In today's fast-paced business environment, maintaining high-quality standards with your vendors is crucial for success. Implementing a robust quality control improvement plan not only enhances the products you receive but also strengthens your partnership with suppliers. By fostering open communication and setting clear expectations, you can ensure that both parties are aligned in their commitment to excellence. Curious about effective strategies to enhance vendor quality control? Keep reading to discover practical tips and insights!
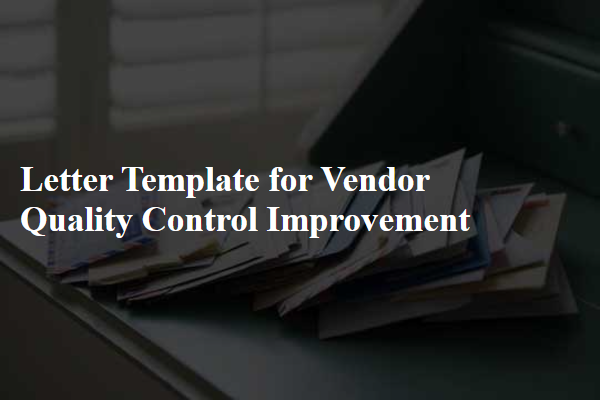
Clear Quality Standards
Establishing clear quality standards is essential for enhancing vendor quality control in manufacturing processes. Specific criteria for materials, such as minimum tensile strength of 300 MPa for metals, are crucial for ensuring product durability. Regular audits, scheduled every six months, help to assess compliance with these standards at vendor facilities in regions like Southeast Asia, where many manufacturing operations are based. Implementing a robust training program for vendor employees, focusing on quality assurance techniques such as Statistical Process Control (SPC), can significantly reduce defects. Introducing a feedback mechanism allows for continuous improvement, ensuring that all parties remain aligned with expectations, fostering transparency and collaboration. Setting measurable targets, like reducing defect rates to below 2% within the next quarter, can drive commitment towards achieving higher quality outputs, ultimately benefiting the supply chain.
Detailed Evaluation Criteria
In vendor quality control improvement, establishing detailed evaluation criteria is essential for ensuring product reliability and compliance with industry standards. Key factors include defect rates, which should ideally be below 2% for manufacturing processes; delivery performance, requiring at least 95% on-time shipments; and adherence to specifications documented in contracts, where 100% compliance is the target. Additionally, inspections must occur at various stages, such as incoming material checks, in-process quality checks, and final product evaluations. Tools like Six Sigma methodologies and ISO 9001 standards can guide quality improvement efforts, emphasizing statistical analysis to identify root causes of defects. Tracking customer feedback and implementing corrective actions are also critical components, impacting vendor relationships and overall supply chain effectiveness. Regular audits and performance reviews help maintain standards and drive continuous improvement.
Consistent Feedback Loop
Implementing a consistent feedback loop within vendor quality control processes is essential for enhancing product standards. Regular evaluations of vendor performance, involving specific metrics such as defect rates and delivery timelines, can create a structured framework for communication. Establishing routine meetings (monthly or quarterly) to review quality metrics at facilities located in regions such as Asia and Europe assists in identifying potential issues early. Additionally, utilizing software tools for tracking quality-related feedback from end-users allows for real-time analysis. Empowering vendors through training programs and sharing best practices fosters a collaborative environment that encourages continuous improvement. Ultimately, this proactive approach not only enhances product quality but also strengthens vendor partnerships.
Corrective Action Plan
A Corrective Action Plan (CAP) for vendor quality control improvement outlines specific steps to address deficiencies in product quality delivered by suppliers. This CAP consists of identifying root causes such as non-compliance with standards, failure in process adherence, and inadequate employee training. Establishing measurable objectives is critical, with guidelines like reducing defect rates by 30% within three months. Implementing regular audits at vendor facilities, such as bi-weekly inspections in regions like Southeast Asia, will help monitor adherence to quality benchmarks. Training sessions focusing on ISO 9001 standards, involving at least 50% of the vendor's workforce, will enhance understanding of quality expectations. Documenting these actions, timelines, and responsible parties in a transparent manner ensures accountability and facilitates future evaluation of progress towards quality improvement goals.
Performance Monitoring System
Performance monitoring systems facilitate the continuous assessment of vendor quality control measures, ensuring compliance with industry standards such as ISO 9001. Key metrics such as defect rates, delivery times, and adherence to specifications play a crucial role in evaluating vendor performance. Implementing regular audits (quarterly or biannual, depending on the contract terms) enhances collaboration between procurement teams and suppliers, identifying areas for improvement. Geographic considerations, such as vendor location (domestic vs. international), may also impact lead times and logistics. Furthermore, utilizing advanced data analytics tools can provide insights into trends over time, aiding in strategic decision-making for supplier selection and retention. Effective communication channels, such as performance review meetings, contribute to fostering strong partnerships while mitigating risks associated with quality failures.
Comments