When it comes to supplier quality assurance, clear and effective communication is essential to maintaining strong partnerships. In this article, weâll explore how to craft a professional letter template that can help convey your quality expectations and enhance collaboration with your suppliers. Whether you're addressing concerns or providing feedback, having a structured approach can streamline the process and ensure everyone is on the same page. So, letâs dive in and discover the elements that will make your supplier communications more effective!
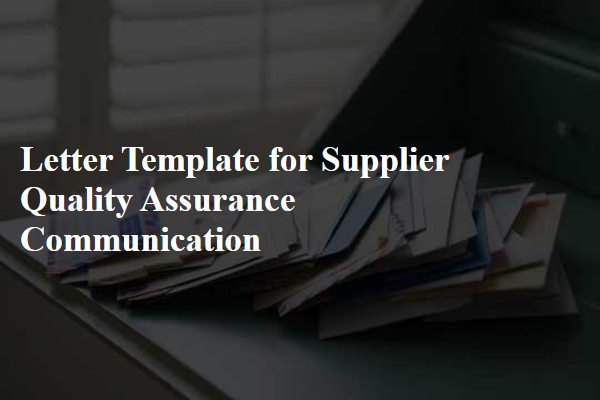
Clear definition of quality standards and expectations.
Supplier quality assurance involves a comprehensive framework that outlines specific quality standards and expectations set by major industries, such as automotive and aerospace. These standards include documentation requirements following ISO 9001 guidelines, which emphasize consistent quality management systems. Key metrics for performance assessment encompass Acceptable Quality Level (AQL) percentages, typically ranging from 1.5% to 2.5%, impacting product rejection rates. Suppliers are expected to adhere to deadlines (e.g., 30-day notice for defects) and maintain traceability for materials sourced from certified vendors (for instance, AS9100 or TS16949 certifications). This structured approach ensures cross-functional collaboration between procurement and quality assurance teams, promoting continuous improvement and risk management strategies throughout the supply chain.
Supplier performance metrics and evaluation criteria.
Supplier performance metrics are essential for assessing the reliability and effectiveness of suppliers in the supply chain. Key performance indicators (KPIs) such as on-time delivery rates (targeting 95% or higher), defect rates (ideally below 2%), and compliance with contractual agreements play a crucial role in evaluating supplier performance. Additionally, factors like quality assurance processes, responsiveness to issues (with a goal of addressing 90% of concerns within 48 hours), and adherence to industry standards such as ISO 9001 significantly influence overall evaluation. Regular assessment through audits (conducted bi-annually) and feedback sessions fosters continuous improvement and stronger supplier relationships. Accurate data collection and transparent reporting practices are vital for maintaining high-level standards in supplier quality assurance communications.
Detailed communication and reporting protocols.
Effective supplier quality assurance communication requires establishing detailed communication and reporting protocols that enhance transparency and accountability within the supply chain. Regular quality audits, typically conducted quarterly, are essential to evaluate supplier compliance with quality standards and specifications. Each audit generates a comprehensive report, focusing on key metrics such as defect rates and on-time delivery percentages. These reports are distributed to stakeholders, including quality assurance teams and management, within three business days of audit completion. Additionally, immediate notification protocols are in place for any non-conformances identified during inspections, ensuring that corrective actions are documented and resolved within 30 days. Regular training sessions, held bi-annually, equip suppliers with necessary quality control techniques, enhancing overall product reliability. A defined escalation pathway for unresolved quality issues ensures timely intervention by senior management, safeguarding product integrity and customer satisfaction.
Procedures for addressing non-conformities or quality issues.
In supplier quality assurance, addressing non-conformities or quality issues is a critical process that ensures compliance with industry standards and enhances product reliability. Procedures typically involve a structured approach that includes identifying the non-conformity through rigorous inspections or quality audits (which occur monthly or quarterly, depending on the supplier agreement). Documentation of the issue is essential, with detailed records that include product specifications, batch numbers, and inspection results. Supplier notifications follow documented protocols, often requiring a root cause analysis within a specified timeframe, usually 30 days. Corrective actions may include rework, product replacements, or changes in manufacturing processes to rectify the quality issues (for instance, ISO 9001 guidelines may be applicable in addressing specific non-conformity types). Ongoing monitoring and verification actions, such as follow-up audits or increased sampling during production, ensure that similar issues do not arise in the future and maintain adherence to contractual obligations.
Continuous improvement and feedback loops.
Effective supplier quality assurance (QA) processes are vital for maintaining product integrity and excellence. Continuous improvement methodologies, such as Total Quality Management (TQM) and Six Sigma, emphasize systematic feedback loops to identify and eliminate defects. For instance, the use of Key Performance Indicators (KPIs) allows for measurable assessments of supplier performance, fostering transparent communication. Regular audits, conducted quarterly, help pinpoint areas needing enhancement, while Quality Assurance Agreements serve as binding documents ensuring compliance with industry standards and specifications. Open dialogues during biannual reviews empower suppliers to share insights and challenges, ultimately building a collaborative environment focused on collective success.
Comments