Are you gearing up for a construction project and wondering how to ensure everything runs smoothly? Proper equipment inspection is crucial to maintaining safety and efficiency on-site. In this article, we'll discuss the key steps you need to take to conduct thorough inspections and the benefits they bring to your project. So, grab your hard hat and let's dive in to uncover the best practices for equipment inspection!

Project Name and Location
Construction equipment inspections are essential for ensuring safety and compliance on sites like the Maple Street Bridge Project in Springfield, Massachusetts. Heavy machinery such as cranes and excavators, regularly exceeding weight limits of 20 tons, must undergo thorough evaluations for operational efficiency and structural integrity. In addition, safety features like emergency stop buttons and backup alarms should be tested to prevent accidents. Regular inspections can uncover potential issues, aiding in prolonging the lifespan of equipment while also adhering to Occupational Safety and Health Administration (OSHA) regulations, which play a crucial role in maintaining worksite safety standards.
Inspection Date and Time
The construction project equipment inspection occurs on March 15, 2024, at 10:00 AM, at the Riverside Development Site, located at 123 River Road, Springfield. This inspection focuses on essential machinery, including excavators, forklifts, and cranes, ensuring that each piece of equipment meets safety standards and is operational. Inspection procedures involve assessing hydraulic systems, engine performance, and overall structural integrity, with adherence to OSHA regulations and manufacturer specifications. Moreover, a thorough review of maintenance logs and safety certifications will be conducted to confirm compliance with industry best practices.
Equipment List and Specifications
The construction project equipment inspection requires a comprehensive Equipment List and Specifications to ensure all machinery meets safety and operational standards. Key equipment includes crane models such as the Liebherr LTM 1200-5.1, capable of lifting up to 200 tons, and excavators like the Caterpillar 336F, which offers a digging depth of 22 feet. Each piece of equipment should be evaluated for compliance with OSHA regulations and equipment manuals. Inspection criteria must address hydraulic systems, track conditions, and safety features such as emergency stop mechanisms. Additionally, operator competency must be verified through certifications, ensuring equipment is operated by qualified personnel. Maintenance records need to be reviewed to confirm regular servicing aligns with manufacturer recommendations, promoting both safety and efficiency on the construction site.
Safety and Compliance Standards
Construction project equipment inspections are critical for ensuring the safety and compliance of machinery, such as cranes, excavators, and bulldozers, in the construction industry. These inspections, typically conducted quarterly or biannually, assess the operational condition and safety features of the equipment, aligning with OSHA (Occupational Safety and Health Administration) regulations. Inspectors examine key components, including hydraulic systems for leaks, braking systems for effectiveness, and safety devices like alarms and lights. Additionally, documentation is essential, registering findings in compliance with local state laws, which may vary, such as California's stringent safety regulations. Proper inspection helps prevent accidents on construction sites and ensures the longevity and efficiency of equipment, ultimately fostering a safer working environment.
Contact Information for Inspection Coordinator
Efficient communication is crucial for any construction project involving equipment inspection. The Inspection Coordinator serves as the main point of contact, ensuring that all equipment, such as cranes and excavators, meets compliance standards set by regulatory bodies, including OSHA (Occupational Safety and Health Administration). Utilizing detailed records from past inspections, the Coordinator also organizes schedules for inspections conducted by certified inspectors with expertise in construction machinery safety, often occurring at designated sites like active construction zones in urban areas. The Coordinator's responsibilities also include addressing any issues identified during inspections, coordinating repairs, and ensuring all equipment is certified for use within specified timeframes, thus minimizing delays and adhering to project deadlines.
Letter Template For Construction Project Equipment Inspection Samples
Letter template of equipment inspection for construction project compliance.
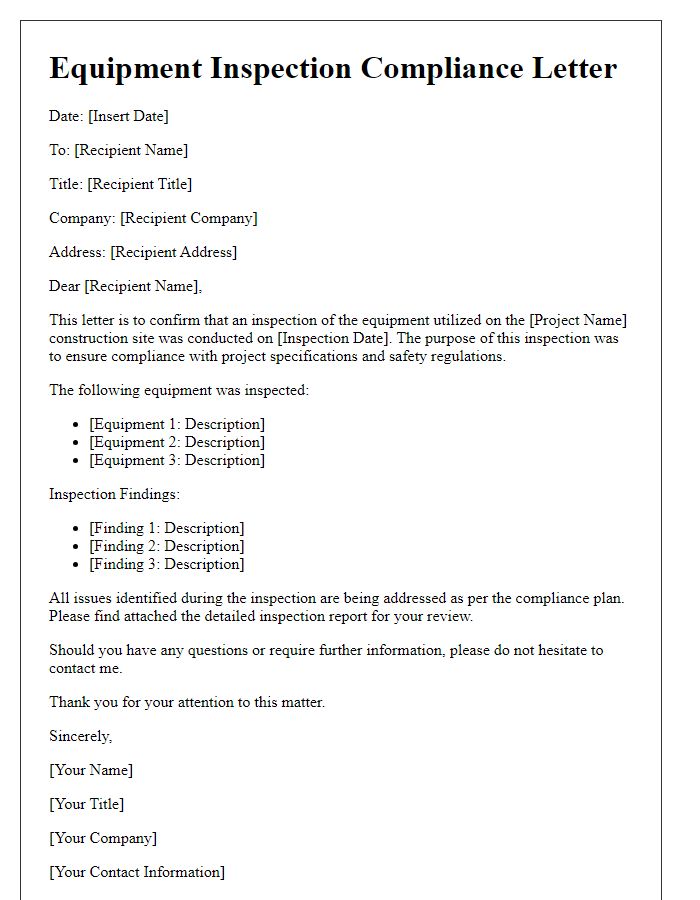
Letter template of construction equipment evaluation for safety standards.
