Are you looking to enhance your contractor quality control documentation? A well-structured letter template can make all the difference in ensuring clarity and professionalism in your communications. This resource not only streamlines the quality control process but also sets clear expectations for contractors. Dive deeper into this topic to discover the essential elements of an effective quality control letter template!
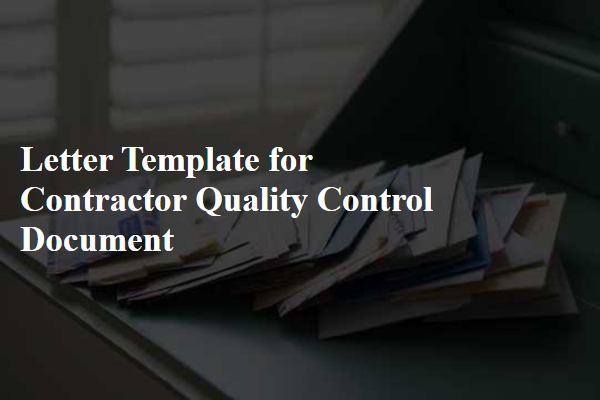
Project Details
Creating a Contractor Quality Control document requires thorough attention to detail, particularly concerning project specifics. The document should encompass vital project details, such as the project name, often tied to significant developments in a specific locale, which also includes the project number that helps in tracking and management. The start and finish dates, marked as crucial milestones, define the project timeline, pivotal for scheduling and resource allocation. Location specifics, usually denoted by address, must include city, state, and applicable zip code for clarity within record-keeping. Contractual parties' details should include the contractor's name, a crucial entity that signifies responsibility for project delivery, as well as client information to ensure accountability. Additionally, references to relevant standards or regulations, such as ISO 9001 for quality management systems, can enrich the document's context and establish a foundation for quality assurance processes throughout the project lifecycle.
Quality Standards and Compliance
Quality control documents for contractors must adhere to industry regulations and standards, ensuring that safety measures and construction practices align with local building codes. The International Organization for Standardization (ISO), for instance, emphasizes quality management principles that guide contractors on maintaining consistent quality throughout projects. Specific compliance benchmarks, like the ASTM standards (American Society for Testing and Materials), set thresholds for material performance and reliability in construction. Documentation typically includes checklists, inspection protocols, and quality assurance plans that monitor adherence to specifications during various phases of construction, such as grading, foundation work, and finishing. Reporting mechanisms are essential, providing data on non-conformance, corrective actions, and the effectiveness of quality control measures. Regular audits and assessments are recommended to identify areas needing improvement and to ensure continuous compliance with established quality standards.
Roles and Responsibilities
Quality control in construction projects involves crucial roles and responsibilities to ensure compliance with specifications and standards. Project managers oversee the entire process, coordinating quality control activities at each construction stage. Quality control inspectors conduct regular site inspections, assessing materials and workmanship against project standards and applicable regulations. Document controllers maintain accurate records of inspections, test results, and compliance reports for auditing purposes. Additionally, subcontractors are responsible for adhering to specified quality standards in their trades, reporting issues to project management. Effective communication among all parties, including architects and engineers, is essential for identifying and resolving quality concerns, ensuring the project remains on schedule and within budget.
Inspection and Testing Procedures
An inspection and testing procedure for contractor quality control emphasizes systematic verification of materials, equipment, and workmanship throughout construction projects. These procedures include specific assessments such as visual inspections, material sampling, and performance testing according to established standards like ASTM (American Society for Testing and Materials) or ISO (International Organization for Standardization). For concrete, slump tests and compressive strength tests are performed at designated intervals, ensuring compliance with project specifications. Additionally, safety measures must be documented, encompassing personal protective equipment (PPE) requirements and emergency protocols relevant to the construction site. Records of test results must be maintained meticulously, detailing the date, location, and responsible personnel, ensuring traceability and accountability throughout the construction timeline.
Documentation and Reporting Protocols
Quality control documentation plays a critical role in construction projects, particularly in adhering to standards and ensuring material compliance. Standard operating procedures often necessitate detailed documentation, including inspection reports, testing results, and corrective action logs. The American National Standards Institute (ANSI) outlines protocols for maintaining these records across phases of construction, from foundation pouring to final inspections. Accurate reporting ensures all team members understand project specifications, safety requirements (such as OSHA regulations), and material certifications (like ASTM compliance). Implementing a structured documentation system can improve transparency and accountability, facilitating smooth communication between contractors, subcontractors, and project managers while minimizing errors and rework.
Comments