In today's fast-paced business environment, cost reduction is not just a necessity but a strategic advantage. Companies are constantly seeking innovative ways to streamline operations and maximize efficiency without sacrificing quality. This article will explore effective cost reduction strategies that can transform your organizationâs financial health and operational effectiveness. So grab a cup of coffee and join me as we dive into practical tips that can lead to substantial savings and enhanced performance!
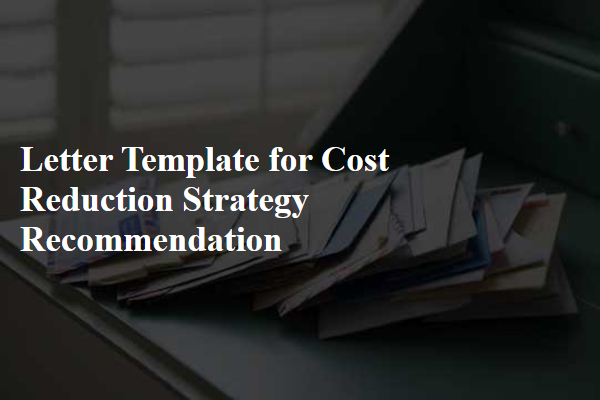
Objective Clarification
Cost reduction strategies, such as Lean Management and Six Sigma, focus on improving operational efficiency within organizations, particularly in manufacturing sectors like automotive and consumer goods. Implementing these strategies can lead to a significant decrease in waste (up to 30% reduction) and enhance productivity (potentially increasing output by 20%). The objective clarification process involves identifying key areas for improvement, such as supply chain optimization (reducing logistics costs by 15%), workforce training (increasing employee productivity through skill enhancement), and technology integration (adopting automation to streamline processes). Companies like Toyota and GE have successfully applied these methodologies to achieve substantial financial savings while maintaining quality standards.
Targeted Areas for Cost Reduction
Implementing a cost reduction strategy can significantly enhance organizational efficiency and profitability. Key areas for potential savings include operational expenses related to supply chain management, such as reducing inventory holding costs by optimizing stock levels, which can be improved by employing just-in-time (JIT) inventory systems. Labor costs can be addressed by reviewing staffing levels against productivity metrics, encouraging a culture of cross-training employees, and investing in automation technologies, potentially resulting in a 20% reduction in workforce-related expenditures. Additionally, energy consumption can be minimized through investments in energy-efficient infrastructure and renewable energy sources (e.g., solar panels), which can lead to a reduction in utility costs by 30%. Furthermore, re-evaluating supplier contracts for better terms and exploring alternative sourcing options can enhance procurement efficiency and achieve significant cost savings. Regularly analyzing these targeted areas ensures sustainable financial health for the organization in a competitive marketplace.
Data-Driven Analysis and Insights
A cost reduction strategy can be effectively guided by data-driven analysis, focusing on key operational metrics. Comprehensive analysis of historical spending patterns can uncover areas where expenses can be minimized, such as material costs linked to suppliers like Company X or service expenses associated with Vendor Y. Implementing a benchmarking approach against industry standards provides context for potential savings, highlighting variances that result in inefficiencies. Process optimization initiatives, informed by data insights, can streamline workflows, reducing overhead costs and increasing productivity across departments. Additionally, examining pricing trends, demand forecasting, and inventory management metrics can lead to improved purchasing strategies, ultimately contributing to lower costs and enhanced profit margins for the organization.
Strategic Implementation Plan
A Strategic Implementation Plan for cost reduction strategies can initiate significant enhancements in organizational efficiency. This plan typically encompasses several key areas: operational efficiency improvements, resource optimization, and technology upgrades. For instance, implementing a lean manufacturing approach can decrease waste by up to 30%, enhancing productivity within production facilities. Thorough analysis of supply chain management, focusing on reducing procurement costs through strategic sourcing, can yield up to 15% savings annually. Additionally, investing in automation technologies, like robotic process automation (RPA), can further streamline operations, potentially lowering labor costs by 20% in administrative roles. Specific milestones, timelines, and responsible parties for each initiative ensure comprehensive tracking of progress, ultimately aligning with the organization's overall financial targets. Regular reviews and adjustments to the plan will facilitate adaptability to changing market conditions and drive sustained cost savings.
Expected Outcomes and Benefits
Implementing a cost reduction strategy can significantly enhance a company's financial health, leading to improved profit margins and long-term sustainability. Expected outcomes include a reduction in operational expenses, where companies can save anywhere from 10% to 30% through efficient resource allocation and automation of repetitive tasks. Enhanced cash flow is anticipated, allowing for reinvestment into critical areas such as research and development, which can foster innovation. Employee productivity can increase, driven by streamlined processes and reduced bureaucratic hurdles. Improved customer satisfaction may result from quicker service delivery through optimized supply chain management, such as adopting lean methodologies. Overall, these strategies can contribute to a competitive advantage in densely populated markets, positioning the company for future growth and adaptability to market changes.
Comments