In todayâs fast-paced business environment, maintaining strong relationships with our suppliers is crucial for success. However, situations may arise that necessitate clear communication about critical issues affecting our partnerships. This letter serves as a formal notification to our esteemed suppliers about significant changes or concerns that might impact our collaborative efforts. We invite you to explore the details of this notification further and understand how we can work together to address these challenges.
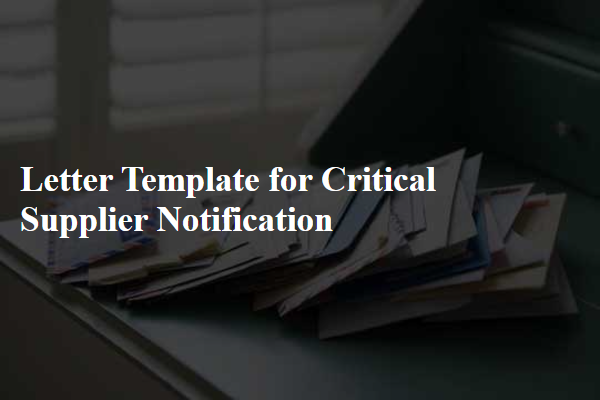
Clear subject line
A critical supplier notification must include a clear subject line to ensure immediate attention. A subject line should clearly state the purpose, such as "Urgent: Critical Supplier Notification Regarding Contractual Changes." A well-defined subject identifies the importance of the message, providing context for the recipient. This helps streamline the communication process, especially when multiple notifications are received. Direct language guides the receiver to prioritize this specific notification amidst other correspondence, fostering timely and appropriate responses. A concise and relevant subject is crucial for effective supplier management and continuity of operations.
Supplier identification details
Critical supplier identification in a procurement process involves essential data to ensure reliable partnerships. Supplier identification details include unique identifiers such as the DUNS number (Data Universal Numbering System) which provides a unique identity for businesses, enabling better risk assessment. Company name, along with the registered address (often necessary for contracts), are fundamental for verifying supplier legitimacy. Key contact information, such as the primary representative's name and direct phone number, facilitates seamless communication. Additionally, the supplier's business classification, such as whether they are categorized as a small or minority-owned business, impacts diversity metrics and procurement strategies. Compliance documents like certificates of insurance and quality assurance standards (ISO certifications) further assure reliability and adherence to industry regulations. Regular updates on the supplier's performance metrics, delivery timelines, and capacity can optimize supply chain operations.
Description of the critical situation
The recent supply chain disruptions have led to a significant delay in the delivery of essential components needed for production. This situation has arisen due to unforeseen circumstances, such as natural disasters in key manufacturing regions, exacerbated by the ongoing global semiconductor shortage affecting various industries. Disruptions noted in regions like Southeast Asia have caused production halts in factories, impacting the availability of critical materials. Additionally, logistical challenges due to port congestion in major shipping hubs worldwide have further delayed shipments, resulting in a projected shortfall of 30% of required components within the next quarter. This critical situation threatens project timelines and overall operational efficiency, necessitating immediate communication and action to mitigate potential impacts on product delivery schedules.
Urgency and priority level
Critical supplier notifications demand immediate attention due to potential impacts on supply chain operations. Urgency is typically classified based on severity levels; for instance, a Level 1 urgency might indicate a total production halt due to shortages of essential materials, like steel from suppliers in China, affecting manufacturing timelines. A Level 2 situation could arise from delayed shipments of components, such as semiconductors necessary for electronics, threatening project deadlines. Compliance with contractual obligations, including delivery schedules, often dictates priority levels in communication. Notable events, like natural disasters or geopolitical tensions, can exacerbate these issues, prompting suppliers to adjust capacity or logistics. Clear guidelines for escalating these notifications ensure that all parties respond effectively to mitigate disruptions.
Request for action and deadline
Critical suppliers must address quality assurance issues in their production processes, which have been linked to multiple product defects reported across various markets (including Quarter 3 sales in North America and Europe). Specific flaws identified include discrepancies in material specifications and inconsistencies in manufacturing tolerances, leading to increased returns and customer dissatisfaction. Immediate action is required: suppliers must implement corrective measures by November 30, 2023, and provide a detailed report outlining these actions and measures taken to prevent future occurrences. Failure to meet this deadline could result in a reassessment of our partnership and potential penalties based on contractual obligations.
