Are you feeling overwhelmed by the intricacies of responding to a subcontractor deficiency list? Itâs a common challenge in the construction industry, but addressing these issues effectively can streamline your project and maintain strong relationships. In this article, weâll break down strategic approaches to crafting a clear and professional response that not only addresses deficiencies but also fosters collaboration. So, letâs dive in and explore how you can turn those challenges into opportunities for improvement!
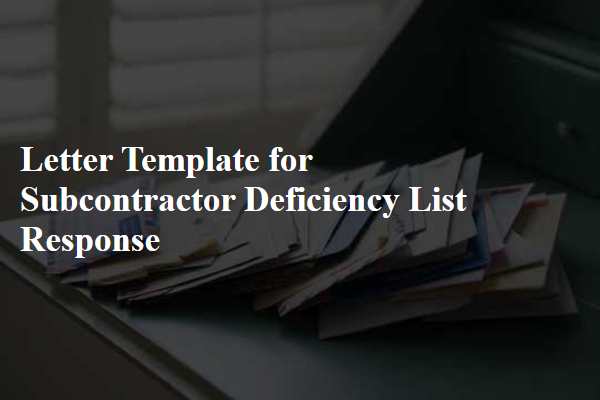
Clear Identification of Deficiencies
A thorough identification of deficiencies is vital in project management to ensure quality and compliance. This process involves inspecting construction work for areas of concern, such as structural defects, safety hazards, or code violations. For instance, in a residential building in Denver, Colorado, issues may arise, including improper insulation installation or cracks in the foundation. Each deficiency must be documented clearly, specifying the location (e.g., Unit 203), the nature of the issue (e.g., leaky pipes), and reference codes from relevant building regulations (such as the International Building Code). Additionally, photographs serve as visual evidence to supplement descriptions. Accurate identification enables effective remediation planning, timely project completion, and adherence to contractual obligations.
Detailed Corrective Action Plan
In construction projects, a detailed corrective action plan is essential for addressing deficiencies identified during inspections or reviews. Each item on the subcontractor deficiency list requires a thorough response, specifying the nature of the deficiency concerning the contracted work (e.g., electrical installations, plumbing, drywall). For instance, an electrical wiring issue in the new office building (located at 123 Business Ave) might necessitate re-routing cables to meet National Electrical Code standards. The plan should include specific corrective measures (e.g., hiring a licensed electrician), timelines for completion (e.g., two weeks for repairs), and quality assurance steps (e.g., subsequent inspections by a project manager), ensuring compliance with project specifications. Progress tracking mechanisms, such as weekly update meetings, will enable transparency and accountability throughout the remediation process.
Timelines for Resolution
A subcontractor deficiency list details the shortcomings in project execution, highlighting areas requiring correction. Timelines for resolution specify deadlines for addressing each identified issue, ensuring accountability in project management. For example, a structural deficiency in concrete reinforcement may require immediate attention within 14 days to meet safety regulations as stipulated by the International Building Code (IBC) 2018. Each timeline should prioritize critical issues impacting overall project completion, such as safety hazards or regulatory compliance. Regular updates on resolution status, potentially outlined in weekly progress meetings, enhance communication between contractors and subcontractors, promoting transparency and efficiency in project execution. Clear documentation of timelines also aids in quality control, ensuring all corrections align with industry standards and contractual obligations.
Contact Information for Follow-Up
The subcontractor deficiency list is a crucial document in construction projects, detailing issues needing attention to ensure compliance with project specifications. Contact information for follow-up is essential, allowing for efficient communication between the contractor and subcontractor. This section should include names, roles, email addresses, and phone numbers of key personnel, such as project managers, quality assurance representatives, and administrative staff. Ideally, the information should be organized for easy accessibility, often presented in a table format for clarity. Clear and prompt follow-up on deficiencies, such as materials failing to meet standards or delays in work completion, ensures the project stays on schedule and within budget.
Acknowledgment of Responsibility
Acknowledgment of responsibility is crucial in addressing deficiencies identified by subcontractors. Companies must perform thorough assessments of the reported issues to ensure proper documentation and resolution. Highlighting specific deficiencies, such as safety compliance problems, quality control failures, or delayed project timelines, can facilitate clearer communication. Timelines for corrective actions should be established, ensuring all parties are aware of expectations. For an effective response, reference industry standards like ISO 9001 for quality management, and include a commitment to continuous improvement processes. Documenting communication through formal channels, such as emails or memos, is essential for accountability and future audits.
