Are you curious about how to maximize your production capabilities? Understanding your production capacity is essential for optimizing efficiency and meeting market demands. In this article, weâll explore the key factors that influence production capacity and provide practical strategies for analysis and improvement. Join us as we dive deeper into enhancing your production processes!
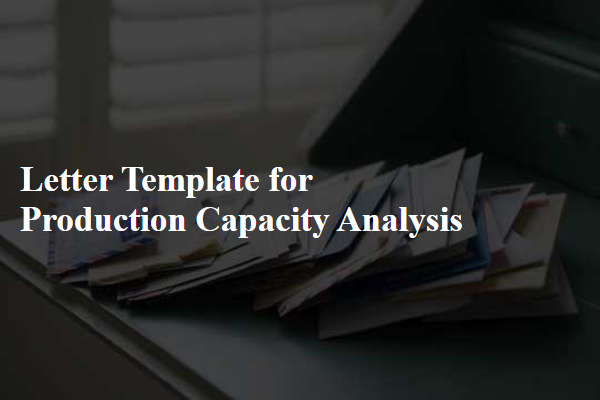
Introduction and Purpose
Production capacity analysis serves as a critical tool for manufacturers seeking to optimize output capabilities. This assessment evaluates the maximum production volume that facilities can achieve under normal operating conditions, encompassing critical factors such as machinery efficiency, workforce availability, and supply chain logistics. By understanding current production limits, businesses can identify bottlenecks, streamline processes, and ultimately enhance productivity. Industries such as automotive manufacturing in Detroit or electronics production in Shenzhen face increasing demands; therefore, capacity analysis aids in informed decision-making for expansion, resource allocation, and strategic planning. The insights gathered can lead to improved operational workflows and ultimately drive profitability.
Current Production Capacity Assessment
Current production capacity assessment reveals critical insights into operational efficiency within manufacturing facilities, such as those located in Detroit, Michigan. This analysis evaluates output levels (measured in units per hour) against demand forecasts for the upcoming quarter, focusing on core product lines like automotive components. Metrics such as overall equipment effectiveness (OEE) and utilization rates (currently at 75%) are analyzed to identify bottlenecks in processes. Additionally, personnel productivity, average labor hours, and material availability are scrutinized to ensure alignment with optimal production schedules. Understanding these factors is essential for making informed decisions about scaling operations or investing in new technologies to enhance throughput and meet projected consumer demands effectively.
Demand Forecasting and Trends
Accurate demand forecasting is essential for optimizing production capacity in manufacturing sectors such as automotive or electronics. Statistical techniques like moving averages and exponential smoothing are commonly employed to analyze historical data and predict future sales trends. Seasonal variations can significantly impact demand, particularly during holiday periods or special events, necessitating adjustments to the production schedule. The application of demand forecasting models enables companies to allocate resources effectively, reducing costs associated with overproduction or stockouts. Integrating real-time market analysis, such as competitor sales and consumer behavior shifts, enhances the forecasting process, enabling businesses to adapt quickly to changing trends.
Bottlenecks and Constraints Identification
In production capacity analysis, identifying bottlenecks and constraints is crucial for optimizing efficiency and output. A bottleneck occurs when a specific step in the manufacturing process limits overall production, such as the assembly line in a factory like Ford Motor Company, where delays can stem from machinery failures or labor shortages. Constraints may involve resource limitations, such as the availability of raw materials like steel or plastic, which can hinder the production flow. For example, a factory producing electronic devices may face constraints if semiconductor supplies diminish due to global shortages, impacting manufacturing timelines. Analyzing these areas through methods like Value Stream Mapping can help pinpoint inefficiencies, allowing manufacturers to implement proactive solutions to enhance throughput and reduce lead times.
Recommendations and Action Plan
Production capacity analysis highlights operational efficiency in manufacturing facilities, essential for meeting market demand. Key variables include total output (measured in units per hour), equipment reliability (percentage of uptime), and workforce productivity (units produced per worker). Locations such as Detroit (known for automotive production) or Shenzhen (a hub for electronics) illustrate varying capacities influenced by local labor markets and technological advancements. Recommendations often involve adopting lean manufacturing principles to reduce waste, implementing automation technologies for improved output rates, and scheduling regular maintenance to enhance equipment longevity. Action plans typically focus on training programs to elevate workforce skills, investment in advanced machinery, and exploring alternative suppliers to mitigate risk and ensure a steady flow of raw materials. These strategic measures aim to optimize production capacity, ultimately leading to increased profitability and competitiveness in changing markets.
Comments