Are you looking to enhance the efficiency of your manufacturing processes? Improving operational workflows not only boosts productivity but also significantly reduces costs in the long run. In this article, we'll explore practical strategies and innovative technologies that can help you streamline your production lines for maximum output. So, if you're ready to transform your manufacturing efficiency, keep reading!
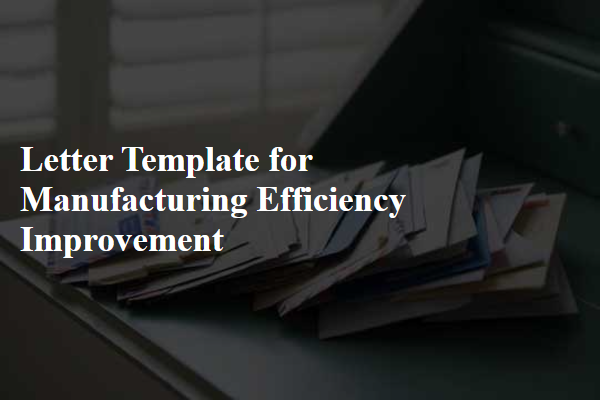
Clear objectives and goals
Manufacturing efficiency improvement focuses on optimizing production methods and minimizing waste in industrial settings, crucial for companies like Toyota (renowned for its lean manufacturing principles). Clear objectives include reducing cycle times by 20% within six months and increasing overall equipment effectiveness (OEE) to 80%. Goals also encompass training 100% of employees in Lean Six Sigma methodologies by the end of the fiscal year to enhance problem-solving skills. Additionally, implementing a real-time data monitoring system can track production metrics, enabling quick responsiveness to inefficiencies. Regular weekly audits will measure progress towards these targets, ensuring alignment with corporate strategy and fostering a culture of continuous improvement across all manufacturing operations.
Detailed action plan
Manufacturing efficiency improvements rely on systematic analysis and targeted action plans. Implementing strategies such as Lean Manufacturing can significantly reduce waste in processes, enabling companies to optimize resource utilization. A detailed action plan might include specific metrics like Overall Equipment Effectiveness (OEE), aiming for a target of 85% efficiency across production lines. Workers need additional training sessions scheduled every quarter, focusing on best practices and safety measures, which can increase productivity by 15%. Regular equipment maintenance intervals must be established, with preventative checks every 30 days, ensuring optimal machine performance. Production layouts can be restructured to minimize downtime between stages, potentially reducing cycle time by 20%. Continuous feedback loops from staff in weekly meetings can enhance accountability and foster a culture of improvement, contributing to overall operational excellence.
Key performance indicators (KPIs)
Key performance indicators (KPIs) are crucial for assessing manufacturing efficiency within production facilities. Metrics such as Overall Equipment Effectiveness (OEE) provide insight into machine productivity by measuring availability, performance, and quality rates. Tracking cycle time, defined as the total time from the beginning to the end of a manufacturing process, allows facilities like Toyota's factories in Japan to identify bottlenecks. Additionally, First Pass Yield (FPY), measuring the percentage of products manufactured correctly without rework, serves as a critical quality indicator. Companies utilize these KPIs to establish benchmarks, enhance processes, and increase output by aiming for reductions in downtime, waste, and defects. The implementation of real-time monitoring systems, such as IoT-enabled machinery, facilitates the continuous analysis of these KPIs, fostering a culture of improvement in competitive industries.
Employee roles and responsibilities
Employee roles in manufacturing efficiency improvement involve a detailed understanding of processes, tasks, and performance metrics. Production managers oversee workflow optimization, ensuring machinery (equipment such as CNC machines) operates at maximum capacity, while quality assurance specialists monitor product standards in compliance with ISO 9001 regulations. Machine operators (with skills in operating various manufacturing tools) are responsible for the precision of their tasks, implementing lean manufacturing techniques to minimize waste. Additionally, maintenance technicians work on preventive measures to avoid downtime (excessive machinery idleness), ensuring that equipment like conveyor belts and robotic arms function smoothly. Collaboration among all roles is crucial for fostering an environment dedicated to continuous improvement, driving overall productivity and profitability within the manufacturing facility.
