Are you struggling to ensure the highest quality standards for the products you receive from suppliers? Itâs vital for any business to maintain robust quality assurance processes to build trust and uphold brand reputation. In this article, we'll explore effective letter templates designed to communicate your quality expectations and foster stronger supplier relationships. Dive in to discover how to elevate your supplier communications and ensure product excellence!
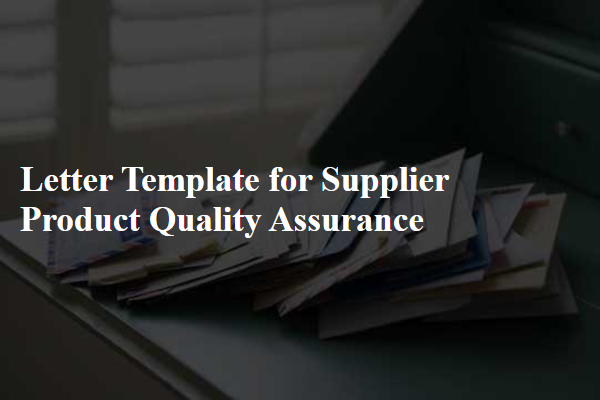
Supplier contact information
Supplier contact information is crucial for effective communication regarding product quality assurance. Essential details include the supplier's name, which identifies the company; address, providing the physical location for correspondence; telephone number, ensuring direct contact for inquiries; email address, facilitating timely communication; and contact person name, identifying the individual responsible for quality assurance matters. Accurate and up-to-date supplier contact information enhances clarity and efficiency in resolving quality-related issues and fostering positive supply chain relationships.
Product specifications
Product specifications for quality assurance are essential in maintaining high standards for supplier-manufactured items. Specifications detail requirements such as dimensions, materials, and performance standards that must be met for products like electronic components, textiles, or automotive parts. For instance, dimensions might require tolerances of +-0.01 millimeters for precision machined parts, while materials could specify Grade A aluminum for durability. Compliance with industry standards such as ISO 9001 ensures adherence to quality management principles. Additionally, individual specifications might include certifications like CE marking for electronic goods sold within the European market, indicating conformity with safety, health, and environmental protection standards. Tracking and documenting these product specifications helps in maintaining consistent quality and eliminating defects in the supply chain.
Quality standards and guidelines
High-quality product standards are essential in maintaining trust between suppliers and manufacturers. The Quality Management System (QMS) outlines stringent requirements to ensure consistency and compliance in deliverables. These guidelines include parameters like material specifications, manufacturing processes, and performance attributes relevant to industries such as automotive or electronics. Adherence to international standards, such as ISO 9001, mandates regular audits and inspections to validate conformity. The inclusion of defect rates, which should ideally remain below 1% for critical components, emphasizes the importance of quality control measures. Understanding customer satisfaction metrics through regular feedback loops further enhances product reliability and market competitiveness.
Inspection and testing procedures
In a robust product quality assurance framework, inspection and testing procedures play a pivotal role in ensuring that goods meet specified standards. For manufacturers and suppliers alike, implementing stringent measures is essential. Visual inspections should occur at various stages, with a focus on identifying defects in raw materials or finished products. Utilizing advanced testing methods, such as Non-Destructive Testing (NDT), can enhance the detection of internal flaws without damaging the product, particularly in industries like aerospace and automotive. Statistical Process Control (SPC) techniques can monitor production quality by analyzing data from random sampling, allowing early identification of variations in the manufacturing process. Documentation of each inspection and test provides traceability, a vital aspect of compliance with standards like ISO 9001 or industry-specific regulations. Frequent audits of these procedures ensure adherence and continuous improvement in quality management systems.
Reporting and feedback mechanisms
In product quality assurance, robust reporting and feedback mechanisms play a critical role in maintaining standards. Regular inspection protocols, such as rigorous testing intervals, ensure adherence to specifications, such as dimensions and material properties (e.g., tensile strength in Newtons). Utilizing data management systems, suppliers can efficiently track defects (typically under 1% acceptable threshold) and customer complaints, categorizing them to identify patterns and areas for improvement. Response times to feedback should be swift, ideally within 48 hours, emphasizing customer satisfaction and continuous enhancement of quality control processes. Scheduled audits, held semi-annually at facilities, help verify compliance with industry standards like ISO 9001. Ultimately, effective communication channels, including digital platforms for real-time updates and reporting, foster collaborative problem-solving and drive quality excellence across the supply chain.
