Are you exploring the world of precision engineering and considering a loan project to support your ambitions? Whether you're looking to upgrade your equipment or expand your facility, understanding the nuances of financing in this specialized field can make all the difference. In this article, we'll break down the key elements you need to know about securing a loan for your precision engineering project, from potential pitfalls to valuable tips for success. So, if you're ready to elevate your engineering game, keep reading to discover everything you need to know!
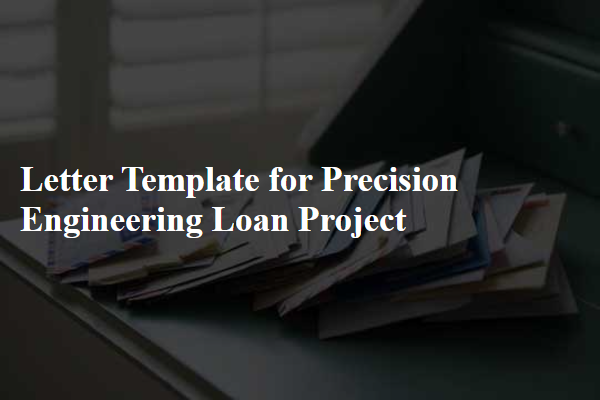
Project Overview and Objectives
The precision engineering loan project focuses on advancing manufacturing techniques through innovative technology. Key objectives include enhancing production efficiency by 30%, reducing material waste by 20%, and improving product quality to meet industry standards such as ISO 9001. The project will implement advanced machining processes, including Computer Numerical Control (CNC) machining, to achieve higher accuracy. Additionally, the initiative involves upgrading equipment at facilities located in advanced manufacturing hubs, such as Silicon Valley, known for its high-tech industries. Collaborations with research institutions will foster knowledge transfer and drive innovation, aiming for a competitive edge in the global market.
Detailed Cost and Financial Plan
The precision engineering loan project outlines a comprehensive financial plan detailing projected costs associated with advanced manufacturing equipment, such as CNC machines valued at approximately $150,000 each, necessary for enhancing production capabilities in a state-of-the-art facility located in Houston, Texas. Initial startup costs include facility modifications estimated at $50,000 to accommodate the new machinery and ensure optimal workflow. Additionally, raw materials, including high-grade stainless steel and aluminum alloys, are projected to cost around $30,000 for the first quarter of operation. Labor expenses, factoring in skilled technicians with an average salary of $70,000 annually, will also significantly contribute to the budget. An estimated $10,000 will be allocated for training programs to ensure employee expertise in operating new technologies efficiently. Furthermore, contingency expenses are allocated at 15% of total projected costs to safeguard against unforeseen circumstances, ensuring overall financial stability and project viability.
Technical Specifications and Expertise
Precision engineering projects require meticulous attention to technical specifications and robust expertise to ensure successful execution. Precision machining involves creating components with tolerances of less than 0.01 millimeters, necessitating advanced tools such as CNC (Computer Numerical Control) machines and laser cutters. In addition, materials like high-grade aluminum and titanium alloy often feature in these projects due to their lightweight properties and exceptional strength-to-weight ratios. Knowledge in the field utilizes CAD (Computer-Aided Design) software for accurate designs, ensuring that components align with industry standards such as ISO 9001 for quality management systems. Furthermore, expert teams often comprise professionals with backgrounds in mechanical engineering, materials science, and quality assurance, ensuring that every phase of production receives valuable insights critical for maintaining precision and reliability in complex assemblies.
Risk Assessment and Mitigation Strategies
Precision engineering projects, particularly those involving high-stakes technologies like aerospace components, robotics, or medical devices, entail various risks that must be assessed meticulously. These risks include potential equipment failures, which can lead to production delays and cost overruns, particularly in critical systems like CNC machines or 3D printers. Regulatory compliance risks, particularly when adhering to ISO 9001 standards or FDA regulations for medical devices, necessitate stringent quality control measures. Financial risks, influenced by fluctuating material costs such as titanium or carbon fiber, can impact project budgets significantly. Consequently, implementing robust mitigation strategies is crucial; this could involve establishing contingency funds, investing in advanced monitoring technologies to predict equipment malfunctions, and conducting regular training sessions for staff on compliance and quality assurance practices. By prioritizing these strategies, organizations can enhance their resilience against the multifaceted risks associated with precision engineering projects.