Evaluation and feedback process
Manufacturing efficiency improvement relies heavily on a robust evaluation and feedback process. Key performance indicators (KPIs) should be established, such as production output (measured in units per hour) or waste reduction percentages (targeting a decrease of at least 15% annually). Regular audits should occur, preferably quarterly, involving real-time data collection from production lines in facilities like those in Detroit, Michigan. Utilization of lean manufacturing principles can streamline workflows, reducing lead times (the amount of time that passes from the beginning until the product is completed) by approximately 20%. Employee feedback, gathered through surveys and suggestion boxes, can foster a culture of continuous improvement (the ongoing effort to enhance products, services, or processes) and increase engagement. Additionally, comparative analysis against industry benchmarks can provide valuable insights into performance gaps and highlight areas for growth and innovation.
Letter Template For Manufacturing Efficiency Improvement Samples
Letter template of request for manufacturing efficiency enhancement proposal

Letter template of communication regarding production efficiency strategies
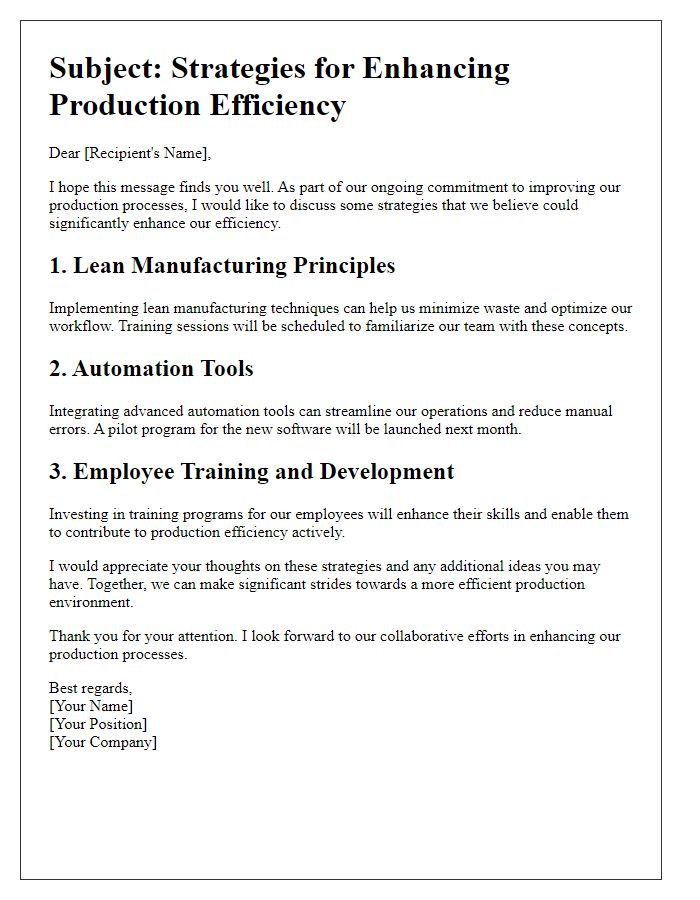