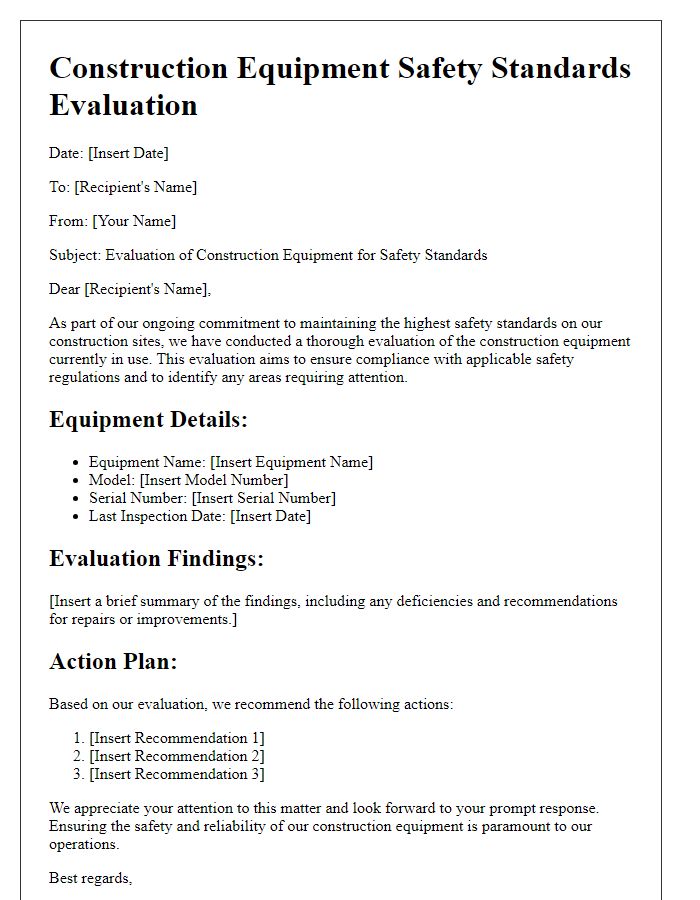
Letter template of post-inspection equipment review for construction site.
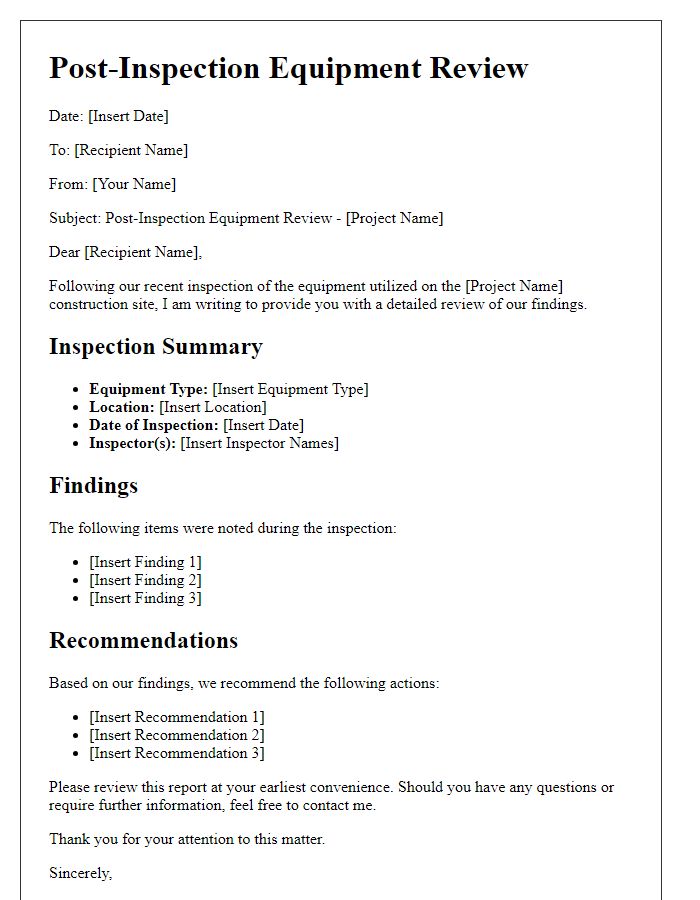
Letter template of heavy machinery safety evaluation for ongoing projects.
