When it comes to ensuring safety in the workplace, having a solid hazard communication plan is essential, especially when working with suppliers. This step-by-step guide is designed to help you create an effective plan that covers all bases, from understanding Material Safety Data Sheets (MSDS) to proper labeling protocols. By prioritizing clear communication and training, you can foster a safer environment for everyone involved. Curious to learn more about developing a robust hazard communication strategy? Let's dive in!
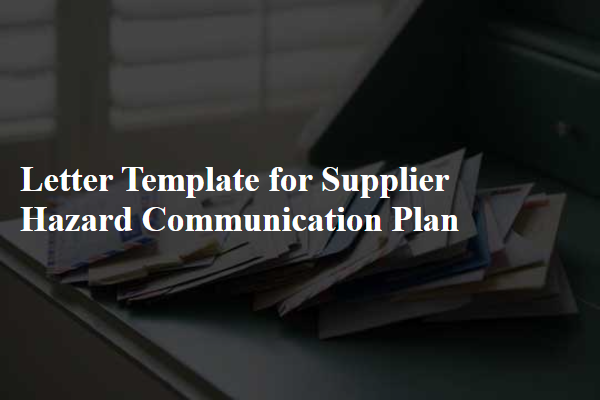
Compliance with regulations
A comprehensive supplier hazard communication plan is essential for ensuring compliance with Occupational Safety and Health Administration (OSHA) regulations, specifically Standard 29 CFR 1910.1200. This plan requires suppliers to provide Safety Data Sheets (SDS) for hazardous chemicals, detailing information such as toxicity levels, first aid measures, and proper handling procedures. Each hazardous substance, identified by the Globally Harmonized System (GHS) symbols, must be clearly labeled to communicate risks effectively to employees and emergency responders. Training programs for staff must educate them on recognizing these labels and understanding the SDS, facilitating a safer workplace environment. Regular audits and updates to the communication plan ensure ongoing compliance and enhancement of safety protocols in accordance with local and federal laws governing chemical safety.
Supplier contact information
Suppliers often provide critical components, materials, or services in industries such as manufacturing, construction, or chemical production. Supplier contact information typically includes the name of the supplier organization, physical address (including city and state for proper identification), phone number for immediate communication, email address for official correspondence, and website URL for access to more detailed information on products and services. Additionally, including key contacts at the supplier, such as account managers or safety officers, can facilitate effective communication regarding hazard communication plans. Providing comprehensive contact details ensures swift responses in emergencies related to hazardous materials or compliance with safety regulations.
Hazard identification and assessment
A comprehensive Hazard Communication Plan is essential for ensuring workplace safety within supply chain operations. This plan must include detailed hazard identification and assessment processes for various substances, including chemical agents (like solvents or acids) and physical hazards (such as toxic dust or sharp objects). For chemical agents, Material Safety Data Sheets (MSDS) should be maintained for each chemical, outlining potential hazards, exposure limits, and appropriate handling procedures. OSHA regulations (Occupational Safety and Health Administration) provide guidelines for evaluating risks associated with hazardous materials in the workplace. The assessment process will also incorporate employee training sessions on recognizing hazards and proper response protocols, ensuring compliance with safety standards. Regular audits should be scheduled to review hazard assessments, using a log to track any new hazards identified, alongside corrective actions taken in response to emerging risks.
Safety data sheets (SDS)
A well-structured supplier hazard communication plan is pivotal for maintaining workplace safety regarding hazardous substances. Safety Data Sheets (SDS), mandated by OSHA (Occupational Safety and Health Administration), provide essential information about chemical properties, health hazards, and handling precautions. Each SDS must contain 16 standardized sections, detailing critical information such as toxicity levels, first aid measures, storage requirements, and protective measures during handling. Compliance with the GHS (Globally Harmonized System of Classification and Labelling of Chemicals) ensures that labeling and SDS formats are consistent across different suppliers, enhancing readability and comprehension for users. Regular training on SDS interpretation is necessary for employees to understand potential risks, ensuring effective communication regarding the safe use of chemicals in the workplace.
Emergency response procedures
Emergency response procedures are critical for effectively managing hazardous situations in the workplace, particularly in industries dealing with chemicals. Clear communication channels should identify key personnel responsible for emergency response roles, such as Safety Officer and Emergency Coordinator. Regular training sessions (at least biannually) help staff understand the proper protocols. In case of a chemical spill, use the Material Safety Data Sheet (MSDS) specific to the hazardous substance for guidance on containment and cleanup. Ensure emergency contact numbers (local fire department, poison control) are prominently displayed throughout the facility. Conduct regular drills simulating emergencies (e.g., chemical leaks, fires) to reinforce readiness and ensure compliance with Occupational Safety and Health Administration (OSHA) standards. Identify designated evacuation routes and assembly points for personnel safety. Inventory of emergency equipment, such as first-aid kits and fire extinguishers, must be conducted monthly to ensure availability during emergencies.
Comments