Letter Template For Supplier Product Quality Assurance Samples
Letter template of supplier quality assurance request for product compliance
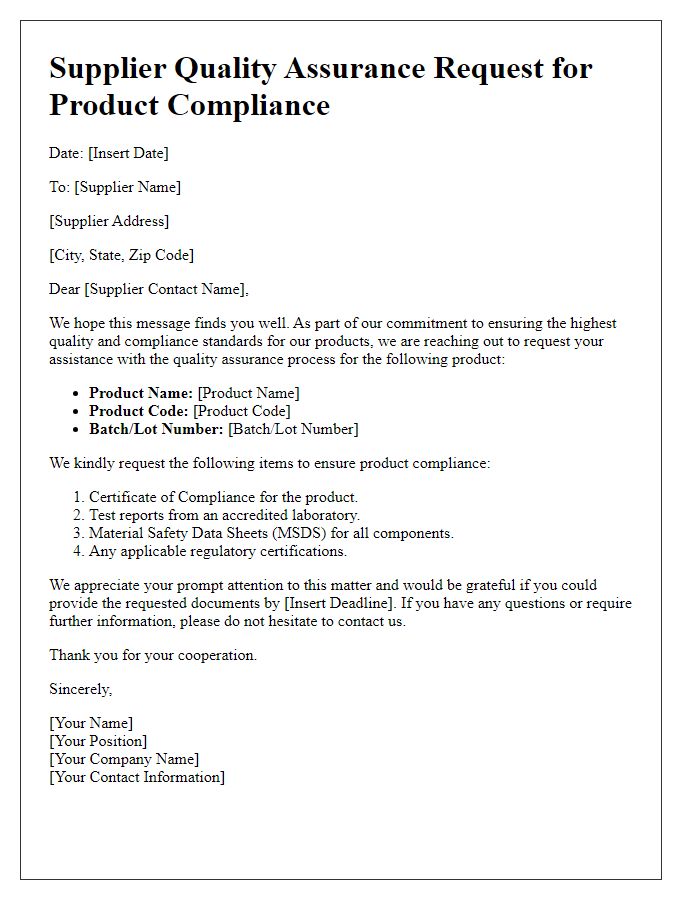
Letter template of supplier corrective action request for quality improvements
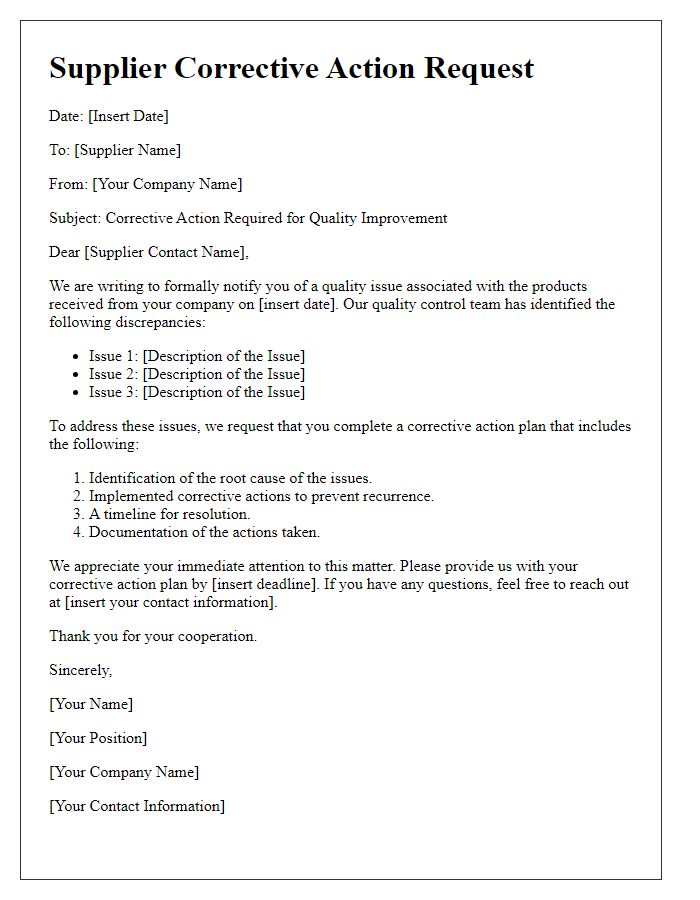
Comments