Letter Template For Subcontractor Deficiency List Response Samples
Letter template of response to subcontractor's deficiency list acknowledgment
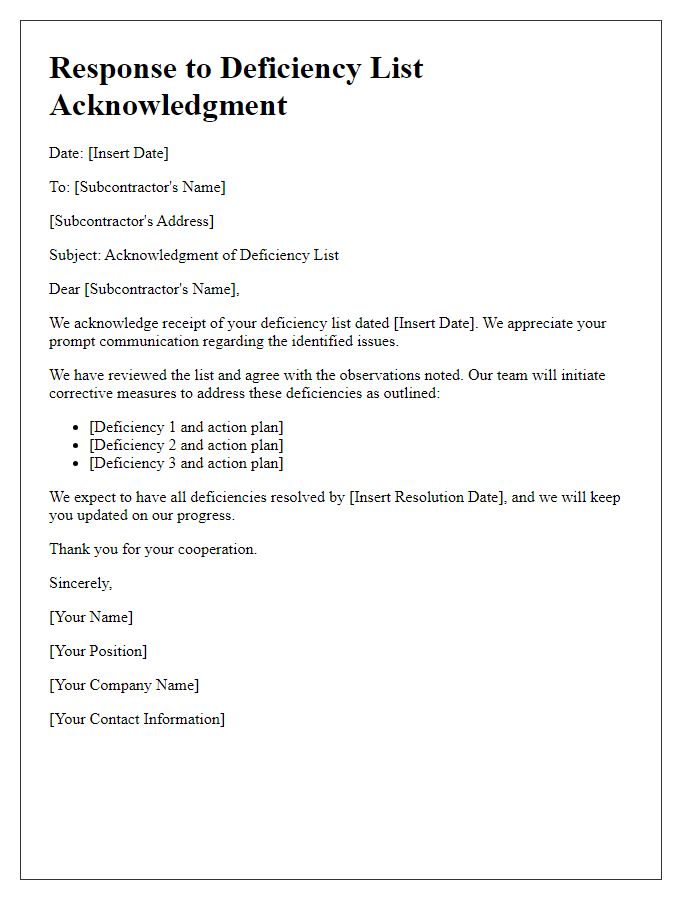
Letter template of corrective action plan for subcontractor deficiencies
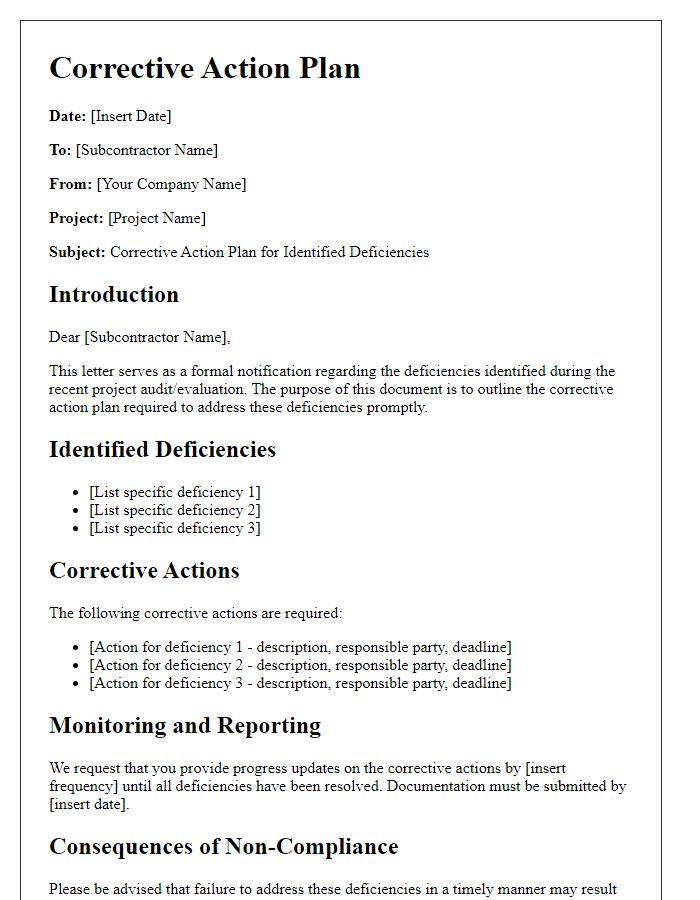
