Hello there! When it comes to addressing supplier audit findings, a well-crafted response letter is essential for maintaining strong relationships and ensuring transparency. This letter should clearly outline the identified issues, your action plan to rectify them, and any steps you will take to prevent future occurrences. Engaging in this open dialogue not only demonstrates your commitment to quality but also fosters trust between parties. Ready to dive deeper into effective strategies for drafting your response?
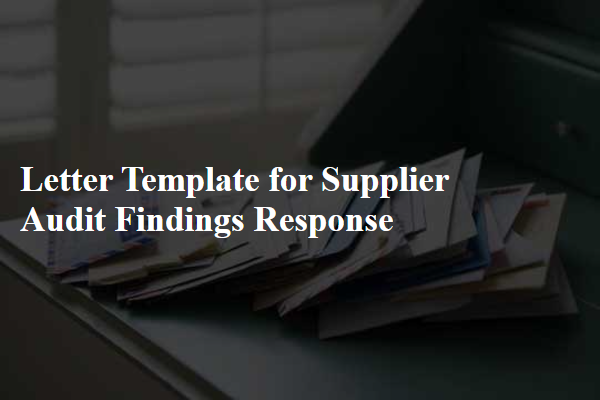
Executive Summary
The executive summary highlights key findings from the supplier audit conducted at XYZ Corporation's manufacturing facility in Q3 2023. A total of 15 major inconsistencies were identified, including non-compliance with ISO 9001:2015 quality management systems. Documentation review revealed gaps in the traceability of raw materials, affecting product integrity. Operational processes lacked adherence to standard operating procedures (SOPs), leading to inefficiencies. Employee training records indicated deficiencies, with only 60% of staff completing mandatory safety training. The audit underscored the urgent need for corrective actions to maintain supplier eligibility and align practices with industry standards. Recommendations include implementing a robust quality assurance program, enhancing training initiatives, and regular internal audits to ensure ongoing compliance.
Detailed Findings and Responses
Supplier audits often reveal crucial insights into operational efficiency and compliance standards. When addressing detailed findings from an audit, it is vital to systematically categorize each item according to severity, with explicit references to relevant industry regulations, such as ISO 9001 or specific contractual obligations. For instance, if a non-conformity involves inadequate documentation in the quality management system (QMS), the response should outline corrective actions, including implementing a revised documentation protocol by March 2024. Each finding should also include a root cause analysis, demonstrating thorough investigation efforts. Additionally, proactive measures, like scheduled training for staff and regular follow-up audits, can reassure stakeholders about the commitment to continuous improvement.
Corrective Action Plan
Supplier audits often reveal critical areas for improvement that require a structured response. The Corrective Action Plan (CAP) must address specific findings outlined during the audit process, such as non-compliance with quality standards, inadequate documentation, or failure to meet delivery timelines. For instance, if the audit identifies deviations from ISO 9001 quality management requirements, the supplier must establish a robust training program for employees to ensure adherence to these regulations. Additionally, setting measurable goals with specific timelines--like reducing defect rates by 20% within six months--can enhance accountability. Implementing regular internal audits also allows for ongoing monitoring, fostering a culture of continuous improvement. The designated point of contact should be responsible for tracking progress and reporting updates to the relevant stakeholders, ensuring transparency throughout the corrective action process.
Preventive Measures
Preventive measures for supplier audit findings focus on ensuring compliance and improving operational efficiency. Regular training sessions for employees on quality control standards can minimize errors. Implementation of a robust supplier performance monitoring system aids in early detection of potential issues. Conducting bi-annual audits ensures adherence to industry regulations and internal protocols. Establishing a feedback loop with suppliers fosters open communication, allowing for quick resolution of discrepancies. Risk assessment procedures should be updated quarterly to identify and mitigate future risks. Documentation practices need enhancement to ensure traceability of materials and processes, minimizing discrepancies in inventory management.
Timelines and Responsibilities
Timelines and responsibilities are critical elements in addressing supplier audit findings effectively. The corrective action plan outlines specific measures to remediate identified deficiencies within stipulated timeframes. Each task is assigned to designated team members who will ensure accountability and track progress. For example, a finding related to non-compliance with safety standards may have a deadline of 30 days for resolution, while another concerning documentation errors might be given a 14-day timeframe for correction. Regular progress meetings will be scheduled weekly to review advancements and adjust responsibilities as needed. Timely communication with the supplier regarding updates and expectations will strengthen the partnership and facilitate compliance with agreed-upon standards.
Comments