When it comes to ensuring that your supply chain operates smoothly and meets all necessary standards, supplier compliance certification plays a crucial role. In todayâs ever-evolving market, having reliable partners is essential for maintaining quality and adherence to regulations. Crafting an effective letter to your suppliers regarding compliance certification can streamline communication and foster stronger relationships. Join us as we explore tips and templates that will help you create a compelling letter to ensure your suppliers stay on track.
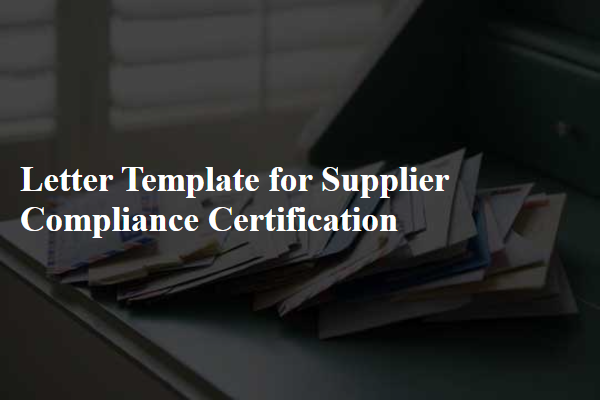
Company Information
Company information for supplier compliance certification includes essential details such as the official name of the business, physical address (including city, state, zip code), registration number (indicating legal incorporation), contact information (phone and email), and the name of the compliance officer or responsible party. Additional elements such as the year of establishment, type of business entity (LLC, corporation, etc.), and industry classification (e.g., manufacturing, services, or retail) provide context for assessing supplier reliability and adherence to regulatory standards. This information establishes a foundational understanding of the supplier's operational framework and compliance capabilities.
Compliance Requirements
Compliance requirements for supplier certification focus on adherence to industry standards, regulations, and best practices. Key elements include quality assurance processes, environmental management systems, and labor laws compliance. Suppliers must provide documentation, such as ISO 9001 certification for quality management, compliance with the Occupational Safety and Health Administration (OSHA) standards, and reports verifying adherence to the Environmental Protection Agency (EPA) regulations. Regular audits in conformity with the standards set by organizations like the International Organization for Standardization ensure ongoing compliance. Additionally, suppliers are expected to demonstrate ethical sourcing practices and commitment to corporate social responsibility, which includes fair labor practices and sustainable environmental practices.
Certification Process
Supplier compliance certification involves a detailed assessment of a supplier's adherence to specified standards and regulations in their field. The process typically begins with an application submission, where the supplier must provide documentation demonstrating compliance with relevant regulations such as ISO 9001 for quality management or ISO 14001 for environmental management practices. Following the application, a rigorous evaluation is conducted by a certifying body, which includes on-site audits, review of processes, and examination of records. Key focus areas may include compliance with safety standards, ethical sourcing practices, and regulatory obligations particular to the industry. Upon successful completion of the audit, the supplier is awarded a certificate of compliance, valid for a designated period, often requiring ongoing surveillance audits to ensure continued adherence to the established standards. This systematic process not only enhances the reliability of suppliers but also strengthens the overall integrity of the supply chain.
Audit and Review Procedures
Supplier compliance certification is crucial for maintaining quality standards in manufacturing. Audits are conducted annually to assess adherence to guidelines set by the International Organization for Standardization (ISO), ensuring compliance with regulations like ISO 9001 for quality management systems. Review procedures include evaluations of documentation, including processes and records, to verify operational integrity. The audit location, typically at the supplier's production facility, involves rigorous inspections of safety protocols and environmental management practices as dictated by the ISO 14001 standard. Non-conformance issues identified during reviews can result in corrective actions, tracking progress through compliance management software. Maintaining transparent communication throughout this process ensures suppliers understand expectations and fosters long-term partnerships.
Contact Details
Supplier compliance certification involves verifying that a supplier adheres to specific regulatory standards and quality assurance processes. Companies often require this certification to ensure that suppliers meet industry-specific guidelines. Key aspects of a supplier compliance certification include detailed contact details such as the company name, physical address, phone number, email address, and primary contact person. The certification process generally outlines mandatory documents to demonstrate compliance, including quality management system documentation, safety certifications, and adherence to environmental regulations. Timely submission of all required information (before deadlines set by regulatory bodies) is crucial for maintaining supplier relationships and minimizing potential disruptions in the supply chain.
Comments