When establishing a solid partnership, outlining quality standards in a vendor agreement is essential. It ensures that both parties clearly understand expectations and maintain a consistent level of excellence. By addressing these standards in your agreement, you set the stage for a successful collaboration that benefits everyone involved. Ready to dive deeper into crafting the perfect vendor agreement?
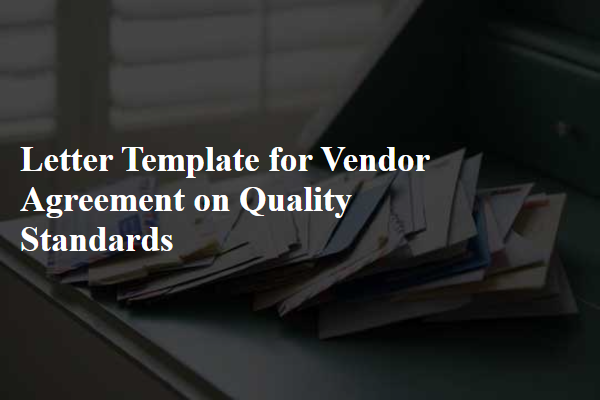
Clear definition of quality standards and expectations.
A vendor agreement on quality standards must include a detailed definition of quality benchmarks. These benchmarks should align with industry standards and specific requirements for production, such as ISO 9001, which outlines effective quality management systems. Key performance indicators (KPIs) for acceptable quality levels could include defect rates, compliance percentages, and on-time delivery metrics. Clear expectations should be set regarding materials used, production processes, and testing procedures, ensuring that the products meet specified durability and safety regulations. It is crucial to outline the consequences of failing to meet these standards, including potential penalties, product returns, and termination of the agreement. Regular quality inspections and audits should be scheduled, promoting ongoing compliance and collaboration between the vendor and the contracting party, establishing a solid foundation for partnership.
Compliance with industry regulations and certification.
Vendor agreements must include stringent quality standards to ensure compliance with industry regulations and certifications crucial for product integrity. Quality assurance protocols often align with ISO 9001 standards, which dictate comprehensive management systems for adherence to quality policies. Specific certifications, such as AS9100 for aerospace and FDA standards for food safety, require meticulous documentation and regular audits to validate compliance. Testing facilities, equipped with advanced technology, must conduct periodic evaluations on materials and processes to mitigate risks and enhance product reliability. Adopting these quality standards not only safeguards consumer safety but also fosters trust and transparency in supplier relationships.
Detailed inspection and testing procedures.
A comprehensive vendor agreement focusing on quality standards mandates specific detailed inspection and testing procedures. These procedures ensure the delivered products, such as electronics or textiles, meet predefined quality benchmarks. Every batch received undergoes rigorous dimensional checks against blueprints, with tolerances maintained within 0.01 millimeters for precision components. Visual inspections involve a 10% random sampling method, assessing for any defects under controlled lighting conditions. Additionally, destructive testing processes, like tensile strength tests conforming to ASTM standards, evaluate the durability of materials used. Documentation of these inspections requires a quality assurance report, outlining findings and corrective actions taken for non-compliance, ensuring accountability and transparency in the vendor relationship.
Penalties and remediation for non-compliance.
Vendor agreements on quality standards necessitate clear stipulations regarding penalties and remediation for non-compliance to ensure accountability and maintain product integrity. Specific penalties can include financial deductions ranging from 5% to 20% of the total contract value for repeated breaches within a fiscal quarter. Non-compliance incidents must be documented in a quality assurance log at the vendor's facility, providing a transparent record of infractions. In cases of severe non-compliance, the agreement may allow for immediate termination of the contract, particularly if product recalls or safety violations related to materials sourced from the vendor are implicated. Remediation efforts must be timely, requiring corrective action plans submitted within 10 business days from the notice of non-compliance, detailing specific measures taken to address quality issues and prevent recurrence. Regular audits and inspections, scheduled quarterly, can further uphold quality standards and reduce risk in the supply chain.
