Are you ready to showcase your manufacturing prowess? Entering the Manufacturing Innovation Award is a fantastic opportunity to highlight your team's cutting-edge initiatives and remarkable achievements in the industry. This prestigious accolade not only recognizes excellence but also provides a platform for sharing revolutionary ideas that can inspire others. Join us as we delve deeper into the particulars of crafting a standout entry that will make your innovation shine!
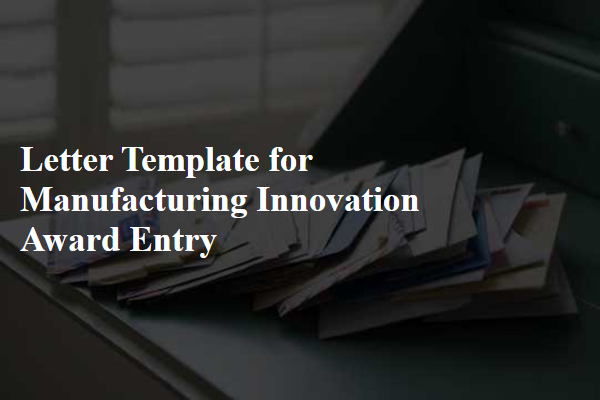
Company Overview and Background
XYZ Manufacturing Inc., headquartered in Seattle, Washington, has been a leader in the production of precision-engineered components since 1995. With a workforce of over 500 skilled employees, the company has achieved a remarkable annual revenue of $150 million. The facility spans 200,000 square feet, equipped with cutting-edge machinery such as CNC milling machines and robotic assembly lines. XYZ Manufacturing focuses on industries like aerospace, automotive, and medical devices, consistently prioritizing quality and sustainability. The implementation of lean manufacturing principles has resulted in a 30% reduction in production waste since 2018. Recent innovations include the development of a patented composite material that enhances durability while reducing weight, contributing to both performance and environmental responsibility.
Innovation Description and Uniqueness
The innovative manufacturing process implemented at XYZ Corporation utilizes advanced robotics and artificial intelligence to optimize production efficiency. This cutting-edge method, specifically the use of collaborative robots (cobots), reduces human error and increases output by 30% compared to traditional methods. The integration of machine learning algorithms allows for real-time adjustments in the production line, enhancing adaptability to varying demand levels. Notably, this process minimizes waste by 40% through precise material handling and predictive maintenance strategies, ensuring sustainability in operations. Unique aspects include the implementation of an IoT-enabled monitoring system, which provides detailed analytics on equipment performance and environmental conditions, contributing to a safer and more streamlined manufacturing environment.
Impact and Benefits on Industry
A manufacturing innovation, such as the integration of Industry 4.0 technologies, facilitates transformative changes in production processes, enhancing efficiency and reducing waste across factories globally. The implementation of advanced robotics and IoT (Internet of Things) devices enables real-time data analytics, leading to a significant decrease in operational costs, estimated at 20-30% in many sectors. This innovation also promotes sustainability by minimizing resource usage, with companies reporting up to 15% lower energy consumption after adopting these technologies. Moreover, enhanced production flexibility allows manufacturers to respond swiftly to market demands, fostering a competitive edge in fast-paced environments like automotive or electronics industries, where rapid changes are common. The positive ripple effect extends to overall workforce engagement, as automation takes over repetitive tasks, allowing skilled workers to focus on high-value activities, ultimately increasing job satisfaction.
Evidence of Success and Metrics
Evidence of success in manufacturing innovation can be measured through various metrics demonstrating efficiency and productivity improvements. For example, a facility in Michigan (2023) reported a 25% reduction in production time due to the implementation of automated assembly lines. This innovation has resulted in a cost savings of $1.5 million annually, alongside a 40% increase in output quality as indicated by a decrease in defect rates to below 1%. Furthermore, employee engagement surveys show a 30% increase in satisfaction levels, resulting from streamlined workflows and the introduction of advanced training programs. Tracking inventory turnover rates revealed an enhancement from 5 to 8 times annually post-innovation, highlighting improved supply chain efficiency. Overall, these metrics indicate substantial success and measurable impacts on operational performance and employee morale following the implementation of innovative manufacturing practices.
Future Plans and Sustainability
Future plans in the realm of manufacturing innovation encompass strategies aimed at enhancing efficiency and minimizing environmental impact. The adoption of advanced technologies such as automation, robotics, and artificial intelligence (AI) can significantly streamline production processes, ensuring higher output with reduced waste. For instance, integrating AI-driven analytics can optimize resource allocation and energy consumption, aligning with sustainability goals. Moreover, the implementation of circular economy principles--where materials are reused, repurposed, or recycled--can drastically decrease the carbon footprint associated with manufacturing activities. Partnerships with local suppliers not only strengthen community ties but also minimize transportation emissions and promote sustainable sourcing. Setting measurable targets, such as achieving a 30% reduction in greenhouse gas emissions by 2025, further underscores a commitment to environmental responsibility and positions the organization as a leader in sustainable manufacturing practices.
Comments