Letter Template For Critical Supplier Notification Samples
Letter template of urgent supplier communication regarding performance issues
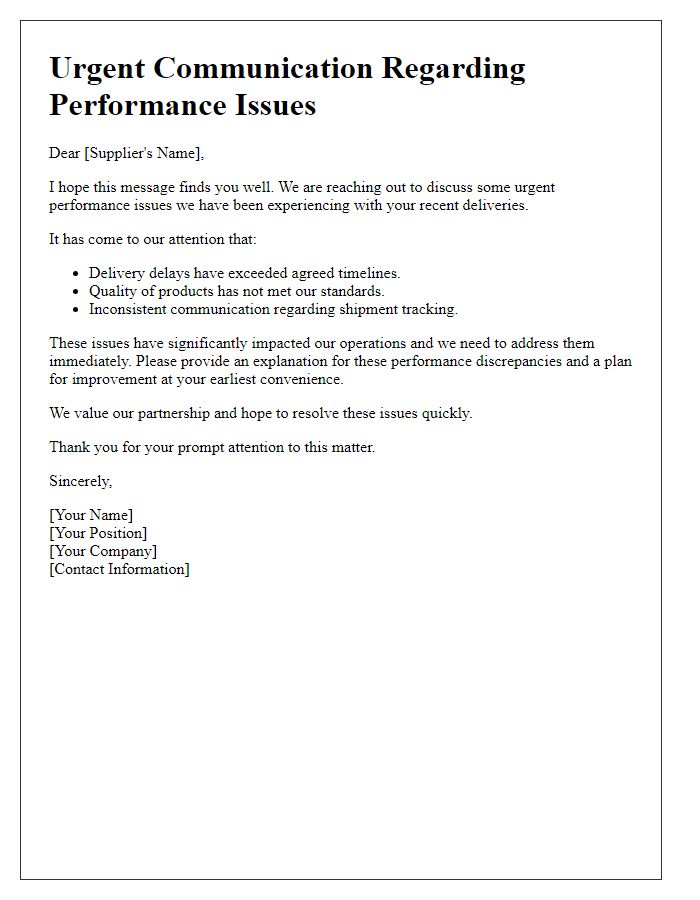
Letter template of critical notice to supplier about compliance failures
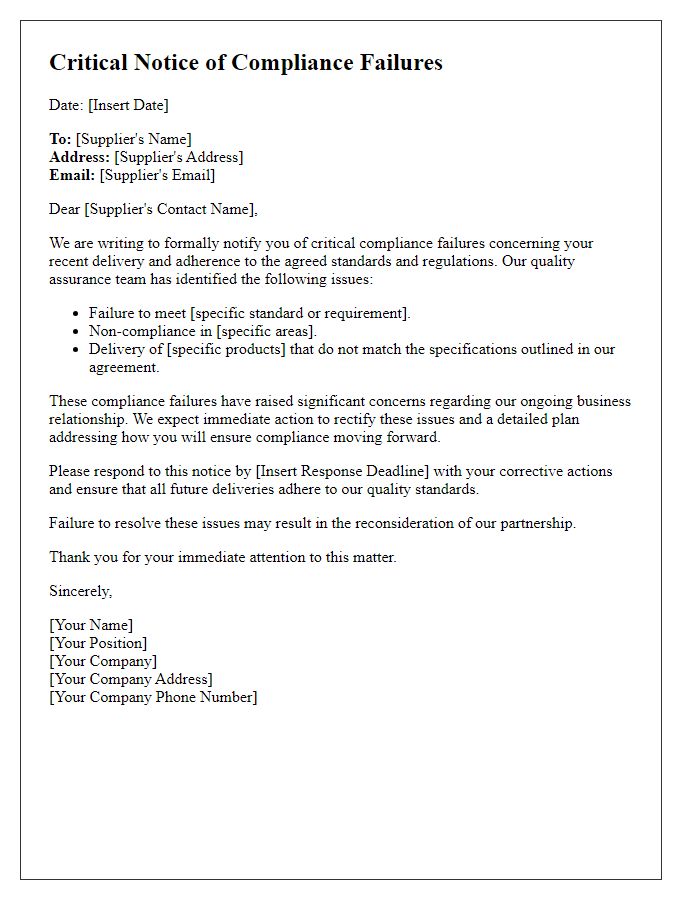
Letter template of crucial reminders for suppliers about quality standards
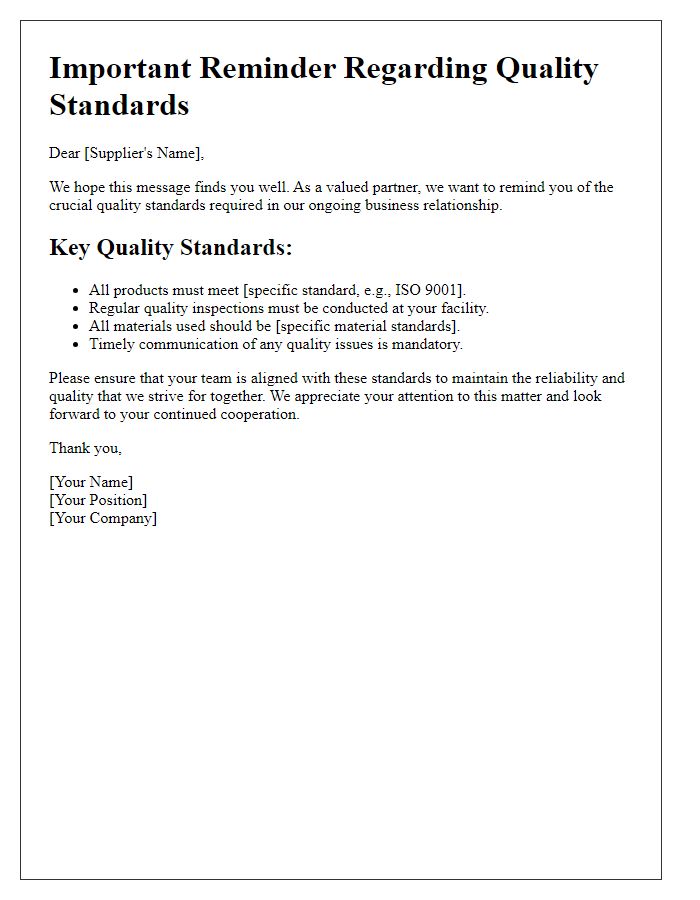
Comments