Are you looking to streamline your supplier selection process? Understanding the essential pre-qualification criteria can save you time and ensure you partner with the most reliable vendors. From financial stability to compliance with industry standards, having a clear framework is crucial for making informed decisions. Dive into our article to explore the key criteria for an effective supplier pre-qualification process!
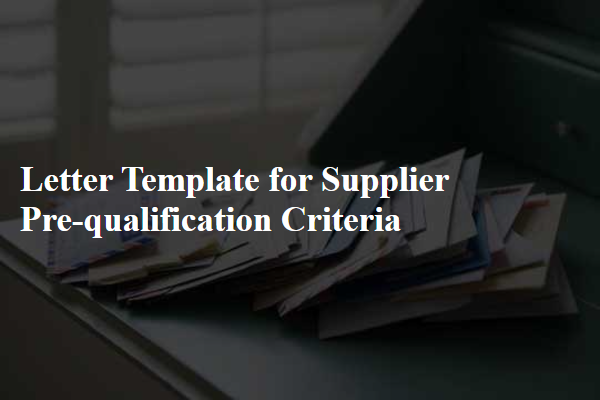
Company Background and Industry Experience
The company's background encompasses over two decades of experience within the manufacturing industry, specializing in high-quality components for the automotive sector. Established in 2003, the firm operates out of a state-of-the-art facility located in Detroit, Michigan, covering 100,000 square feet. The organization has successfully completed projects for renowned global brands such as Ford and General Motors, showcasing a proven track record of delivering innovative solutions and maintaining rigorous compliance with ISO 9001 standards. Additionally, the team consists of over 200 skilled employees, including engineers with expertise in automotive design and production processes, contributing to the firm's reputation as a reliable supplier in a highly competitive market.
Financial Stability and Creditworthiness
Financial stability is a crucial factor in assessing potential suppliers, ensuring they possess adequate resources to fulfill contractual obligations effectively. Key indicators include a positive net worth, a healthy current ratio (typically above 1.5), and consistent revenue growth (averaging at least 5% annually over the past three years). Additionally, creditworthiness is evaluated through credit scores from major agencies, ideally above 700, reflecting the supplier's reliability in meeting payment terms. Past financial statements, including balance sheets and income statements, should demonstrate profitability margins (commonly above 10%) and efficient operational management. Furthermore, a track record of timely payment to creditors and financial institutions underscores the supplier's commitment to maintaining strong financial relationships in various sectors.
Compliance with Industry Standards and Certifications
Compliance with industry standards and certifications is essential for suppliers in sectors such as manufacturing, food safety, and electronics. Companies must adhere to regulations set by recognized organizations like ISO (International Organization for Standardization), which establishes benchmarks for quality and safety across various industries. Certifications such as ISO 9001 for quality management and ISO 22000 for food safety systems are critical indicators of a supplier's commitment to excellence. Additionally, adherence to local and international regulations, such as ASTM (American Society for Testing and Materials) for materials and EN (European Norms) standards in Europe, underscores a supplier's reliability. Compliance ensures products meet safety, efficiency, and quality requirements, crucial for maintaining consumer trust and operational integrity. Regular audits and assessments help verify ongoing conformity to these standards, fostering partnerships based on accountability and performance.
Quality Assurance and Control Processes
Quality assurance and control processes play a critical role in ensuring that products meet established standards and specifications. Organizations implementing rigorous quality assurance measures often adhere to international standards such as ISO 9001, which outlines requirements for a quality management system. Key components of an effective quality control process include systematic inspections, comprehensive testing protocols, and the use of statistical tools to analyze product performance. For instance, manufacturers may utilize Six Sigma methodologies to minimize defects and variability in production, leading to higher levels of customer satisfaction. Additionally, regular audits and assessments should be conducted to evaluate compliance with quality standards, ensuring that suppliers consistently deliver reliable and high-quality materials or products. Proper documentation of quality checks and adherence to corrective action plans are essential for maintaining standards across the supply chain.
Capacity and Scalability for Production and Delivery
Suppliers must demonstrate sufficient production capacity to meet large-scale orders, ensuring efficient delivery timelines. Facilities need to be equipped with advanced machinery and technologies to support high-volume manufacturing. Proven scalability in operations is crucial, allowing the supplier to adapt to fluctuations in order sizes and meet growing demand. Historical data showcasing previous projects, including production volumes and lead times, should be provided for assessment. Certifications relevant to quality control and operational excellence, such as ISO 9001, indicate commitment to maintaining industry standards. A robust supply chain management strategy enhances reliability in sourcing materials, preventing delays during peak production periods. Additionally, contingency plans should be in place to address potential disruptions, ensuring continual product availability.