Letter template of request for clarification on subcontractor deficiency list
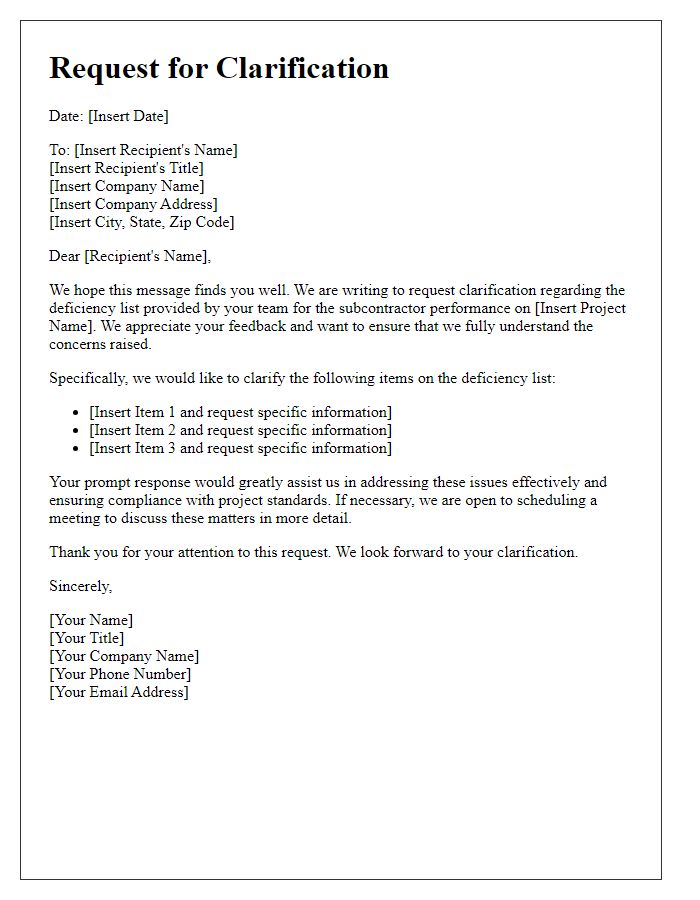
Letter template of proposed timelines for addressing subcontractor deficiencies
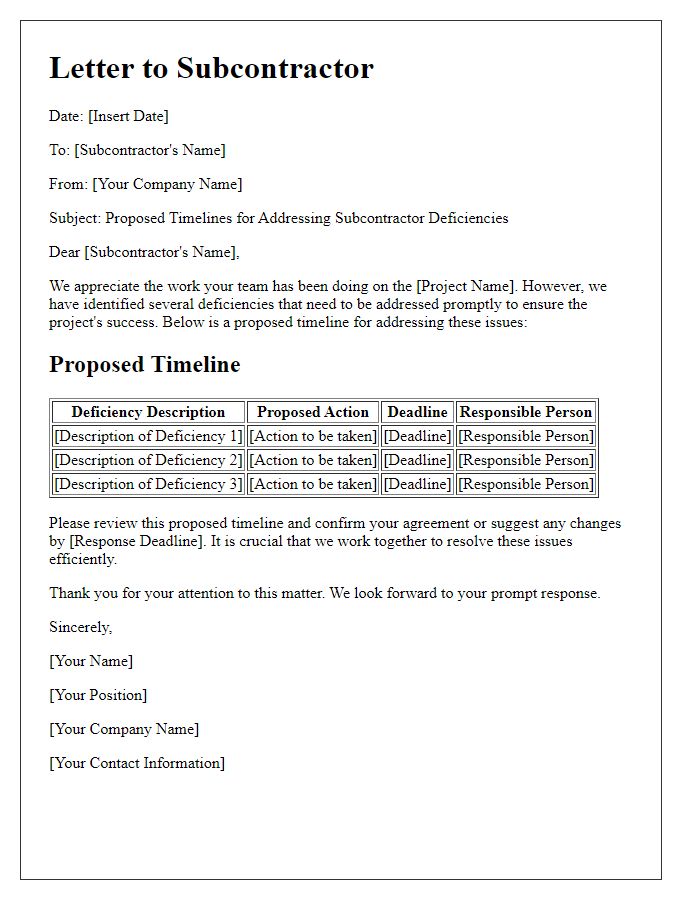
Letter template of acknowledgement of subcontractor's revised deficiency list
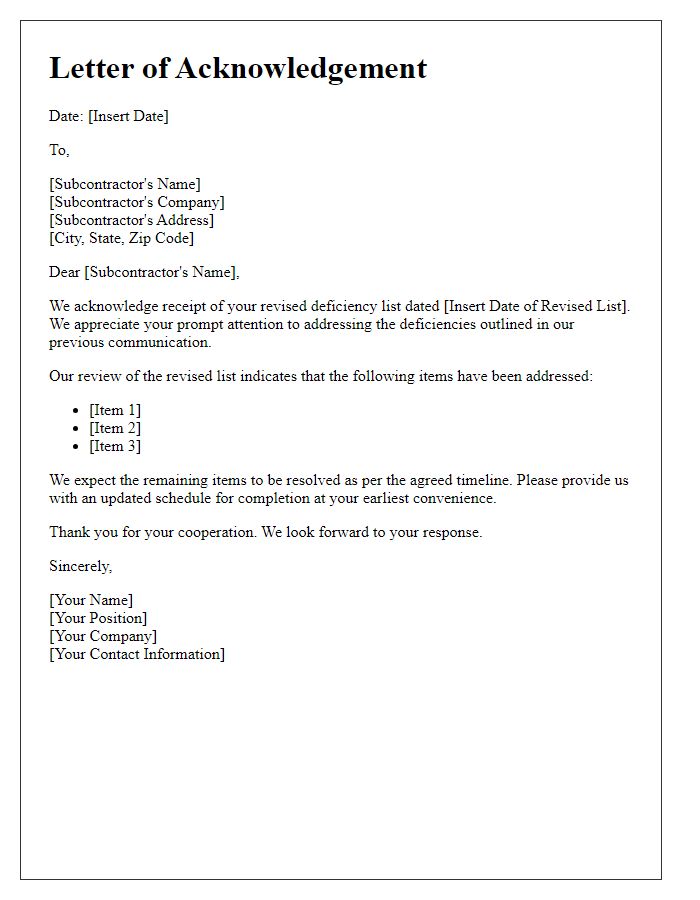
Comments