When it comes to ensuring a safe and productive work environment, providing the right protective equipment for contractors is essential. This not only safeguards their health but also enhances overall project efficiency. In this article, we'll explore the key elements you need to consider when equipping your contractors properly. So, if you're ready to create a safer workplace, keep reading to discover best practices and essential tips!
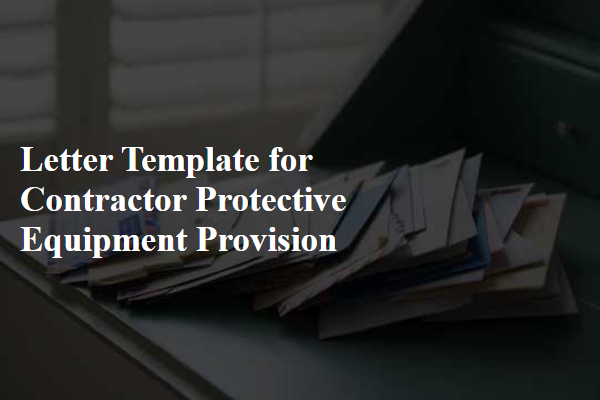
Contractor Company Information
Contractor companies play a vital role in ensuring workplace safety through the provision of protective equipment. Personal protective equipment (PPE) includes essential gear such as helmets, gloves, eye protection, and safety boots. Compliance with safety regulations (for example, OSHA in the United States) necessitates that contractors equip their workers with adequate PPE to mitigate risks associated with hazardous environments. Proper training programs enhance the effective use of provided equipment, ensuring that employees at construction sites in locations like New York or Los Angeles remain safe from potential injuries. Monitoring and regularly updating the inventory of PPE not only guarantees availability but also ensures that the equipment meets the latest safety standards.
Recipient Details
Contractor protective equipment provision involves the allocation of essential safety gear for construction and industrial activities, ensuring worker safety across various environments. Specific equipment includes hard hats (for head protection), safety goggles (to shield eyes from debris), high-visibility vests (for visibility in low-light conditions), and steel-toed boots (to protect feet from heavy objects). Legal frameworks, such as OSHA regulations in the United States, mandate the provision of these safety items, with penalties for non-compliance. The process typically requires detailed assessments of on-site hazards in locations like construction zones, factories, or remote job sites, ensuring that all personnel have access to the appropriate protective gear tailored to the risks associated with their specific tasks.
Description of Protective Equipment
Contractor protective equipment includes items designed to ensure safety in various work environments. Personal Protective Equipment (PPE) such as hard hats (ANSI Z89.1 compliant, designed to protect against head injuries from falling objects) should be provided. Safety goggles (ANSI Z87.1-2015 certified) are essential for protecting the eyes from flying debris or chemical splashes. High-visibility vests increase visibility in low-light conditions, particularly in construction zones or on roadways. Steel-toed boots (with ASTM F2413-18 certification) safeguard against foot injuries from heavy materials. Respirators (NIOSH-approved) are critical in environments with airborne contaminants or insufficient oxygen levels. Gloves appropriate for the specific hazards--such as cut-resistant or chemical-resistant gloves--must also be included to protect hands during various tasks. Other equipment may include ear protection (with noise reduction ratings suitable for loud environments), harnesses, and lanyards for fall protection when working at heights, ensuring comprehensive safety measures for all contractors involved.
Compliance with Safety Regulations
Contractors must adhere to safety regulations regarding protective equipment. Personal Protective Equipment (PPE) such as hard hats, safety goggles, gloves, and reflective vests are essential on construction sites like those in New York City, which has strict OSHA standards. Compliance with these regulations reduces workplace injury rates (which can average over 100,000 annually in the construction sector) and ensures the safety of workers. Regular training and inspections (recommended at least monthly) help maintain adherence to safety protocols, with documentation required to prove ongoing compliance. Non-compliance can lead to fines, increased insurance rates, or project delays impacting timelines significantly.
Contact and Support Information
Providing contractors with appropriate protective equipment is essential for workplace safety and compliance with Occupational Safety and Health Administration (OSHA) standards. This equipment includes items like hard hats, safety goggles, and steel-toed boots, which are critical for protecting against workplace hazards. Contractors should be informed about contact and support resources available for any questions or concerns regarding equipment maintenance or replacements. For instance, obtaining equipment supplier contact details or safety officer support lines can streamline communication, ensuring contractors have immediate access to assistance for any protective gear-related issues.
Comments