Are you looking to fine-tune your quality control processes? Adjusting the quality control measures in your organization can significantly enhance product reliability and customer satisfaction. In this article, we'll explore the key components and strategies for implementing effective quality control adjustments. So, if you're ready to elevate your company's standards, let's dive in!
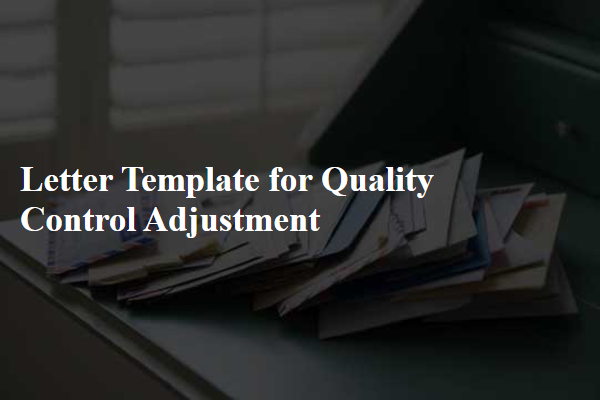
Header and contact information
Quality control adjustments play a critical role in maintaining product standards and ensuring compliance with industry regulations. Regular audits allow organizations to identify discrepancies in manufacturing processes and supplier performance, thereby reducing defects and enhancing overall product quality. Effective communication regarding these adjustments also fosters collaboration among teams, including quality assurance, production, and engineering. Implementing data-driven strategies enables teams to track quality metrics and assess adjustments based on historical performance, enhancing decision-making. Continuous improvement methodologies, such as Six Sigma, can further streamline quality control processes and ensure that products meet customer expectations consistently. Detailed documentation of quality control parameters is essential for regulatory compliance and serves as a reference for future audits.
Subject line and salutation
Quality control adjustments are critical to maintaining product standards and consumer safety. Quality control processes, such as Six Sigma or ISO 9001, ensure consistent manufacturing practices in industries like pharmaceuticals or automotive. Regular audits, typically scheduled semi-annually, identify discrepancies and improve product quality. Actionable insights derived from inspection data guide necessary adjustments to machinery or procedures, helping prevent defects and reduce waste. Continuous training for staff on quality assurance practices reinforces a culture of quality, ultimately leading to enhanced customer satisfaction and brand reputation.
Description of quality issue
Quality control issues often arise in manufacturing processes, impacting product standards and customer satisfaction. For instance, in the automotive industry, a common quality issue could be related to defective brake systems, where a sample lot of brakes (potentially 5% of a recent batch) exhibits a failure rate of 2% during routine testing, causing safety concerns. Additionally, in electronics, a malfunctioning display might occur in a batch of 1,000 smartphones, particularly affecting models released in 2023, leading to pixel abnormalities or color inconsistencies. Identifying the root cause of these issues is critical, often involving traceability of materials used, inspection protocols, and adherence to ISO 9001 standards. Moreover, the effectiveness of corrective actions should be monitored meticulously to ensure compliance and improve overall product reliability, thereby enhancing brand reputation.
Specific adjustments or actions planned
Quality control adjustments play a vital role in enhancing manufacturing standards and ensuring product reliability. Specific actions planned include implementing a review of batch processes to identify discrepancies in production lines, conducting training sessions for staff on quality assurance protocols, and adjusting inspection frequency for high-risk components, such as steel parts in automotive manufacturing. Data analysis from previous quality assurance reports will guide these adjustments, focusing on defects reported in the last quarter of 2023. Additionally, collaborations with suppliers will be established to ensure that raw materials meet established specifications and standards, thereby improving overall product quality and customer satisfaction.
Closing remarks and contact details
Quality control adjustments often lead to significant improvements in product standards, ensuring compliance with regulations and customer satisfaction. In these processes, documentation plays a crucial role in tracking changes and decisions. For example, revising quality parameters might involve adjusting the acceptable limits for defects, adhering to ISO 9001 standards. Closing remarks in quality control reports should summarize the findings and highlight the importance of continuous improvement methodologies. Additionally, providing relevant contact details for further inquiries or clarification fosters communication and collaboration among team members and stakeholders, facilitating a more efficient resolution of quality issues.
Comments