In any manufacturing environment, ensuring the safety of your team is paramount. As we navigate the complexities of daily operations, it's essential to have clear and accessible safety guidelines in place. These guidelines not only protect our workforce but also enhance productivity and morale on the floor. Join us as we dive deeper into the best practices and key measures that can transform safety culture in your manufacturing facility.
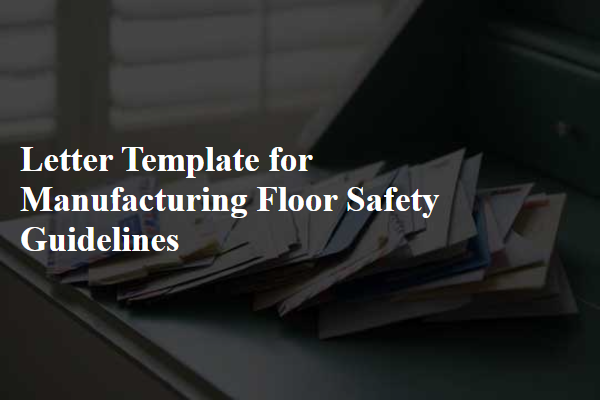
Clarity and Simplicity
Ensuring safety on the manufacturing floor is paramount for the well-being of all employees and the smooth operation of production processes. Safety guidelines must be communicated clearly and simply, utilizing straightforward language. Critical points include wearing Personal Protective Equipment (PPE), such as helmets, gloves, and safety goggles, to minimize injury risks. Regular training sessions should highlight hazard identification, emergency procedures, and proper equipment handling, including forklifts and conveyors, which are crucial for efficient operations. Clear signage indicating safety zones, emergency exits, and first aid stations must be prominently displayed, ensuring accessibility and visibility for all personnel. Daily safety checks can help identify potential hazards, fostering a proactive safety culture within the manufacturing environment.
Concise Instructions
Manufacturing floor safety guidelines are essential for maintaining a secure working environment. Personal protective equipment, including hard hats, goggles, and gloves, must be worn at all times. Hazardous materials, such as solvents and chemicals, are to be stored in designated safety cabinets equipped with proper ventilation systems. Emergency exits, clearly marked and unobstructed, should be accessible at all times. Regular safety drills, conducted quarterly, ensure preparedness for emergencies, such as fire or chemical spills. Additionally, machinery safety protocols, including lockout/tagout procedures, are critical for preventing accidental startups during maintenance. Accident reporting, with specific timelines (within 24 hours), encourages a culture of safety awareness. Employees must be trained in these guidelines, fostering a proactive approach towards workplace safety.
Visual Aids Inclusion
Manufacturing floor safety guidelines emphasize the critical role of visual aids in enhancing workplace safety and awareness. Simple yet effective resources such as brightly colored warning signs, instructional posters, and floor markings serve to communicate hazards, proper procedures, and emergency protocols clearly. In environments like assembly lines or chemical handling areas (like those found in manufacturing facilities), easily recognizable symbols (following ISO 7010 standards) can alert workers to potential dangers, such as slip hazards or the presence of machinery. Additionally, the implementation of safety data sheets (SDS) in conspicuous areas provides information about hazardous materials, ensuring compliance with OSHA regulations and fostering a culture of safety. Utilizing clear visuals not only aids in orientation for new employees but also reinforces the importance of safety practices among seasoned workers, ultimately reducing the risk of accidents on the manufacturing floor.
Compliance and Regulations
Manufacturing floor safety guidelines are critical to ensuring a safe working environment in factories, such as those producing automotive parts or consumer electronics. Compliance with OSHA (Occupational Safety and Health Administration) regulations, effective since founded in 1970, mandates safety training programs covering proper use of personal protective equipment (PPE) like helmets, gloves, and goggles. Regular inspections must occur, following industry standards, to identify hazards such as exposed machinery or slip hazards. Furthermore, emergency protocols need to be established for events like chemical spills or fires, including training employees on evacuation procedures and access to first aid kits. Safety audits, typically conducted quarterly, are essential in maintaining adherence to these regulations and preventing workplace accidents.