Letter template of invitation for collaboration on manufacturing advancement

Letter template of outline for efficiency improvement initiatives in production
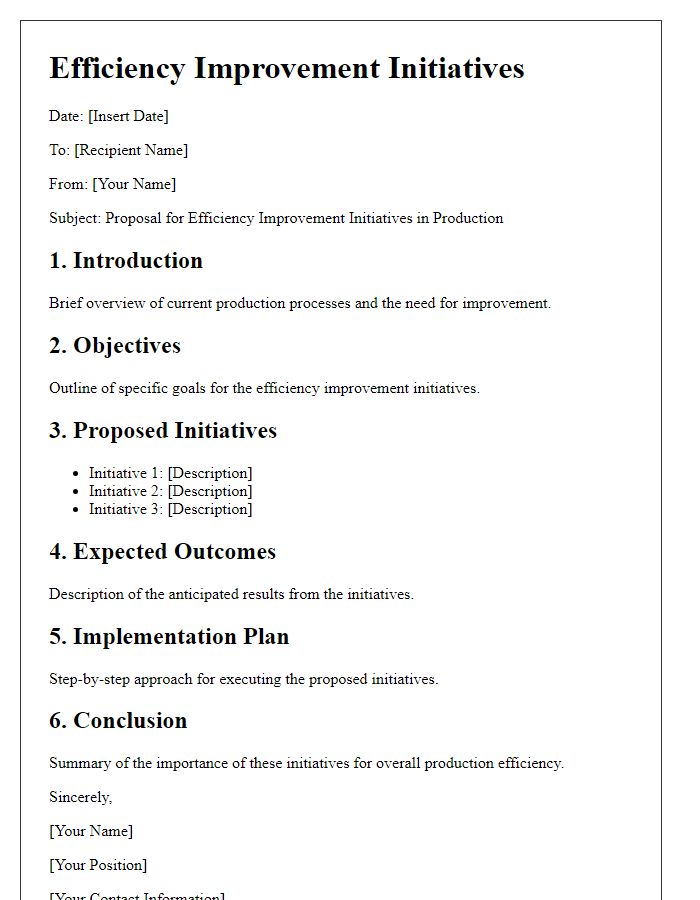
Letter template of assessment for current manufacturing efficiency levels
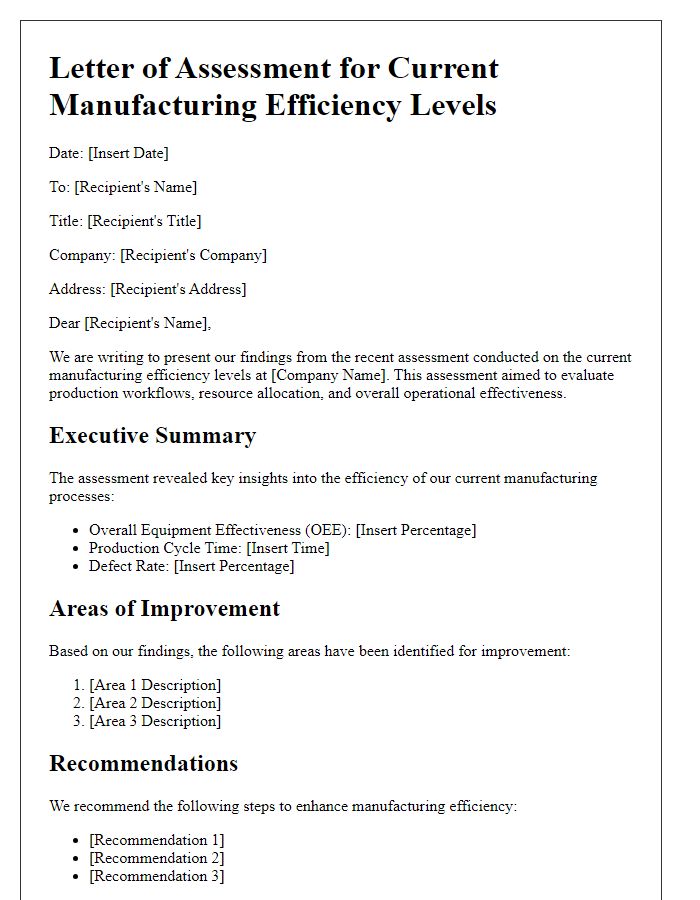
Letter template of feedback request on manufacturing productivity enhancements
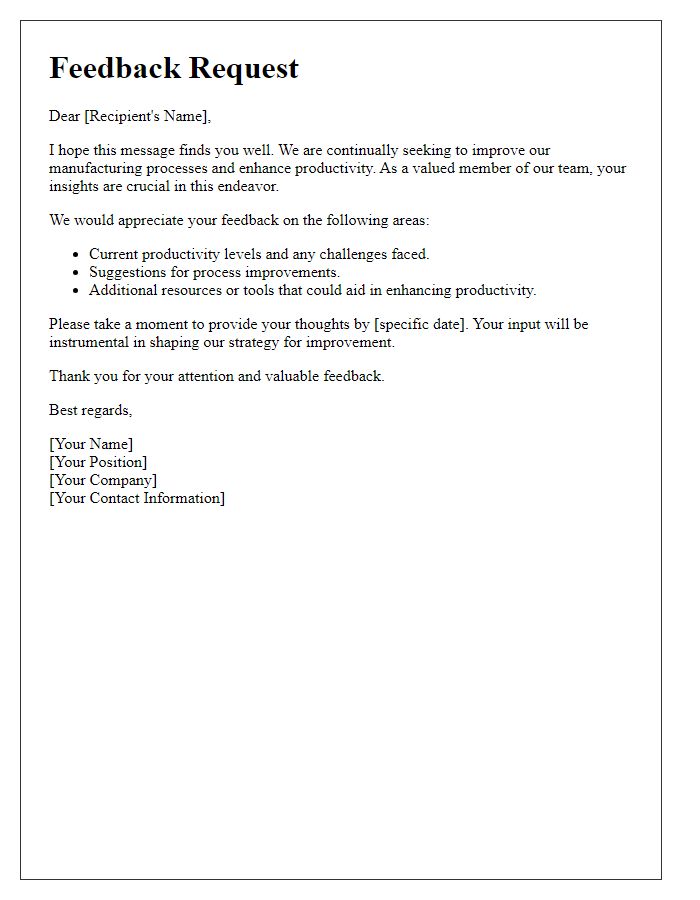
Letter template of discussion prompts for operational efficiency improvements
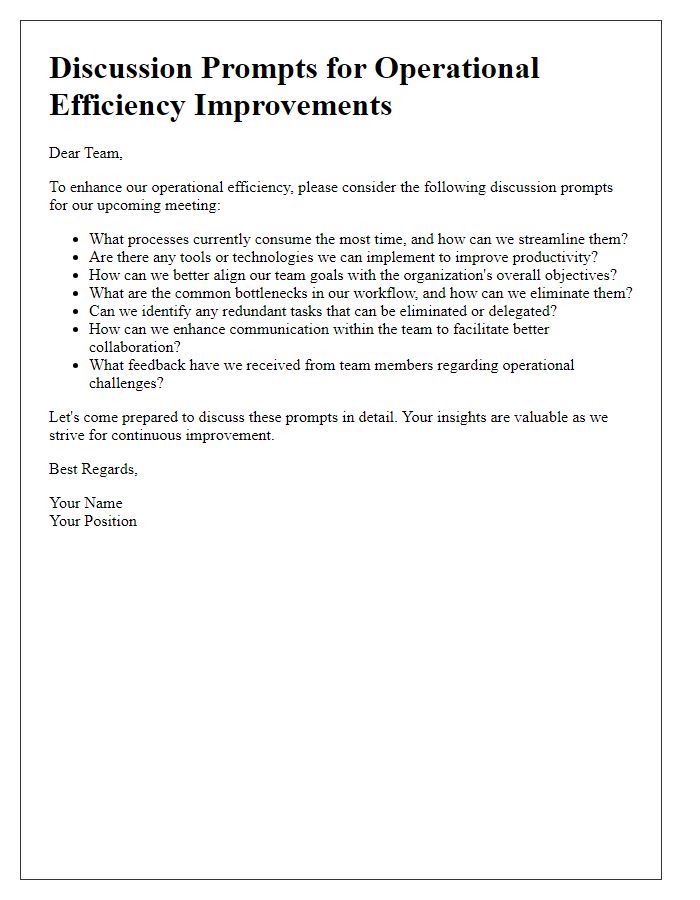
Letter template of summary report on recent manufacturing efficiency projects
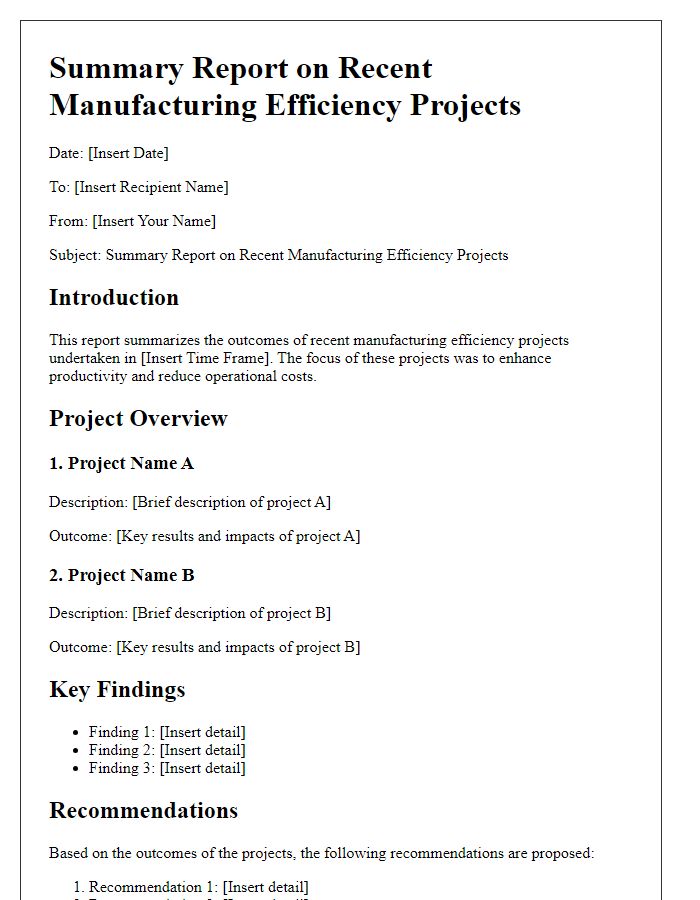
Comments