Communication and reporting protocols.
A vendor agreement focusing on quality standards involves clear communication and reporting protocols to ensure compliance and accountability. Quality Control (QC) measures, established by organizations like ISO (International Organization for Standardization), mandate regular audits for adherence to required specifications. Vendors must submit detailed reports outlining performance metrics, defect rates, and corrective actions taken within predetermined timeframes, typically on a monthly or quarterly basis. Communication channels, such as designated liaisons or dedicated email addresses, should facilitate timely exchanges of feedback between parties. Additionally, any quality breach incidents must trigger immediate notification processes, allowing for quicker resolution and maintaining standards expected by the clients. Compliance to these protocols is essential in industries such as manufacturing or food production, where quality directly impacts consumer safety and satisfaction.
Letter Template For Vendor Agreement On Quality Standards Samples
Letter template of vendor agreement regarding quality assurance measures
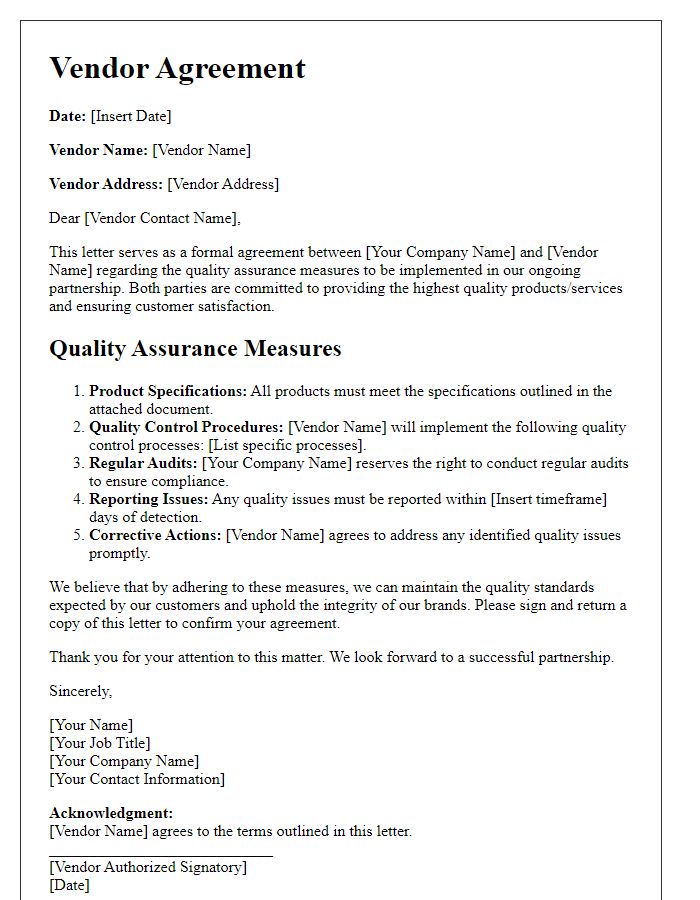
Letter template of vendor agreement focusing on product quality expectations
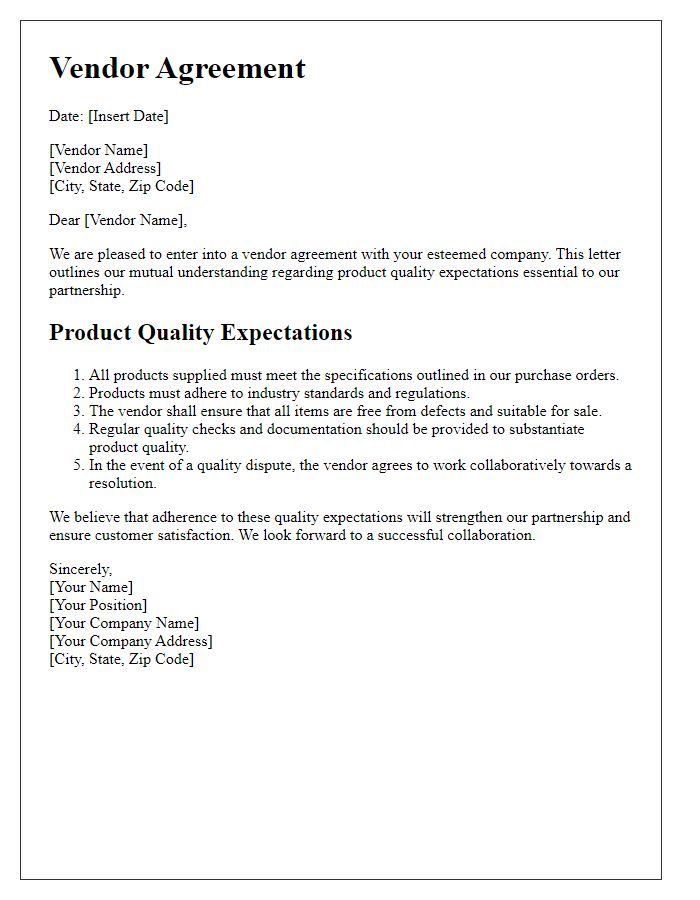
Letter template of vendor agreement to establish quality control protocols

Letter template of vendor agreement emphasizing quality enhancement strategies