Letter Template For Supplier Pre-Qualification Criteria Samples
Letter template of supplier pre-qualification requirements for project submission.
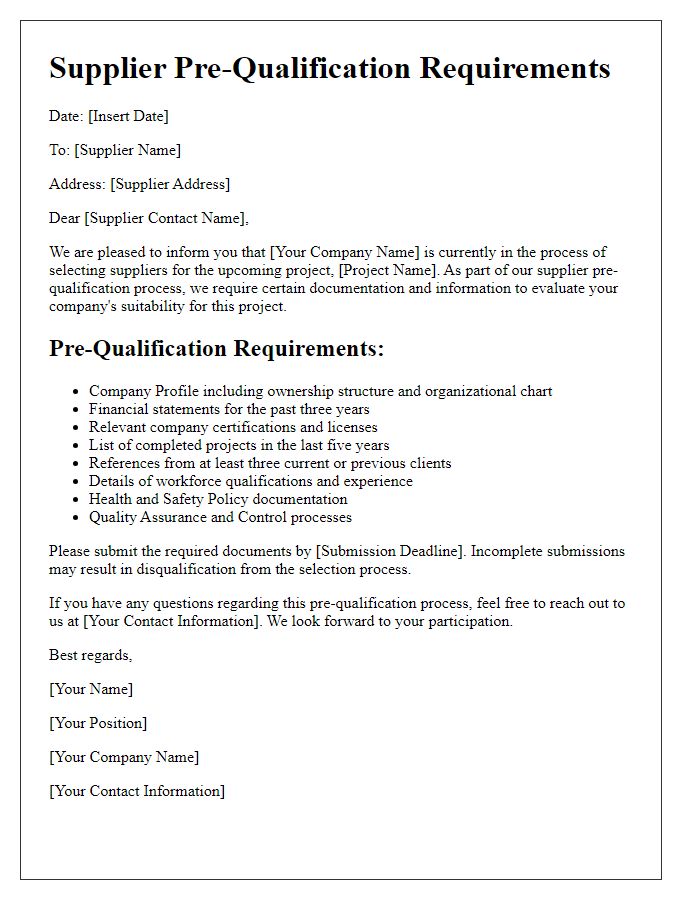
Letter template of supplier assessment criteria for bidding invitations.
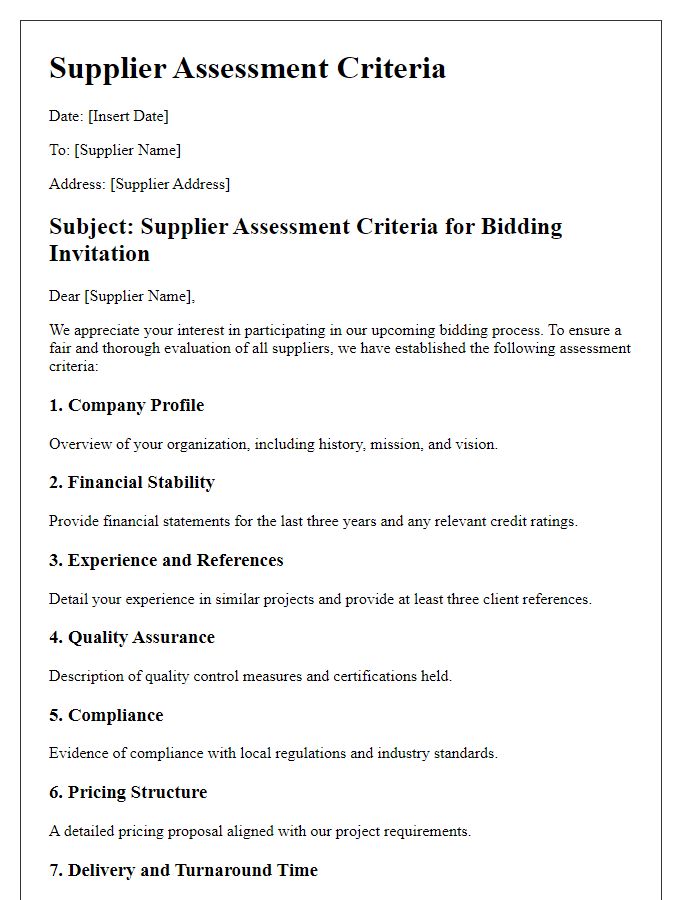
Letter template of supplier eligibility standards for partnership considerations.