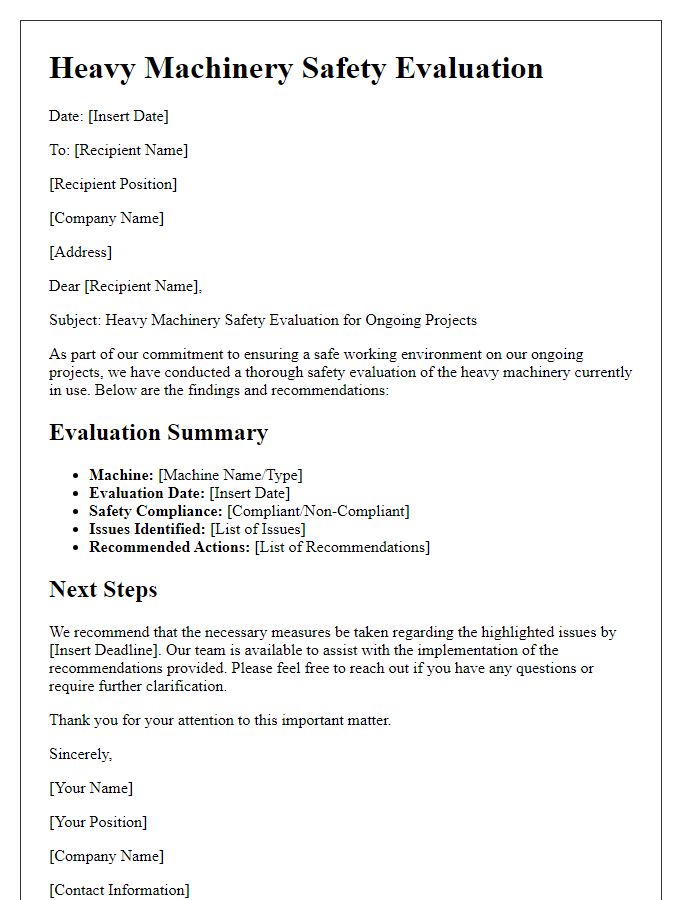
Letter template of scheduled equipment review for construction activities.
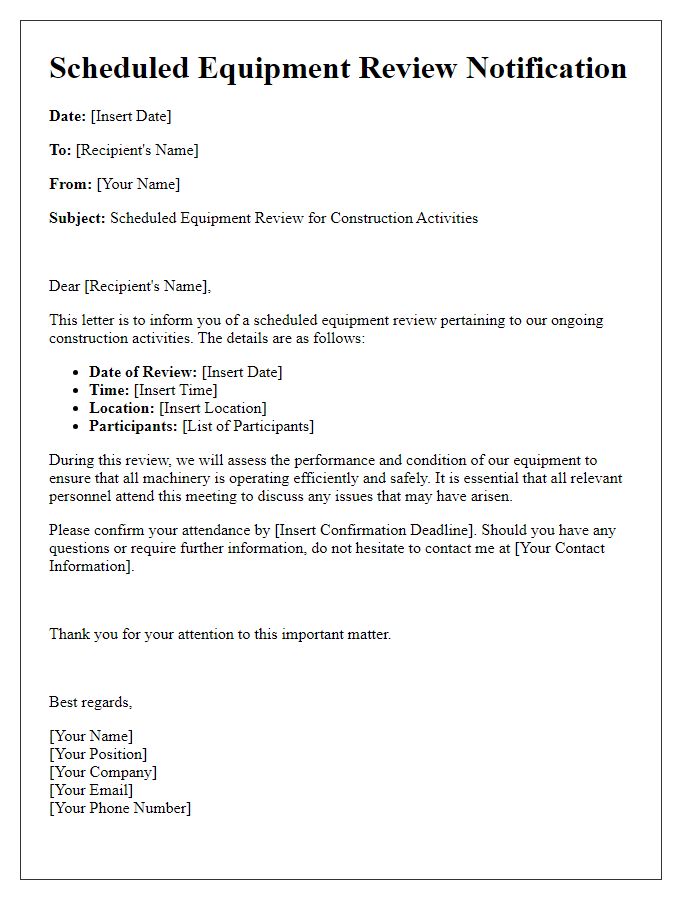
Comments