In the ever-evolving world of supply chain management, understanding the risks involved is more crucial than ever. Businesses face a myriad of challenges, from fluctuating global markets to unexpected disruptions that can impact operations. By conducting a comprehensive supply chain risk assessment, companies can identify vulnerabilities and develop strategies to mitigate potential issues. Curious about how to effectively carry out this assessment and safeguard your operations? Read on to discover valuable insights!
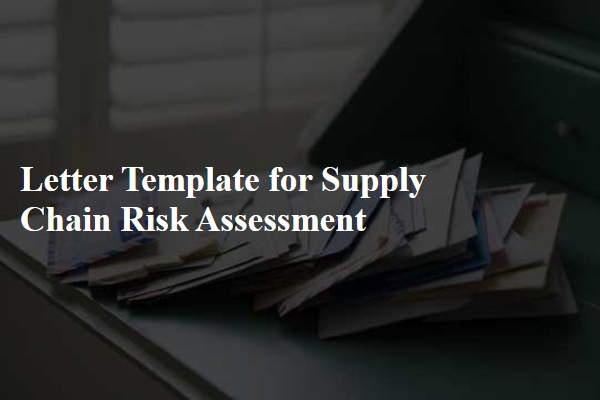
Identification of potential risks
Conducting a supply chain risk assessment is crucial for identifying potential vulnerabilities within the procurement and distribution processes. Key risks include supplier insolvency, which poses a threat when companies like XYZ Corp cannot fulfill orders due to financial difficulties. Natural disasters, such as hurricanes or earthquakes, can disrupt logistics, particularly in regions like the Southeast United States where storms frequently occur. Additionally, geopolitical tensions can impact materials imported from countries like China, where trade restrictions could hinder supply continuity. Cybersecurity threats also represent a significant risk, with ransomware attacks potentially compromising sensitive data and halting operations. Furthermore, regulatory changes in the European Union may affect compliance standards, requiring swift adaptations by businesses. Understanding these risks enables proactive measures, enhancing resilience in the supply chain.
Mitigation strategies and contingency plans
Supply chain disruptions can arise from various sources, impacting the flow of goods and services. Natural disasters, including hurricanes or earthquakes, can halt production and transportation. For instance, Hurricane Katrina in 2005 caused immense delays in the Gulf Coast, affecting supply chains nationwide. Geopolitical tensions, such as the trade disputes between the United States and China, can lead to increased tariffs and delays in shipments. Mitigation strategies include diversifying suppliers to reduce dependency on a single source, which can enhance resilience against disruptions. Employing technologies like AI and blockchain can improve visibility, allowing for real-time monitoring of supply chain activities. Additionally, contingency plans, such as establishing alternative routes for shipping or securing extra inventory during peak seasons, can effectively minimize the impact of unforeseen events. Salesforce, a leader in cloud-based software, exemplifies how predictive analytics can forecast potential supply chain risks, enabling proactive measures to ensure stability and continuity.
Supplier reliability and performance metrics
Supplier reliability is crucial for maintaining operational efficiency in supply chains, especially in manufacturing sectors like automotive and electronics. Key performance metrics, including on-time delivery rates (ideally exceeding 95 percent), defect rates (should be below 1 percent), and responsiveness (response time within 24 hours for inquiries), play vital roles in evaluating supplier performance. Tools such as scorecards can systematically track these metrics, compiling data from various sources, including purchase orders and performance reviews. Understanding regional factors, such as natural disasters in the Southeast Asia region that may disrupt shipping channels, can further enhance risk assessment processes. Regular audits and feedback loops ensure continual improvement in supplier relationships, fostering reliability and reducing risks associated with supply chain disruptions.
Regulatory and compliance requirements
Regulatory compliance in supply chain management involves adhering to laws and regulations imposed by governing bodies, such as the Federal Trade Commission (FTC) and the European Union (EU) General Data Protection Regulation (GDPR). Companies must ensure that suppliers follow standards (ISO 9001 for quality management, for instance) to avoid potential fines or delays in shipments. These requirements may vary by region, requiring businesses to assess risks associated with non-compliance, which can lead to legal repercussions and reputational damage. Supply chain audits (often conducted annually) help identify compliance gaps, ensuring that manufacturers, distributors, and logistics partners adhere to environmental regulations (such as the Clean Air Act in the USA). Understanding these regulatory frameworks is crucial for maintaining smooth operations and fostering trust in the supply chain.
Regular monitoring and assessment schedules
Regular monitoring and assessment schedules are essential in effective supply chain risk management. Practices often include bi-annual reviews of supplier reliability, focusing on performance metrics such as on-time delivery rates, quality defect percentages, and inventory turnover ratios. These assessments are conducted in key locations such as distribution centers, manufacturing facilities, and third-party logistics providers to ensure comprehensive evaluation. Additionally, organizations often implement risk scoring systems to categorize risk levels based on factors like geopolitical events, natural disasters, or sudden regulatory changes. Utilizing advanced analytics and data visualization tools helps identify emerging trends and vulnerabilities, allowing proactive adjustments in procurement strategies and inventory management. Effective communication channels with suppliers enhance collaboration and transparency, critical for navigating potential disruptions in global supply chains.
Comments