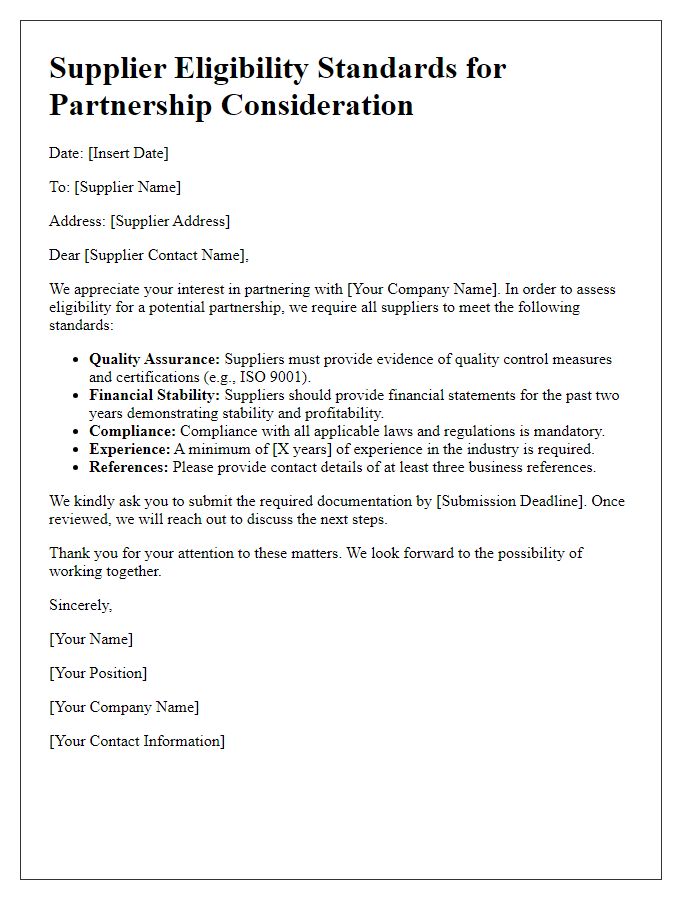
Letter template of supplier qualification guidelines for potential contractors.
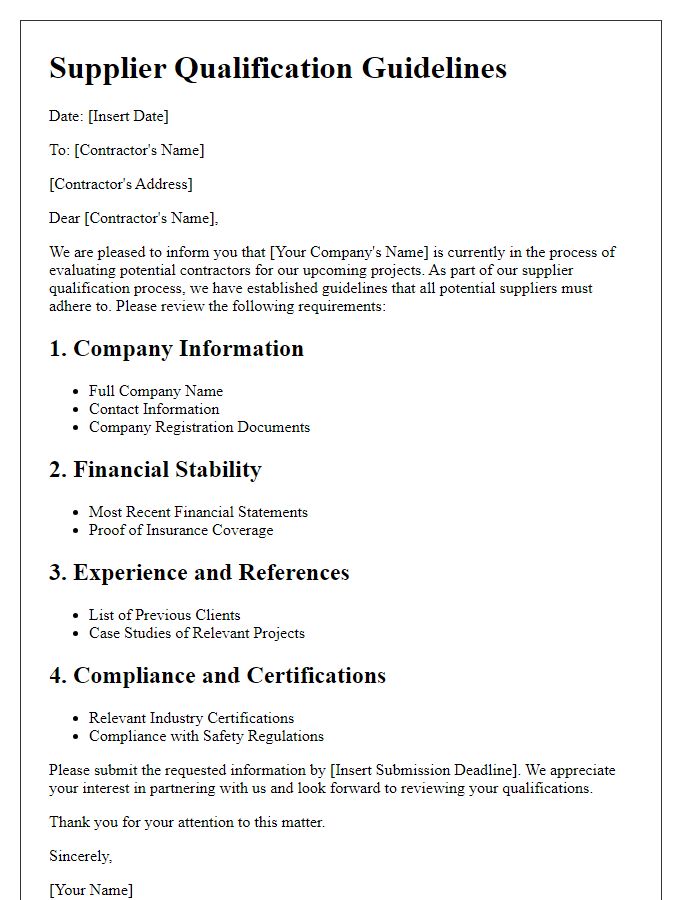
Letter template of supplier pre-screening checklist for approved vendors.
