Are you gearing up for an inventory audit but unsure where to start? Itâs essential to set the stage with a well-structured letter that outlines your audit process and expectations clearly. A good inventory audit report not only helps in identifying discrepancies but also streamlines your future inventory management practices. Ready to dive deeper into crafting the perfect letter template? Letâs explore the key elements together!
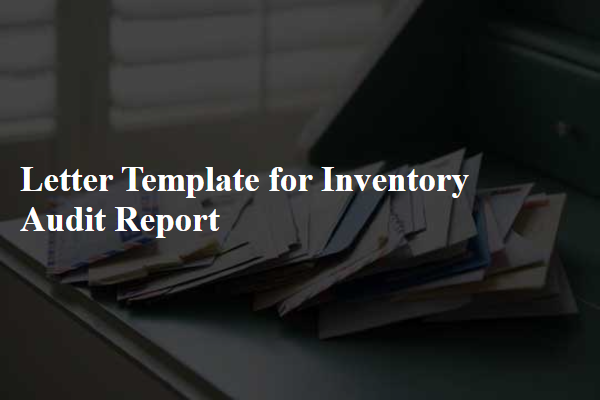
Introduction
An inventory audit report serves as a critical assessment tool for organizations aiming to evaluate their stock levels and management practices. This detailed document analyzes the accuracy and completeness of inventory records, conducted periodically, often on a quarterly or annual basis, to ensure compliance with accounting standards and internal policies. The report highlights discrepancies between recorded inventory on hand and physical counts, often leading to necessary adjustments in financial statements and future stock assessments. It typically includes information on inventory turnover rates, valuation methods, and recommendations for improving inventory management systems at locations like warehouses or retail outlets, ensuring efficient operations and minimizing losses due to shrinkage or obsolescence. An effective inventory audit is vital for optimizing resource allocation and enhancing overall business performance.
Methodology
The inventory audit report methodology encompasses a systematic approach to evaluating stock accuracy and integrity within the warehouse (specific location details may vary). The process includes initial planning, including defining the auditing objectives and the scope of the inventory (specific items or categories, e.g., electronics, perishables). Data collection methods incorporate physical counts and verification techniques, ensuring alignment with financial records dated at the end of the fiscal quarter. Sampling methods, such as selective or random sampling, may be employed to ensure comprehensive coverage of inventory items (e.g., reviewing 10% of the total stock). Post-audit analysis facilitates identification of discrepancies or shrinkage, allowing for corrective actions to be documented thoroughly. The final report will provide findings and recommendations based on collected data, ultimately leading to improved inventory management practices and reduced operational risks.
Key Findings
The inventory audit report for the fiscal year ending December 31, 2023, revealed several key findings that warrant attention for operational improvements and financial accuracy. The total value of inventory, amounting to $2.5 million across multiple product categories, showed discrepancies in the physical counts versus recorded figures, with a 10% variance identified. Notably, the electronics segment, representing approximately $1 million, demonstrated the highest discrepancies, particularly in popular items like smart TVs and smartphones. Seasonal items, such as holiday decorations, exhibited slower turnover rates, resulting in excess stock valued at around $500,000. Additionally, the audit identified a lack of consistent labeling and organization within the warehouse located in Springfield, leading to processing delays and inefficiencies. Enhanced inventory management practices and system updates will be crucial to mitigate these issues moving forward.
Recommendations
Inventory audits are crucial for maintaining accurate stock records in businesses, including retail and warehouse operations, leading to improved efficiency and reduced losses. Implementing a robust inventory management system (like SAP or Oracle) can streamline tracking, ensuring real-time updates on product levels. Conducting frequent physical counts, ideally quarterly or biannually, helps identify discrepancies between recorded and actual stock, enhancing accuracy. Training staff on best practices in inventory handling and management reduces errors and fosters accountability. Establishing a clear process for reporting damages, losses, or discrepancies promotes transparency. Utilizing advanced technologies such as barcode scanning and RFID systems can significantly enhance tracking speed and accuracy, minimizing human error. Regularly reviewing inventory turnover rates (ideally every month) helps identify slow-moving items, enabling strategic decisions on markdowns or promotions to manage excess stock.
Conclusion
An effective inventory audit report conclusion provides a clear summary of findings, highlighting discrepancies or areas of concern regarding stock levels and management practices. The examination of inventory data, which may include quantitative figures like total assets or variances in expected versus actual counts, reveals critical insights into the operational efficiency of the business. Identified issues may stem from factors such as inaccurate record-keeping, employee training gaps, or outdated inventory management systems. Recommendations for improvement can encompass implementing real-time tracking technologies, enhancing employee training programs, or revising inventory rotation practices. Addressing these areas may significantly enhance inventory accuracy, reduce losses, and improve overall financial health.
Comments