Return on Investment and Economic Impact
Precision engineering projects often encompass advanced manufacturing techniques, specialized machinery, and skilled labor. These initiatives can lead to significant enhancements in production efficiency, quality control, and customer satisfaction. Estimated returns on investment (ROI) in this sector typically range from 15% to 25% over five years, depending on market demand and operational improvements. Economic impacts include job creation in regions with precision engineering facilities, contributing to local economies. For instance, a new facility in Ohio can create upwards of 100 jobs and generate $5 million annually in local spending. The incorporation of innovative technologies, such as CNC machining and 3D printing, further drives competitive advantage and profitability, aiding in sustainable growth for both businesses and the economy.
Letter Template For Precision Engineering Loan Project Samples
Letter template of loan application for precision engineering project funding
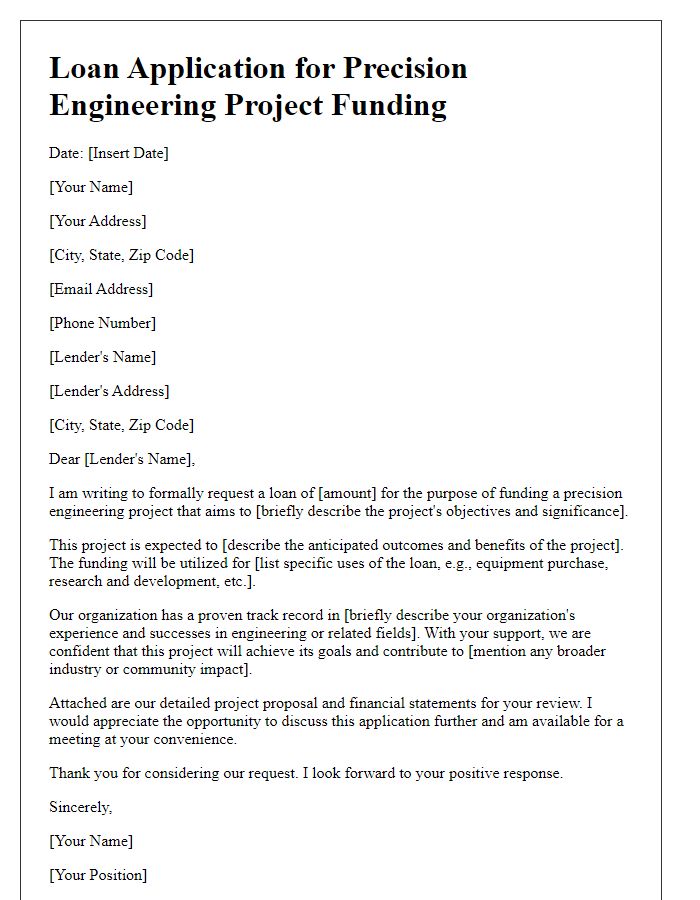
Letter template of funding request for precision engineering development
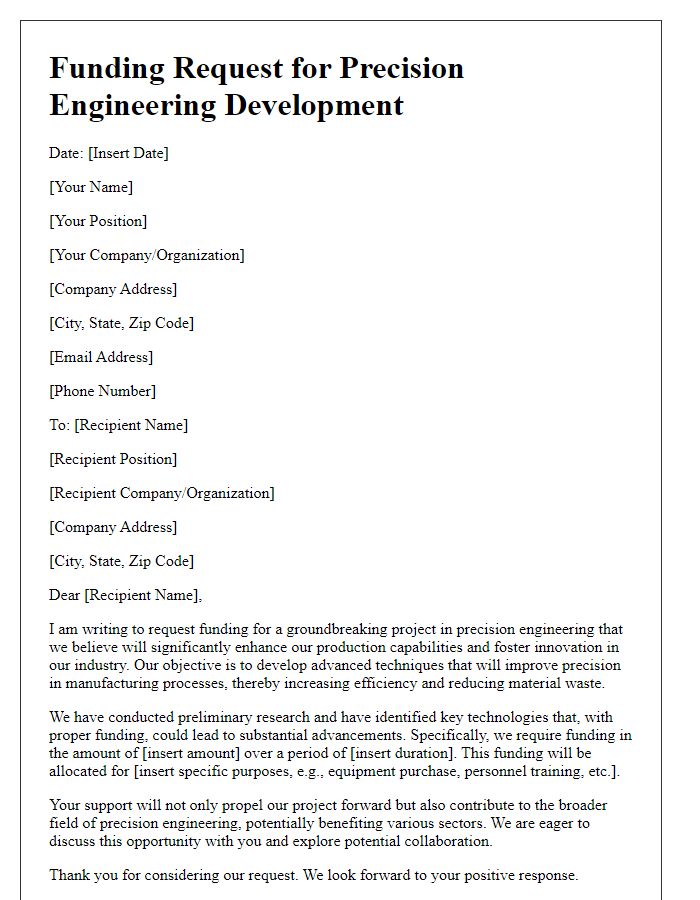
Letter template of financing proposal for precision engineering initiatives
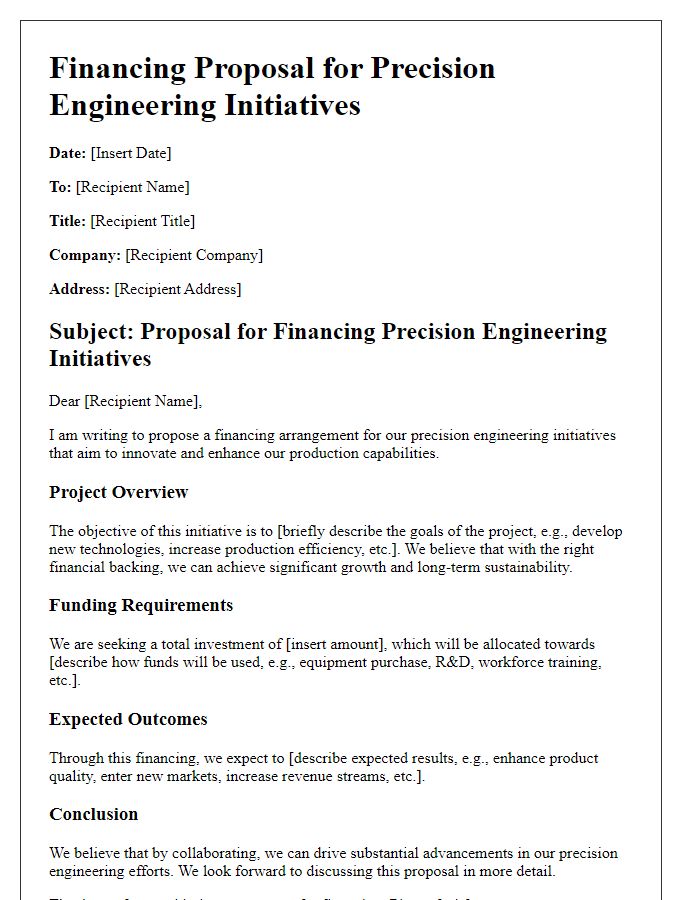
