Are you looking to streamline your manufacturing process for better efficiency and higher output? In today's fast-paced industry, optimizing every aspect of production is essential for staying competitive and meeting customer demands. Whether it's reducing waste, enhancing workflow, or implementing new technologies, there's a wealth of strategies to explore. Dive in as we unveil key insights and practical tips that can transform your operationsâread more to discover how to elevate your manufacturing processes!
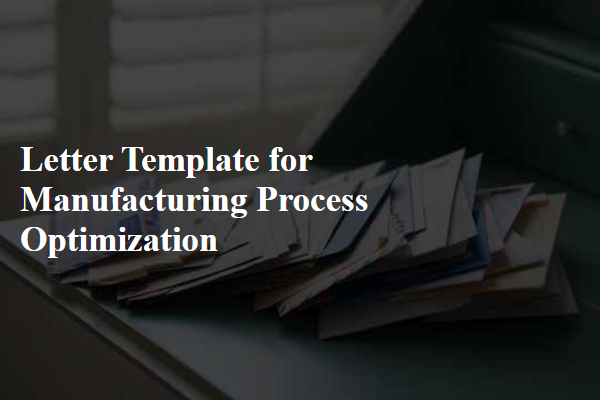
Objective and Purpose
The objective of manufacturing process optimization focuses on enhancing efficiency and reducing waste in production facilities such as automotive factories or electronics manufacturing plants. By utilizing strategies like Lean Manufacturing and Six Sigma, organizations aim to streamline workflow, minimize lead times, and decrease operational costs through analysis of key performance indicators (KPIs). Purpose of these initiatives encompasses improving product quality, ensuring timely delivery to clients, and enhancing overall profitability. Adoption of advanced technologies like automation and artificial intelligence can significantly aid in data analysis, enabling continuous improvement cycles and fostering a culture of innovation within the manufacturing sector. Moreover, employee training and involvement play a crucial role in the successful implementation of these optimization efforts.
Current Process Overview
The current manufacturing process at XYZ Corporation involves several key stages, including raw material procurement, assembly line production, quality control testing, and distribution logistics. Raw materials, primarily sourced from localized suppliers, are delivered using a just-in-time inventory system, ensuring minimal storage costs. The assembly line operates under a lean manufacturing model, aiming for a production efficiency of 85% and minimizing waste through efficient workflow designs and employee training programs. Quality control processes include end-of-line testing in compliance with ISO 9001 standards, which ensures product reliability and safety before reaching customers. Distribution logistics utilize advanced tracking systems, allowing for real-time monitoring of shipments to major retailers like ABC Stores and DEF Warehouses, enhancing delivery times and customer satisfaction. Continuous improvement strategies often analyze cycle times, defect rates, and material utilization rates to identify optimization opportunities that drive production excellence.
Identified Bottlenecks
Bottlenecks in the manufacturing process can significantly hinder overall efficiency in production facilities such as car assembly lines or semiconductor fabrication plants. Common issues include equipment breakdowns; for instance, a machine might experience a 15% failure rate, leading to delays. Labor constraints, particularly in skilled positions like machinists or welders, can further exacerbate production slowdowns, especially when staffing levels fall below 85% of required personnel. Additionally, supply chain disruptions, particularly with critical components like microchips or raw materials, can cause material shortages, pushing production schedules back by several weeks. Implementing solutions like predictive maintenance, workforce training programs, and diversified supplier strategies can help mitigate these identified bottlenecks and enhance throughput.
Proposed Solutions
Manufacturing process optimization focuses on improving efficiency and effectiveness within production environments, such as automotive assembly lines. Efficient workflows (reducing cycle times by 20% or more) can significantly cut costs and enhance output. Implementing lean manufacturing principles, such as just-in-time inventory (reducing excess stock by 30%), minimizes waste and improves resource allocation. Additionally, employing automation (robotics integration can increase production speed by 50%) allows for consistent quality and less human error. Regular staff training programs (increasing skill levels by 25%) enhance workforce competency and adaptability, ensuring rapid response to production demands and potential disruptions. Analysis tools, such as Six Sigma metrics (aiming for 3.4 defects per million opportunities), can facilitate data-driven decisions and continuous improvements. Overall, these strategies foster a streamlined manufacturing process, driving profitability and sustainability.
Expected Outcomes and Benefits
Manufacturing process optimization involves streamlining production methods to enhance efficiency, reduce waste, and improve product quality. Key expected outcomes include a significant reduction in cycle time, with targets aiming for at least a 20% decrease, leading to faster delivery times. Cost savings, projected to reach up to 15% annually, stem from minimizing resource use and energy consumption in facilities, such as ones located in Michigan, known for their automotive manufacturing. Enhanced product quality may improve customer satisfaction ratings, increasing market competitiveness and brand loyalty. Additionally, employee engagement can rise due to streamlined workflows, fostering a positive working environment. Implementing advanced technologies, like automation tools and data analytics, will provide real-time insights into production, further optimizing scheduling and inventory management, crucial for facilities operating under just-in-time (JIT) principles.
Comments