Upgrading production equipment is an exciting opportunity for businesses looking to enhance efficiency and boost output. With the rapid advancements in technology, investing in state-of-the-art machinery can streamline operations and reduce downtime. Additionally, modern equipment often promises improved safety and quality, ensuring your company stays competitive in a fast-paced market. Curious about how to make the most of this upgrade? Read on to discover essential tips and insights!
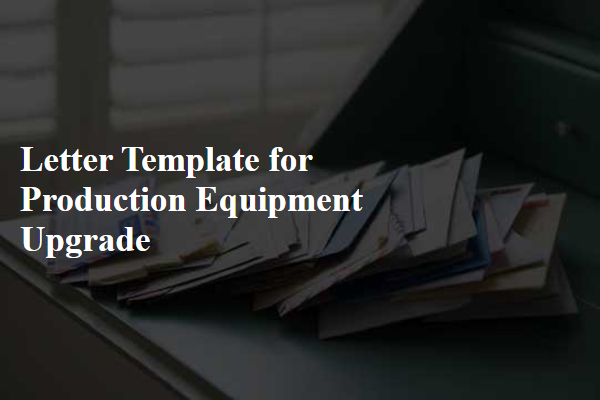
Subject line prioritization
Subject line prioritization significantly impacts the effectiveness of communication regarding production equipment upgrades. Effective subject lines should include specific details such as machinery type, intended upgrades, and urgency to capture attention. For instance, a subject line like "Immediate Action Required: Upgrade CNC Milling Machines for Enhanced Efficiency" clearly conveys the topic and need for prompt attention. By incorporating relevant keywords, such as "cost reduction" or "production capacity increase," decision-makers can quickly assess the importance of the message. Additionally, utilizing clear formatting and avoiding vague terms ensures that the intended audience can easily prioritize the communication amidst other operational considerations.
Recipient's title and name
A comprehensive evaluation of outdated production equipment can significantly enhance operational efficiency in manufacturing facilities like GreenTech Industries in Chicago. Upgrading equipment, particularly in critical areas such as assembly lines and quality control stations, can reduce downtime and improve speed, directly impacting production rates. For example, implementing advanced CNC (Computer Numerical Control) machines can increase precision in part fabrication by up to 20%, leading to higher quality products. Additionally, integrating automation technologies, like collaborative robots (cobots), can streamline workflows, allowing human workers to focus on complex tasks while machines handle repetitive actions. Modernizing this infrastructure not only boosts productivity but can also enhance worker safety and reduce operational costs over time.
Purpose of upgrade
Upgrading production equipment is essential for enhancing operational efficiency and meeting industry demands. Modern machinery, like advanced CNC machines, can significantly improve precision and reduce waste, leading to increased product quality. Implementation of automation technologies, such as robotic arms, streamlines workflows and reduces labor costs, making production faster and more reliable. In addition, integrating Industry 4.0 solutions, including IoT devices for real-time monitoring, increases visibility across the production line. This upgrade supports sustainability efforts through energy-efficient equipment, which decreases carbon footprint while maintaining output levels, aligning with modern environmental standards. Overall, updating production equipment is a strategic investment, vital for sustaining competitiveness in the manufacturing landscape.
Benefits and improvements
Upgrading production equipment can significantly enhance operational efficiency and output quality in manufacturing facilities, such as automotive plants. Modern machinery, equipped with advanced automation technologies, can increase output by up to 30% while reducing energy consumption by 20%, resulting in lower operational costs. Enhanced precision in manufacturing processes decreases waste rate by 15%, ensuring more sustainable production practices. Additional features, like real-time data analytics, improve decision-making by providing insights into equipment performance, allowing for timely maintenance and minimizing downtime. Implementing upgraded safety mechanisms, such as automated emergency stops, can also reduce workplace accidents by 25%, promoting a safer environment for employees. Overall, the investment in modern production equipment not only boosts productivity but also aligns with industry standards for quality and safety.
Call to action
Production equipment upgrades enhance manufacturing efficiency, reduce operational costs, and improve product quality. Modern machinery, such as CNC machines (Computer Numerical Control) and robotics, can significantly increase production rates by up to 30% while minimizing human error. Investing in advanced technologies, like IoT (Internet of Things) sensors for real-time monitoring, can lead to smarter maintenance schedules and decreased downtime, ultimately boosting overall productivity in facilities located in industrial parks. Upgrading equipment not only meets increasing consumer demand but also aligns with sustainability goals by reducing waste and energy consumption. Engaging with suppliers at trade expos can help identify cutting-edge solutions tailored to specific production needs.
Comments