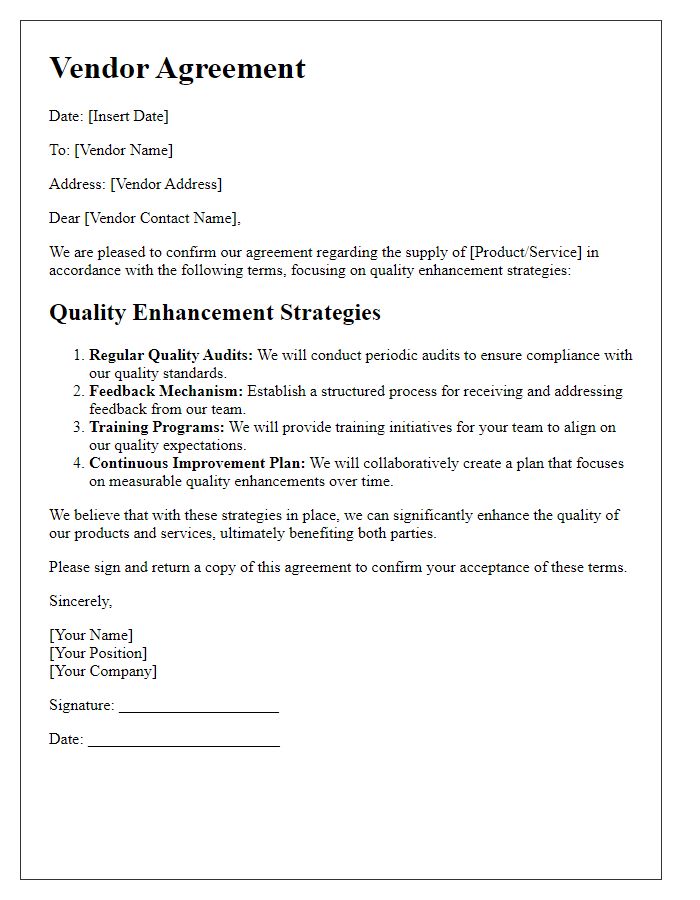
Letter template of vendor agreement outlining quality assessment criteria
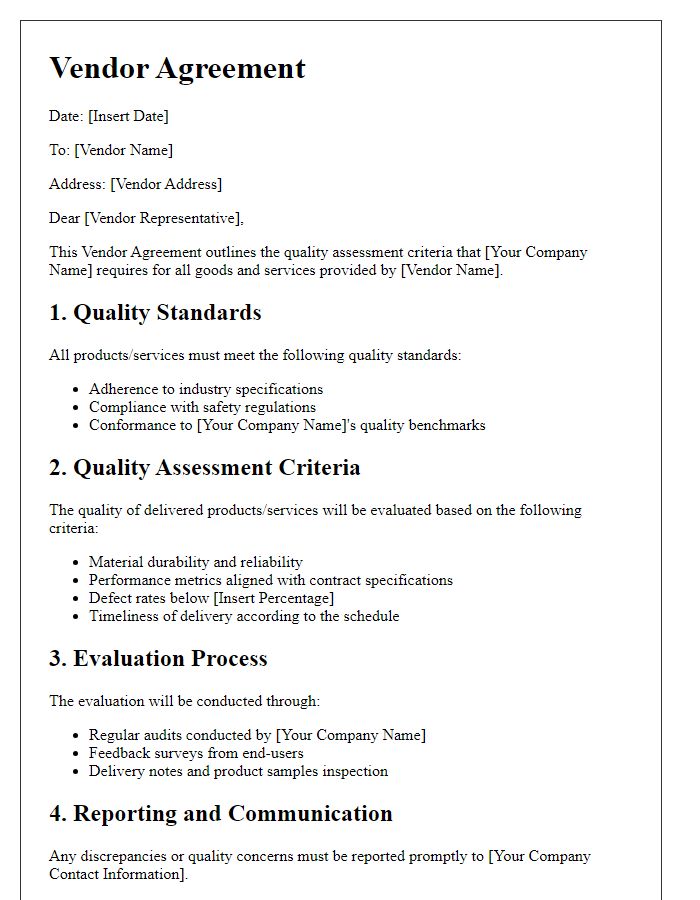
Letter template of vendor agreement detailing quality monitoring processes
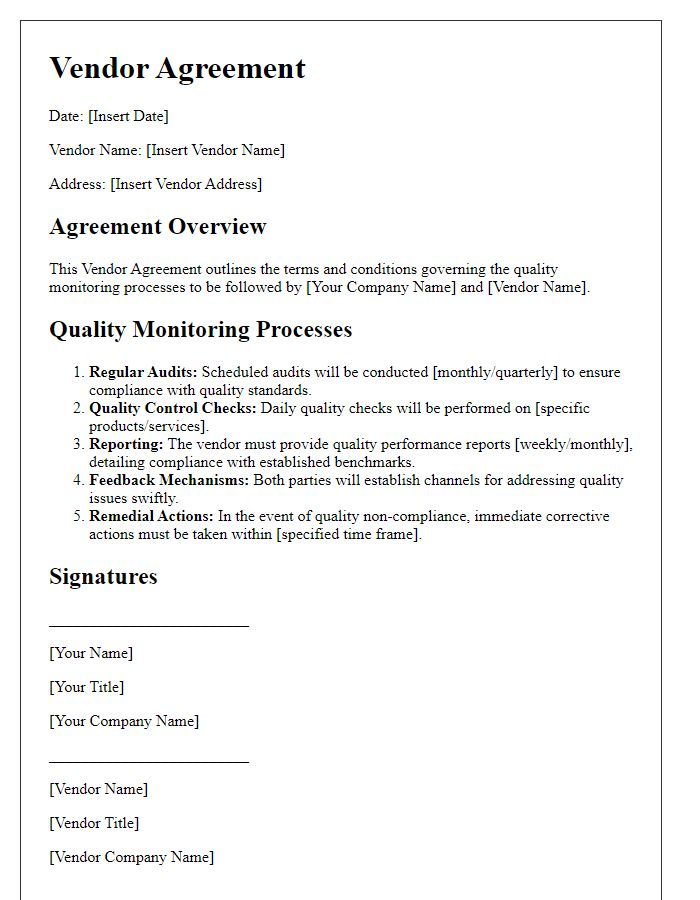
Letter template of vendor agreement concerning quality dispute resolution
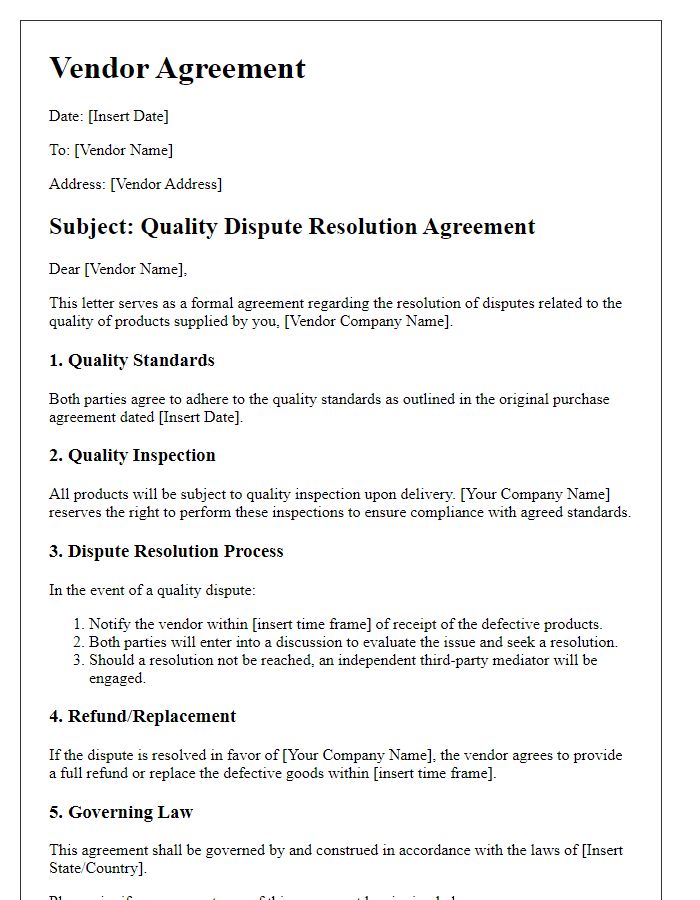
Letter template of vendor agreement addressing product quality certifications
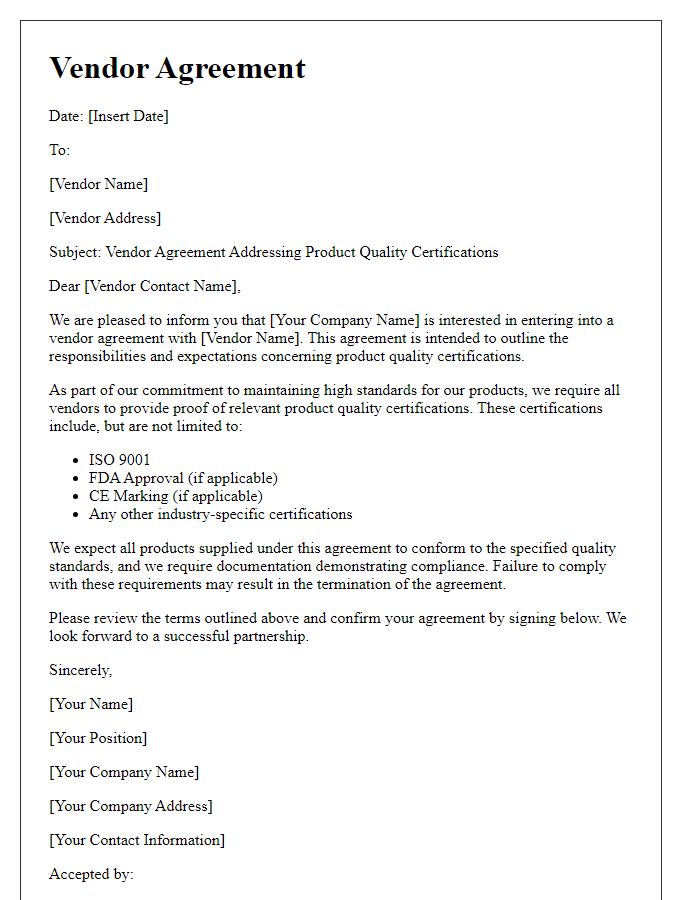
Comments