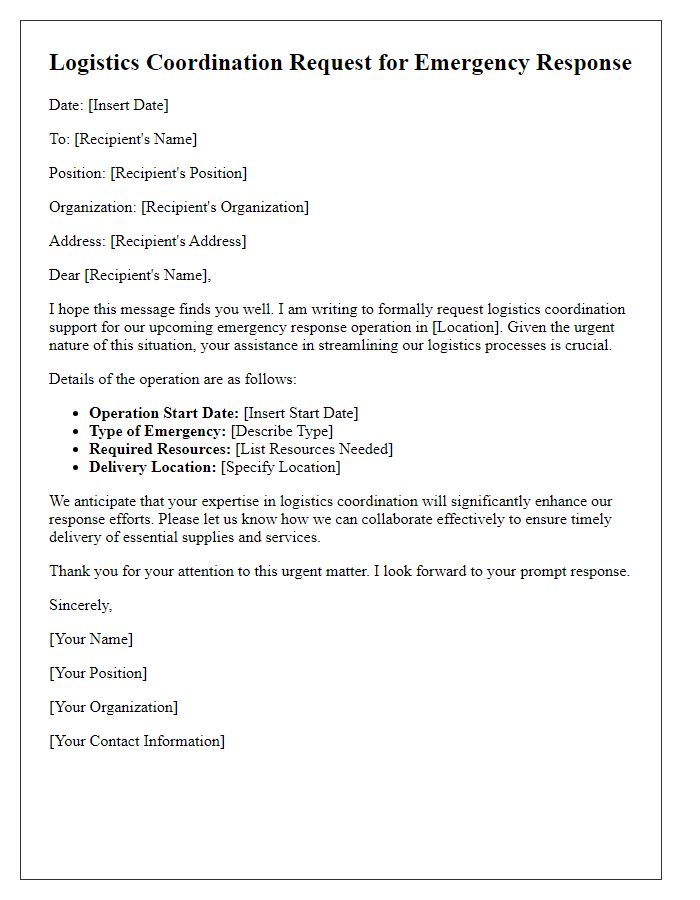
Comments