Employee Engagement and Feedback
Manufacturing floor safety guidelines emphasize employee engagement and feedback to foster a culture of safety. Regular safety meetings, held weekly in designated areas such as break rooms, enhance communication about potential hazards and safety protocols. The use of suggestion boxes located throughout the facility encourages workers to share insights or report unsafe conditions anonymously. Training sessions, scheduled quarterly, focus on proper equipment handling and emergency procedures, ensuring all employees, estimated at over 250, are equipped with the knowledge to maintain a safe environment. Moreover, safety audits, conducted monthly by trained personnel, provide opportunities for employees to contribute to evaluations and suggest improvements. This proactive approach bolsters workplace morale and cultivates a united commitment to safety.
Letter Template For Manufacturing Floor Safety Guidelines Samples
Letter template of safety protocol reminders for the manufacturing floor
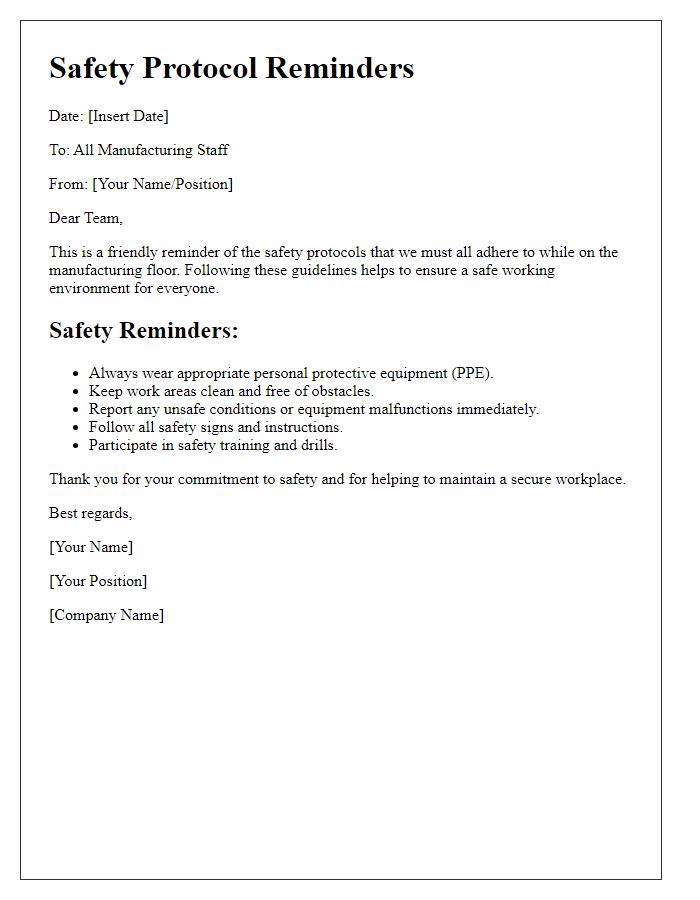
Letter template of incident reporting procedures for shop floor employees
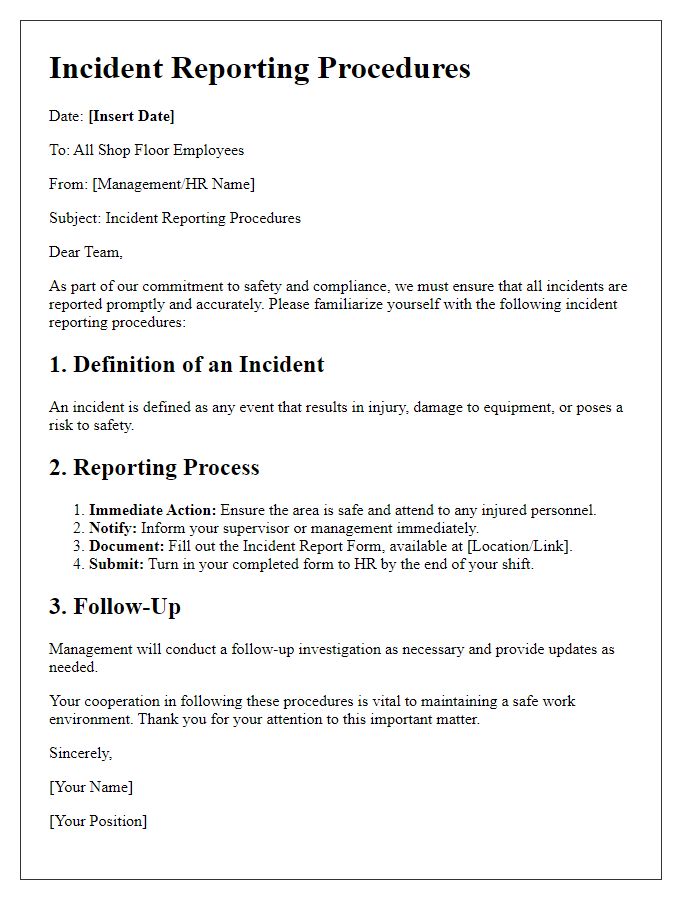
Letter template of personal protective equipment (PPE) requirements for workers
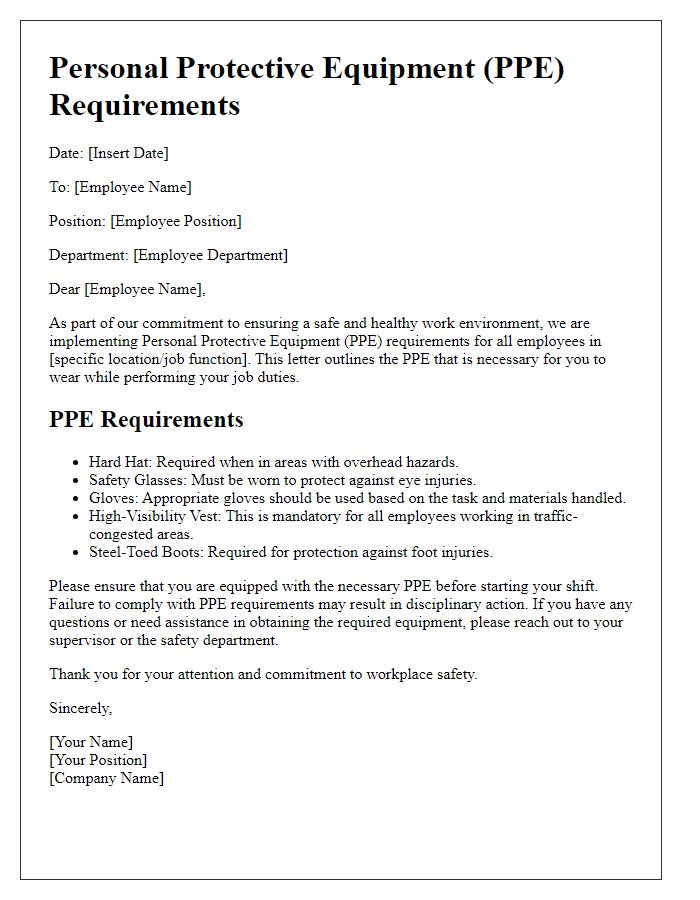
Letter template of emergency evacuation plans for the manufacturing area
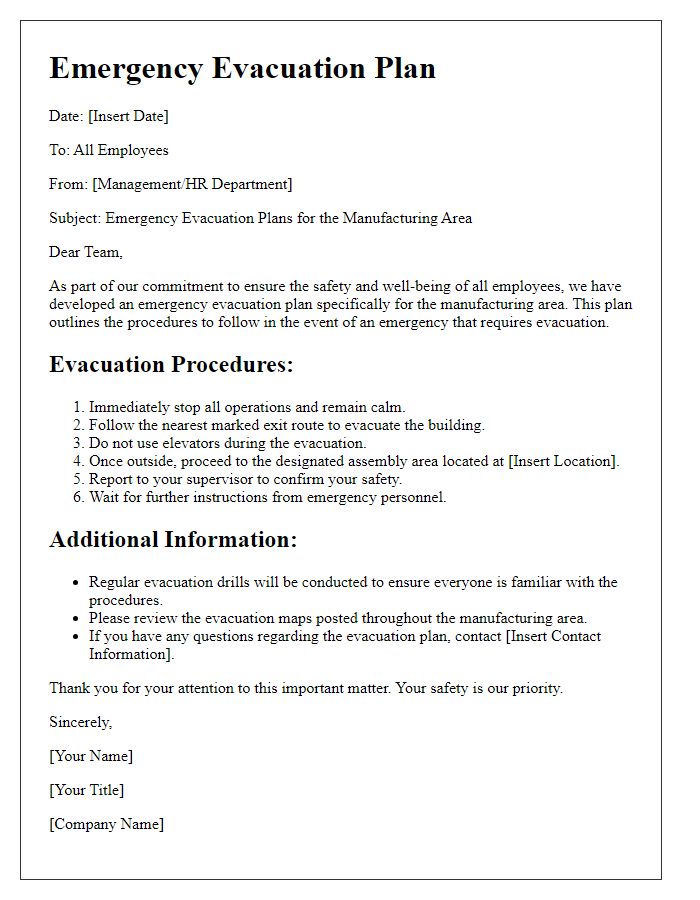
Letter template of safety awareness campaigns for manufacturing personnel
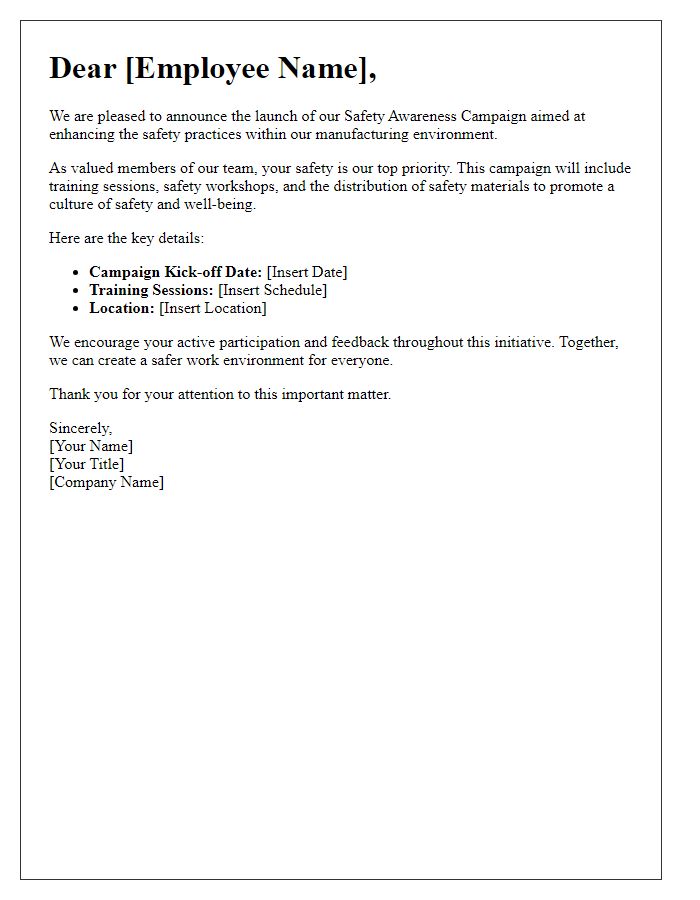
Comments