Are you preparing to negotiate batch testing with your supplier? Itâs essential to approach this discussion with a clear strategy that aligns your quality standards with their capabilities. In this article, weâll explore effective techniques for ensuring that your batch tests not only meet your specifications but also foster a collaborative relationship with your supplier. Read on to discover practical tips that will enhance your negotiation process and lead to successful outcomes!
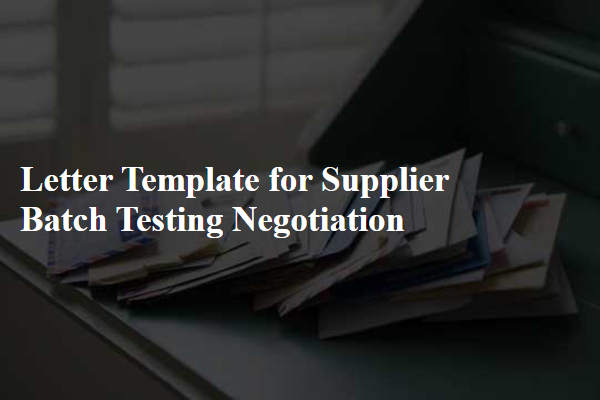
Clarity and Precision
In vendor contract negotiations for batch testing procedures, clarity and precision are essential to establish mutual understanding. Suppliers must adhere to specific testing protocols to ensure product consistency and quality. Batch testing refers to assessing samples from production lots, with standards set by industry benchmarks like ISO/IEC 17025 for laboratory accreditation. Parameters include material specifications, chemical composition, and performance metrics, which must be documented in test reports. Clear timelines for testing phases, such as initial sampling, analysis duration (typically 5-7 business days), and delivery of results, are crucial. Parties must also negotiate pricing structures related to testing services, with costs influenced by factors such as sample size and complexity. Establishing these details protects both supplier and buyer interests, ensuring seamless transaction flow and minimizing disputes.
Terms and Conditions
Negotiating terms and conditions for supplier batch testing involves several essential components. A detailed contract outlines responsibilities, including adherence to industry standards (such as ISO 9001), testing protocols (like ASTM methods), materials specifications (e.g., type, grade), and acceptable failure rates (typically between 1% and 5%). It is crucial to define the timeline for batch testing procedures (usually ranging from three days to two weeks), delivery schedules for test results, and penalties for delays (potentially up to 10% of the contract value). Payment terms must also be explicitly stated, reflecting agreed rates for testing services and potential batch re-testing costs (often 25% of the original testing fee). Additionally, specify liability clauses to address defective goods and the recourse available (such as refunds or replacements) should a batch fail to meet quality assurance benchmarks. Ensuring clear communication regarding these terms fosters collaboration and builds a strong supplier relationship.
Deadlines and Timelines
Effective supplier batch testing negotiations require a clear understanding of deadlines and timelines for each stage of the process. Importantly, each batch, specifically those with sensitive materials, must undergo rigorous testing protocols adhering to industry standards such as ISO 9001. Detailed timelines should outline the testing phases, starting from the initial submission of samples, which ideally should occur within two weeks of order receipt, followed by testing durations that range from five to ten business days, contingent upon testing complexity. Moreover, communication checkpoints should be established at key milestones, including pre-testing meetings to discuss criteria and parameters, mid-testing updates to address any discrepancies, and final review sessions for results. Enhancing clarity with specific dates for report delivery, potential retesting windows, and final approval timelines will facilitate a smoother negotiation process and foster stronger partnerships based on reliability and efficiency.
Quality Assurance Standards
Negotiating supplier batch testing for Quality Assurance Standards requires detailed discussions on specific metrics and protocols. Suppliers must adhere to established benchmarks such as ISO 9001, which specifies requirements for quality management systems. Batch testing frequency may differ based on product type; for instance, pharmaceutical industries often mandate validation every 1000 units. The importance of statistical process control (SPC) should be emphasized to monitor process stability. Specifications for acceptable quality levels (AQL) should also be defined, typically set at 1.5% defects for electronic components. Documentation of testing results and compliance is crucial for traceability, ensuring products meet safety standards established by regulatory bodies such as the FDA or CE marking in Europe.
Communication and Collaboration Channels
Effective communication and collaboration channels are crucial in the negotiation process for supplier batch testing agreements, particularly in industries like pharmaceuticals and manufacturing. Utilizing platforms such as Microsoft Teams or Slack can enhance real-time discussions, ensuring that all stakeholders, including quality assurance professionals and supply chain managers, remain aligned. An organized schedule for weekly check-ins can facilitate timely information sharing regarding testing outcomes and any potential discrepancies. Document sharing services like Google Drive or Dropbox streamline access to important files, such as testing protocols and compliance reports. Establishing these channels early on fosters transparency, builds trust, and ultimately leads to more successful negotiations with suppliers regarding batch testing parameters and expectations.
Comments