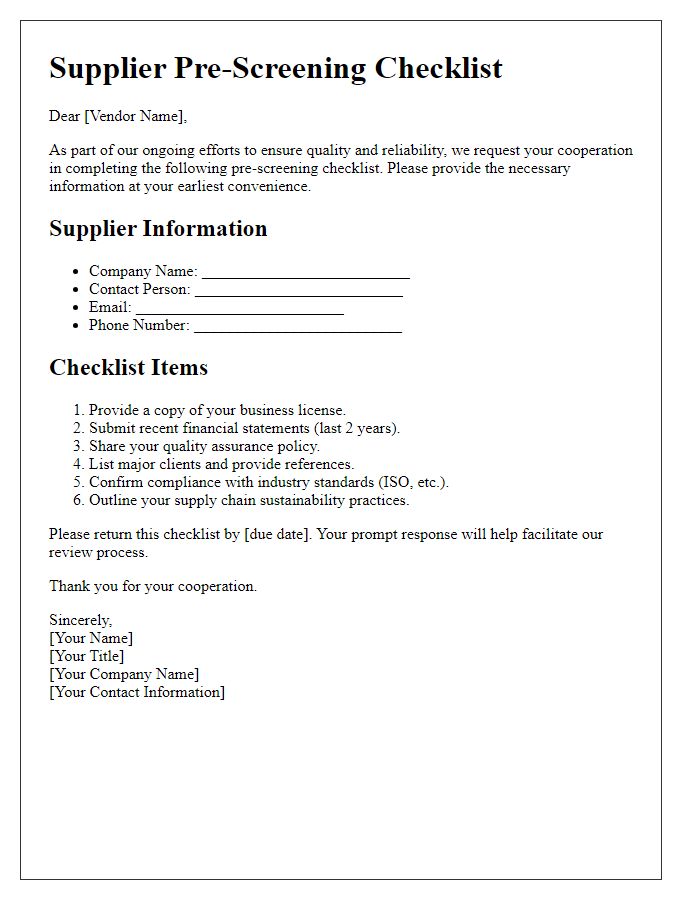
Letter template of supplier capability evaluation for procurement processes.
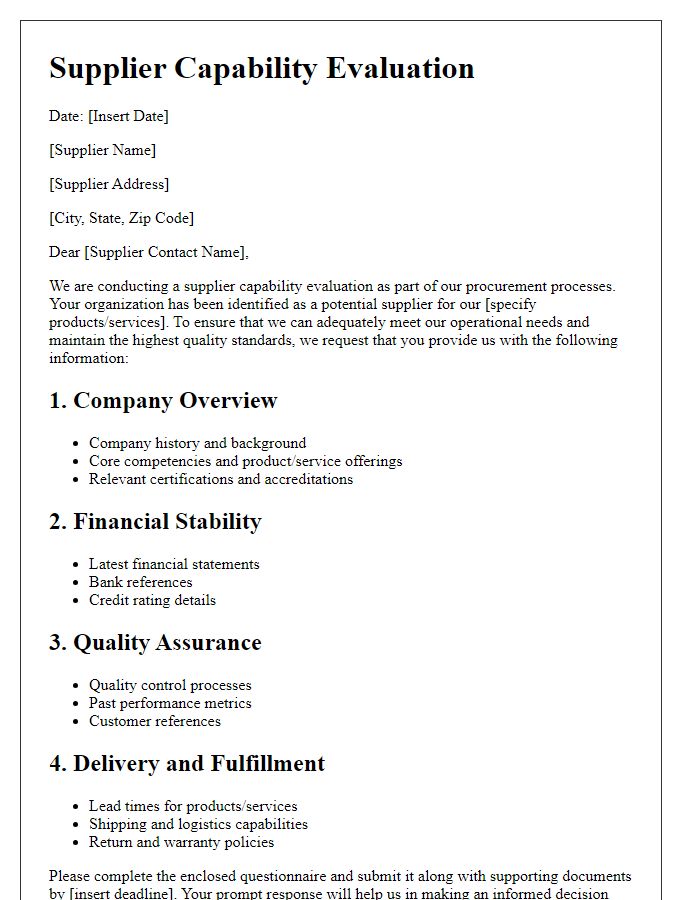
Letter template of supplier selection criteria for tender opportunities.
