Are you looking to enhance your supplier relationships and ensure the highest quality products for your business? In todayâs competitive market, effective communication is key, and a well-crafted letter can make all the difference in initiating quality improvements. By addressing specific concerns and outlining clear expectations, you foster collaboration and drive positive change with your suppliers. Dive into our detailed guide on crafting the perfect supplier quality improvement request letter to elevate your partnerships and achieve optimal results!
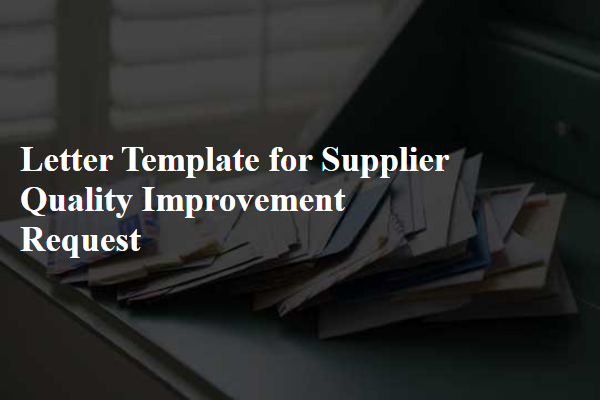
Clear identification of quality issues
A thorough assessment revealed several critical quality issues with the supplied components from the manufacturing facility, located in Dongguan, China. In batches produced during March 2023, approximately 15% of items exhibited defects, including incorrect dimensions (over 3 millimeters variance from specifications), surface imperfections (noted in over 20% of units), and inconsistent material composition (varied from required ISO standards). These quality lapses impact product performance and customer satisfaction, affecting ongoing contracts with key clients in the automotive sector. Immediate collaboration is essential to establish corrective actions, enforce stringent quality control measures, and adhere to scheduled delivery timelines.
Specific performance metrics
Supplier quality improvement requests often focus on specific performance metrics crucial for ensuring product reliability and customer satisfaction. Key performance indicators such as defect rates (measured in parts per million, ppm), on-time delivery percentages (aiming for 95% or higher), and adherence to specifications (evaluated through tolerances in dimensions or material composition) form the basis of quality assessments. Additionally, metrics like customer complaint rates (tracked over a specific period) and the effectiveness of corrective actions (evaluated by follow-up audits) are essential for gauging supplier performance. These detailed metrics serve as benchmarks for ongoing evaluation and improvement initiatives, ensuring that suppliers align with desired quality standards and contribute to overall production excellence.
Detailed improvement expectations
Supplier quality improvement requests require precise articulation of expectations. Clear documentation outlining specific improvement areas is essential for effective communication. Key aspects include the identification of quality metrics, such as defect rates--ideally targeting a reduction to below 2%--and the adherence to agreed-upon delivery schedules within a timeframe of 48 hours. Specific processes, such as regular audits at a frequency of every three months, should be established to assess compliance with quality standards (like ISO 9001). Furthermore, implementing a corrective action plan following identified discrepancies ensures continuous improvement. Establishing a feedback loop allows for ongoing assessment of supplier performance regarding product consistency and reliability, fostering a collaborative environment aimed at enhancing overall quality.
Timeline for corrective actions
Suppliers play a crucial role in the overall quality of products manufactured in various industries, such as automotive, electronics, and consumer goods. A well-structured timeline for corrective actions is essential for addressing quality issues effectively. Initial assessment of the defect's root cause should take one week, allowing suppliers to gather data and analyze production processes. Following this, a corrective action plan should be developed within two weeks, detailing specific steps, resources, and responsibilities. Implementation of the corrective actions should be allotted a three-week timeframe, ensuring that modifications to processes or materials are thoroughly executed. Finally, a follow-up evaluation period of one month is necessary to verify the effectiveness of the corrective actions and ensure sustained improvements in quality. Regular communication between suppliers and manufacturers throughout this timeline is crucial for successful resolution of quality issues.
Consequences for non-compliance
Failure to comply with quality standards can have serious consequences for suppliers in the automotive industry, including financial penalties (up to 10% of contract value), loss of contracts resulting in reduced revenue, and damage to reputation that can impact future business opportunities. Non-compliance may also lead to product recalls (which can cost millions of dollars) and increased scrutiny from regulatory agencies such as the National Highway Traffic Safety Administration (NHTSA). Frequent quality issues can create strain on relationships with Original Equipment Manufacturers (OEMs) and may necessitate extensive corrective action plans, diverting valuable resources. Ultimately, consistent non-compliance can jeopardize a supplier's market position, leading to diminished competitiveness and long-term sustainability.
Comments