In todayâs fast-paced world, we sometimes fall short of expectations, and thatâs perfectly human. If you've received a letter of apology regarding a missed commitment or subpar delivery, itâs essential to understand the sentiments behind it. A heartfelt acknowledgment of mistakes not only fosters trust but also sets the stage for a stronger relationship moving forward. Join me as we delve into the nuances of crafting the perfect apology letter that restores confidence and encourages open communication.
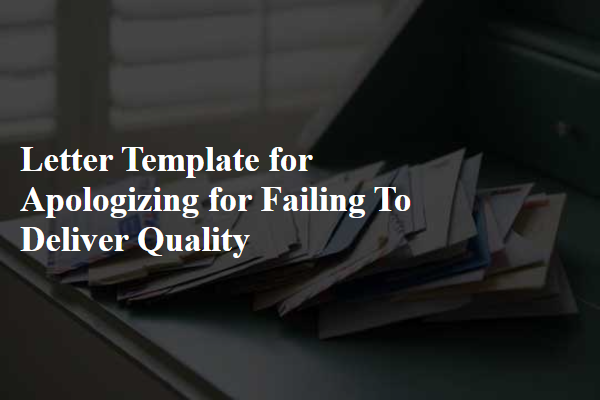
Acknowledgment of the Issue
Our company recognizes a significant decline in quality regarding recent product deliveries. Customers expected high standards, typical of our brand, particularly in products such as the Elite 3000 series, renowned for durability and performance. Complaints have surfaced from locations such as New York and Los Angeles, highlighting inconsistencies in functionality and design. Affected items, including the premium battery packs, failed rigorous quality assurance tests (with some units recording defects rates as high as 15%). Feedback indicates a breach of trust, as our commitment to excellence was not upheld. A full investigation into manufacturing processes is underway, with the goal to restore customer faith in our products and services.
Sincere Apology Statement
A sincere apology statement can address the impact of failing to deliver quality service or product, acknowledging specific instances of disappointment experienced by customers. Acknowledging the importance of quality assurance in maintaining trust and customer satisfaction is crucial. Providing details about the affected product or service, such as a specific model number or order date, can help clarify the context. Outlining immediate actions taken to rectify the situation, like quality control enhancements or staff retraining programs, also demonstrates a commitment to improving performance. Ensuring customers feel valued through earnest communication can foster goodwill and pave the way for future positive interactions.
Explanation of Situation
In product manufacturing, quality control plays a crucial role in ensuring that items meet customer expectations. Recent production errors have resulted in substandard products being delivered to clients. These quality issues were traced back to a malfunctioning assembly line machinery at our facility in Springfield. Reports indicated that over 200 units, produced between March 1 and March 15, showed defects in their finish, leading to a dissatisfied customer base. Internal investigations confirmed that a failure in the quality assurance protocols allowed these faulty products to be shipped without adequate inspection. Immediate steps have been taken to rectify these issues, including a comprehensive review of all machinery and revising quality control measures to prevent future occurrences.
Assurance of Corrective Action
High-quality standards are essential in manufacturing processes, especially in industries like aerospace, where safety and reliability are paramount. In a recent project for a commercial aircraft model, a production fault led to substandard components being delivered. The quality control inspection identified over 200 non-conforming parts, specifically in the wing assembly section. This situation necessitates immediate corrective actions, including a thorough review of supplier materials, updated training for quality assurance personnel, and the implementation of stricter inspection protocols. Future compliance will be reinforced through quarterly audits to ensure adherence to aerospace specifications. A dedicated team, comprising engineers and quality specialists, will oversee these corrective measures to restore confidence and maintain our commitment to excellence.
Offer of Recompense or Future Commitment
Failing to meet quality standards significantly impacts business relationships and customer trust. Instances of subpar products or services can lead to dissatisfaction among clients, ultimately affecting brand reputation. A sincere apology is necessary to acknowledge the oversight and restore confidence. Offering a recompense, such as discounts or refunds, compensates for the loss experienced. Additionally, a commitment to quality improvement emphasizes dedication to customer satisfaction. Implementing new quality control measures and providing regular updates on progress can reassure clients of future reliability and service excellence.
Letter Template For Apologizing For Failing To Deliver Quality Samples
Letter template of acknowledgment for failing to meet quality standards.
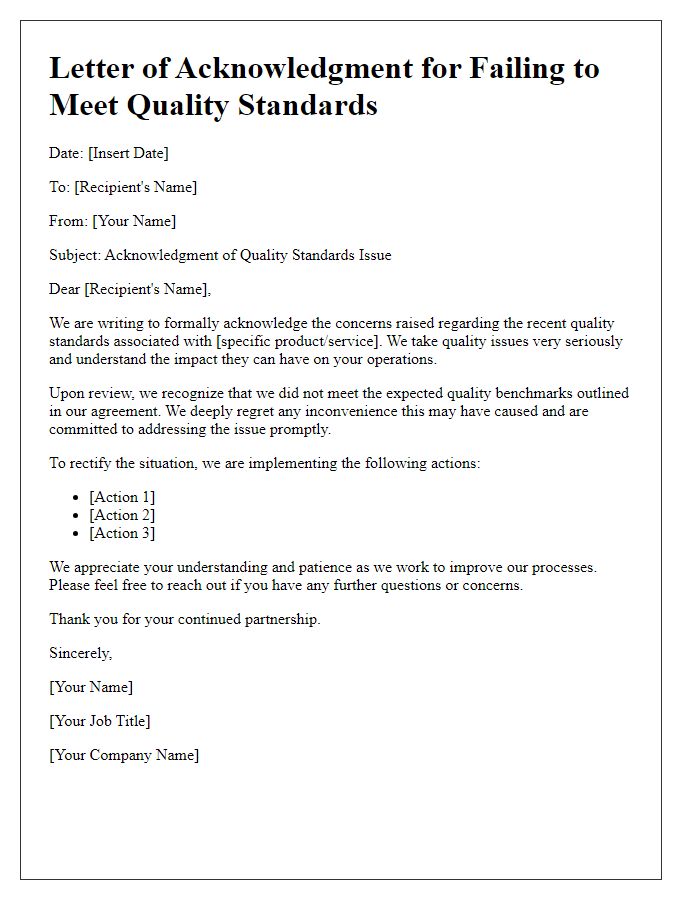
Comments