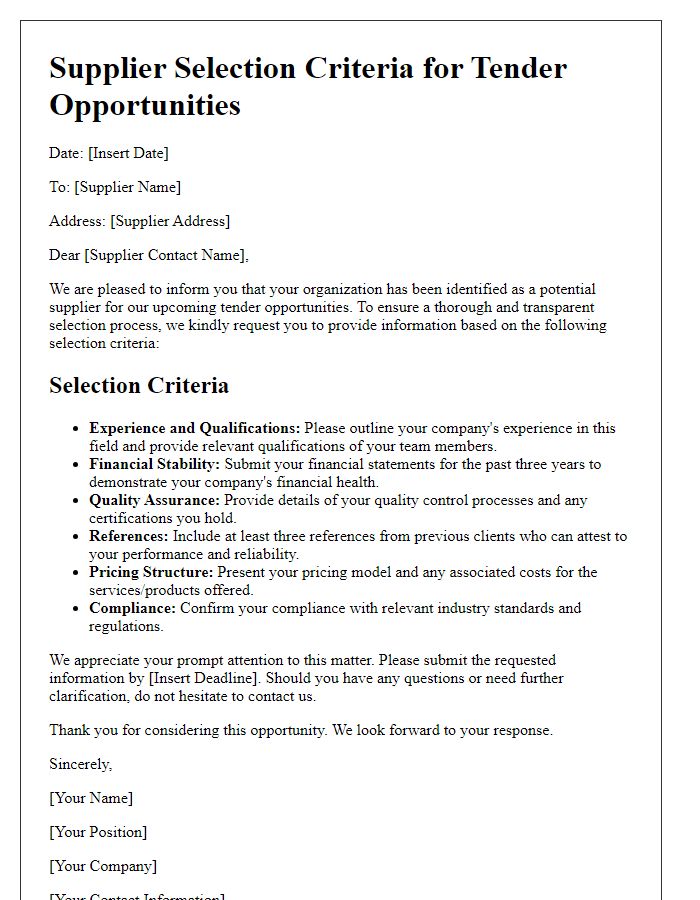
Letter template of supplier vetting procedures for compliance verification.
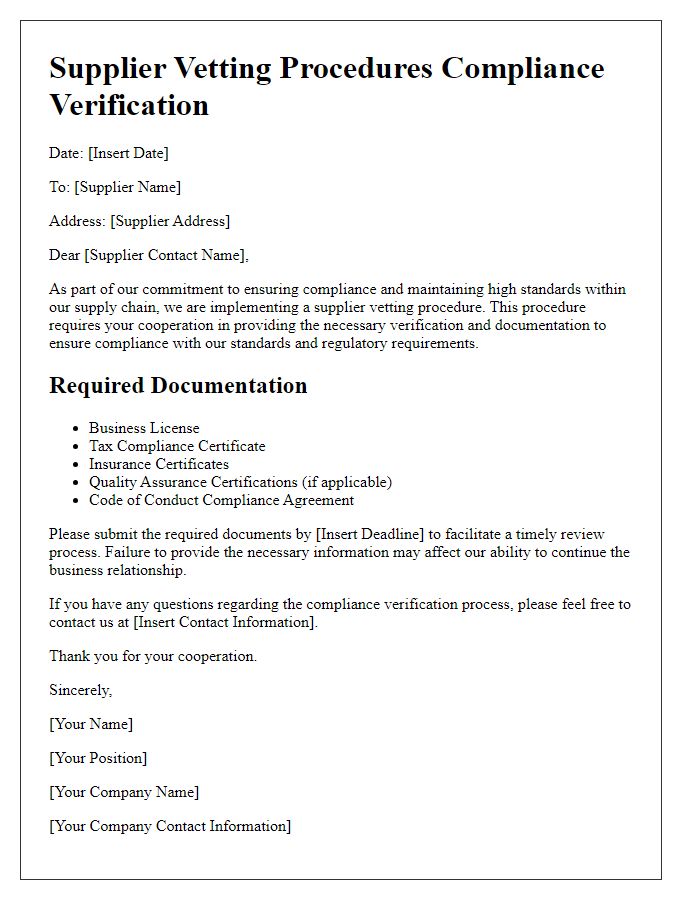
Comments