Letter template of investment application for precision engineering projects
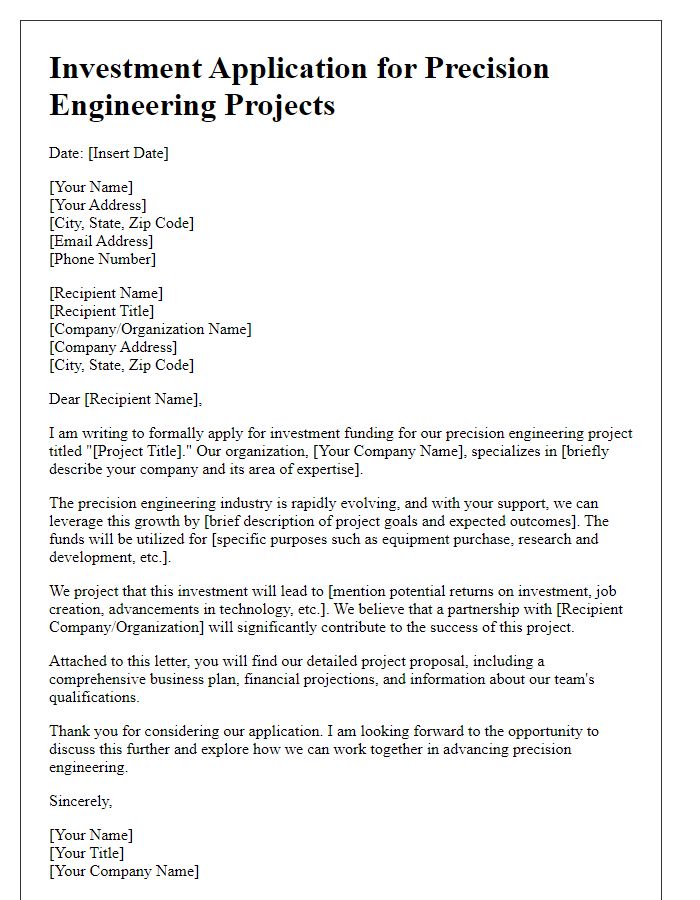
Letter template of sponsorship request for precision engineering research
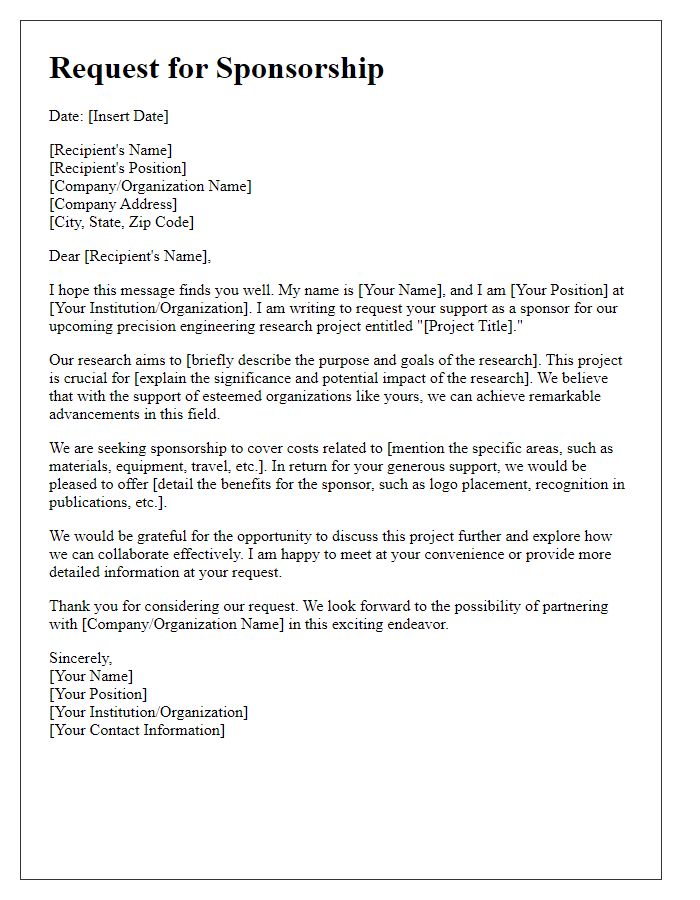
Letter template of partnership inquiry for precision engineering ventures
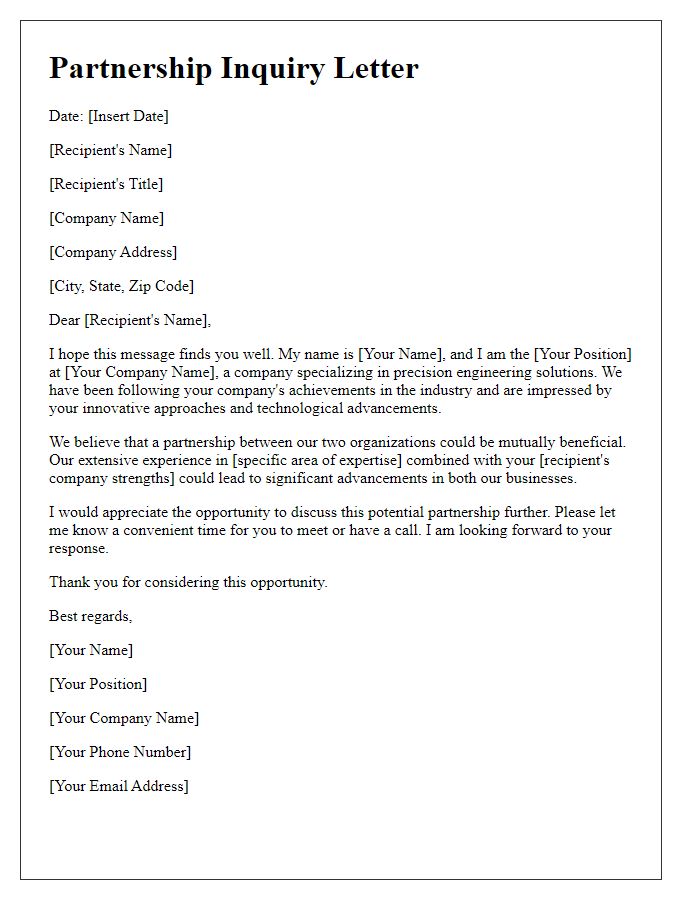
Letter template of financial support request for precision engineering solutions
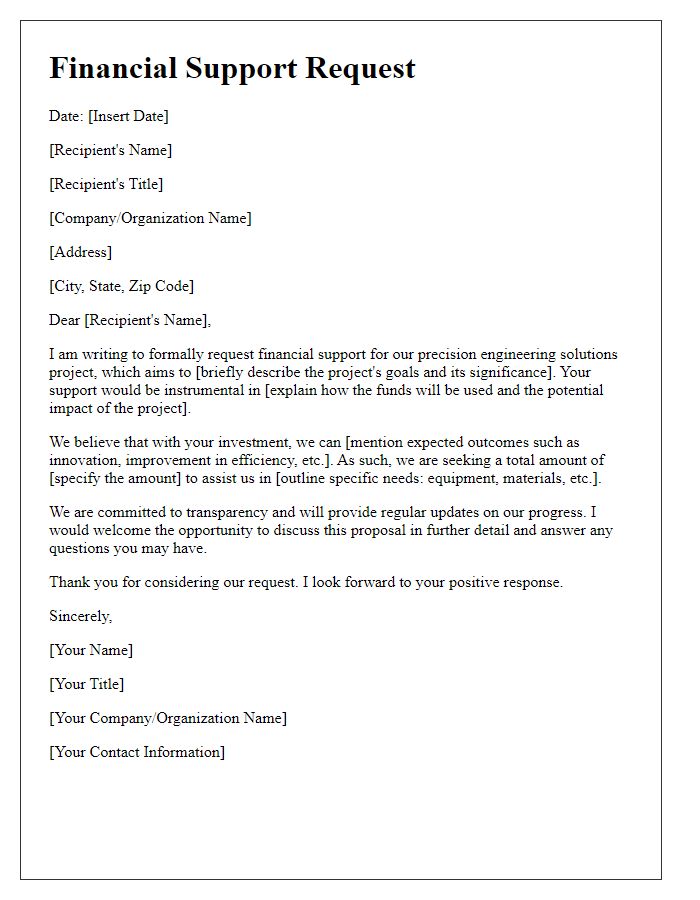
Comments