Are you a reseller looking to streamline your warehouse logistics? Understanding the ins and outs of efficient logistics can dramatically boost your business operations and enhance customer satisfaction. In this article, weâll explore essential strategies and best practices for optimizing your warehouse processes. Team up with us as we dive deeper into this topic and discover how to elevate your logistics game!
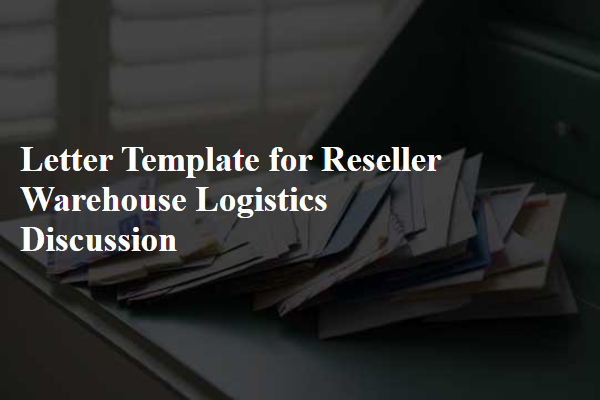
Clear communication and expectations
Efficient communication in reseller warehouse logistics is crucial for optimizing operations and ensuring timely delivery. Clear protocols for inventory management (which typically involves tracking over thousands of SKUs) facilitate streamlined processes within large warehouse facilities, often spanning over 100,000 square feet. Regular meetings (preferably scheduled bi-weekly) among stakeholders, including logistics managers and resellers, should focus on updates regarding shipment schedules and inventory levels. Implementing robust tracking systems, such as RFID (Radio Frequency Identification), can enhance visibility and real-time data access. Understanding key performance indicators (KPIs) like order fulfillment rates (aiming for at least 95%) illustrates the warehouse's efficiency and helps identify areas for improvement. Expectations, particularly regarding lead times (generally ranging from 24 to 48 hours), play a significant role in maintaining reseller relationships and ensuring customer satisfaction.
Efficient inventory management
Efficient inventory management is crucial for optimizing warehouse logistics in reseller operations, particularly in facilities like those found in major distribution hubs such as Los Angeles or Houston. Implementing robust tracking systems can enhance accuracy and reduce discrepancies, with tools like RFID technology tracking items in real-time. Utilizing inventory management software can streamline order processing, ensuring timely fulfillment, especially during peak seasons like the holiday shopping period. Moreover, employing Just-In-Time (JIT) inventory strategies can minimize holding costs, while proactive forecasting based on sales trends helps maintain optimal stock levels, preventing both shortages and overstock situations. Regular audits and a well-defined organizational system can further improve retrieval efficiency, supporting a seamless flow of goods and enhancing overall productivity in the warehouse environment.
Timely delivery and distribution
Timely delivery and distribution are critical components in the logistics framework of a reseller warehouse, impacting supply chain efficiency and customer satisfaction. Late shipments can result in stockouts, which affect sales figures and brand reputation, particularly during peak seasons like the holiday shopping period. Efficient distribution systems, utilizing advanced technologies such as real-time tracking (GPS-based systems), streamline operations, ensuring products arrive at retailers (like Costco, Walmart) within specified timeframes. Additionally, adherence to industry standards for packaging can prevent damages during transit, reducing costs associated with returns. Furthermore, strategic location of warehouses, such as proximity to major highways or urban centers, enhances the speed of fulfillment, ultimately fostering stronger relationships between resellers and suppliers.
Cost-effective transportation solutions
Effective transportation solutions play a crucial role in optimizing logistics for resellers managing warehouse operations. Cost-effective options include partnerships with local carriers, which can reduce shipping expenses significantly, sometimes by up to 25% compared to national providers. Utilizing intermodal transport (combining rail and truck) offers additional savings, particularly for long-distance routes, reducing carbon footprint by up to 30%. Implementing route optimization software enhances delivery efficiency, minimizing fuel costs and improving service speed. Additionally, regional distribution centers strategically located within proximity to key markets, such as Atlanta or Los Angeles, can expedite order fulfillment and reduce overall transit times, ensuring quicker turnaround for resellers and their customers. Investing in technology like real-time tracking systems allows for better inventory management, ensuring that products are delivered on-time and in full.
Enhanced data tracking and analytics
Enhanced data tracking and analytics in reseller warehouse logistics can significantly improve operational efficiency. Advanced analytics tools enable real-time monitoring of inventory levels, ensuring optimal stock management. For instance, implementing a Warehouse Management System (WMS) can provide insights into order fulfillment rates, minimizing delays and improving customer satisfaction. Utilizing Internet of Things (IoT) sensors can track the movement of goods within the warehouse, offering precise data on item location and status. Predictive analytics can forecast demand patterns, allowing for proactive inventory adjustments. Furthermore, businesses can leverage these analytics to identify bottlenecks in the supply chain and streamline processes, ultimately reducing operational costs and enhancing overall productivity.
Comments