Are you looking to improve your organization's operational efficiency? In today's fast-paced business environment, understanding where you stand compared to your peers can provide invaluable insights. Benchmarking not only highlights areas for improvement but also helps identify best practices that can propel your operations to new heights. Dive into our article to explore effective benchmarking strategies and discover how to elevate your operational performance!
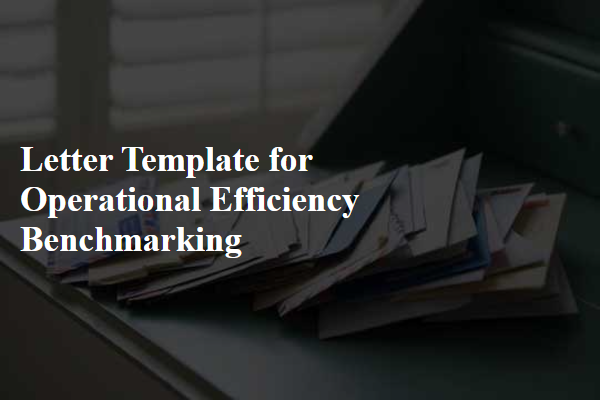
Clear Objectives
Operational efficiency benchmarking involves setting clear KPI (Key Performance Indicators) to measure performance. Organizations often define benchmarks based on industry standards to assess productivity levels across various departments. For example, manufacturing plants may focus on output rates (units produced per hour) and waste reduction percentages. Service-based companies might evaluate response times (customer queries resolved within 24 hours). Clear objectives ensure alignment among teams, enhancing communication and accountability. This structured approach can result in improved resource allocation and strategic decision-making, ultimately leading to increased profitability and competitive advantage in the market.
Key Performance Indicators (KPIs)
Operational efficiency benchmarking involves the evaluation of Key Performance Indicators (KPIs) to measure the performance of a business against industry standards and best practices. Specific KPIs such as Cost per Unit ($), Overall Equipment Effectiveness (OEE, expressed as a percentage), and Order Fulfillment Time (in hours or days) play crucial roles in determining operational effectiveness. A well-structured analysis may include data from various sectors, encompassing Manufacturing, Logistics, and Customer Service departments, to identify gaps and areas for improvement. Regular assessments, ideally quarterly, can provide insights into productivity trends, revealing opportunities for enhanced process optimization and resource allocation across departments. Collaboration with industry leaders and participation in benchmarking studies can further enrich the evaluation, offering valuable comparative data and actionable strategies for advancing operational practices.
Data Collection Methods
Operational efficiency benchmarking involves gathering and analyzing data to evaluate performance against industry standards or competitors. Common data collection methods include surveys, which gather quantitative and qualitative insights from employees or customers, and interviews that provide in-depth understanding of processes and challenges. Observational studies involve monitoring workflows in real-time, allowing for identification of inefficiencies. Time tracking tools can measure the duration of specific tasks, highlighting areas for improvement. Additionally, utilizing software analytics can reveal usage patterns and operational bottlenecks. Industry reports and case studies from organizations such as McKinsey or Deloitte offer comparative data for contextual analysis. Employing these methods creates a comprehensive data repository for effective benchmarking.
Industry Comparison Metrics
Operational efficiency benchmarking involves analyzing key performance indicators (KPIs) across various industries to identify best practices and areas for improvement. Metrics such as Overall Equipment Effectiveness (OEE), which quantifies productivity by measuring availability, performance, and quality, are critical. Industries like manufacturing, healthcare, and logistics utilize these benchmarks to assess resource utilization. Examples include the pharmaceutical industry's average OEE benchmark of 85%, while the automotive sector often aims for 90% or higher. Understanding labor productivity rates, such as revenue per employee, additionally allows organizations to compare against industry averages; for instance, the technology sector often reports figures around $200,000 per employee. Effective benchmarking enables companies to streamline processes, reduce waste, and enhance customer satisfaction, promoting increased competitiveness in their respective markets.
Actionable Insights
Actionable insights derived from operational efficiency benchmarking reveal critical opportunities for improvement in organizational processes. Identifying key performance indicators (KPIs) such as cycle time, productivity rates, and resource utilization can provide a clear picture of operational performance across various departments. Utilizing data analytics tools can help visualize trends, such as a 15% decrease in production time since implementing lean methodologies, highlighting areas for further optimization. Additionally, comparative analysis against industry standards (for instance, the manufacturing sector average of 80% equipment effectiveness) can drive strategic initiatives aimed at enhancing operational capabilities, reducing waste, and increasing overall profitability. Employing best practices from high-performing organizations can lead to significant enhancements in workflow efficiency and resource allocation.
Comments