Are you looking to enhance your supply chain with reliable manufacturing partners? Understanding a vendor's capabilities is essential for making informed decisions that align with your business goals. In this article, weâll explore effective strategies for crafting an inquiry that helps you gauge a vendor's manufacturing capabilities. Stick around as we dive into tips that will ensure you get the answers you need!
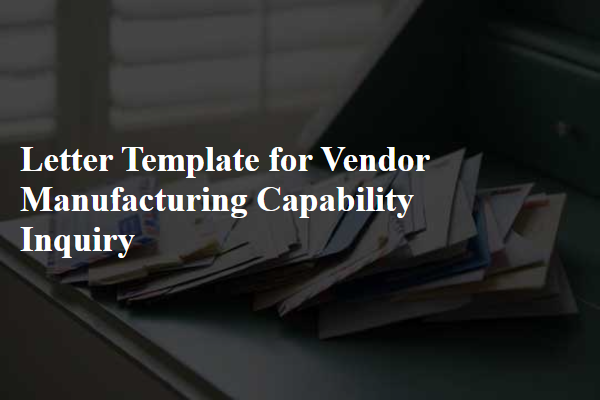
Contact Information
Contacting vendors to inquire about manufacturing capabilities requires a clear and concise approach. Vendors may represent diverse industries, so understanding specific areas of expertise, such as production capacity, technology used, quality assurance practices, and lead times, is essential. Including essential details like company size, certifications, and past project examples enriches the inquiry. Furthermore, requesting relevant documentation or references can enhance trust, ensuring potential collaboration aligns with business goals. Utilize professional tone while being direct and respectful in all communications.
Introduction and Purpose
Inquiring about manufacturing capabilities is crucial for establishing a successful partnership with vendors, particularly in industries such as electronics and textiles. A detailed inquiry can provide insights into the vendor's production capacity, technological capabilities, and adherence to quality standards. Companies often seek manufacturers who can meet specific requirements, such as ISO certification or the ability to scale production during peak demand seasons. A comprehensive manufacturing capability inquiry can include questions about recent changes in production processes, ongoing investments in automation technology, or product-specific expertise. Understanding these factors can help businesses determine if a vendor aligns with their strategic objectives and quality expectations.
Detailed Product Specifications
Inquiries regarding vendor manufacturing capabilities require specificity. Detailed product specifications encompass crucial elements such as material specifications (e.g., stainless steel or polypropylene), dimensions (e.g., length, width, height in millimeters), tolerances (e.g., +/- 0.1 mm), production rates (e.g., 100 units per hour), and quality certifications (e.g., ISO 9001). It is important to include the intended application of the product, such as automotive components or consumer electronics, to better assess the vendor's suitability. Furthermore, understanding the vendor's technology (e.g., CNC machining or injection molding), experience with similar products, and their capacity for customization (e.g., color options or branding) provides insight into their capabilities. Lead times for production and shipping logistics also should be clarified to align with project timelines.
Production Capacity and Lead Times
Manufacturers play a crucial role in the supply chain, determining production capacity and lead times that directly impact delivery schedules. Evaluating these capabilities involves assessing metrics such as maximum output per day or week and the average turnaround time for order fulfillment. For instance, a factory in Vietnam might have a production capacity of 10,000 units monthly for electronic components, with a typical lead time of four to six weeks for standard orders. Additional factors include workforce availability, machinery efficiency, and historical performance during peak seasons, which can all influence the reliability of promised delivery dates. Understanding these parameters aids businesses in making informed decisions regarding partnerships with manufacturers.
Quality Assurance and Certifications
Manufacturing capabilities significantly influence product quality and reliability, particularly in industries requiring stringent standards, such as pharmaceuticals and aerospace. Quality Assurance (QA) processes ensure products meet specifications through rigorous checks and evaluations. Certifications like ISO 9001, which indicates a commitment to quality management systems, and ISO 13485 for medical device manufacturing signify adherence to international standards. The vendor's facility, often located in strategic industrial hubs such as Shenzhen, China or Tijuana, Mexico, plays a crucial role in production consistency. Certifications by third-party organizations, including SGS or UL, provide additional assurance of quality and safety standards compliance, enhancing buyer confidence. Collectively, these factors determine the vendor's capability to deliver high-quality products on time.
Letter Template For Vendor Manufacturing Capability Inquiry Samples
Letter template of request for information on manufacturing capabilities
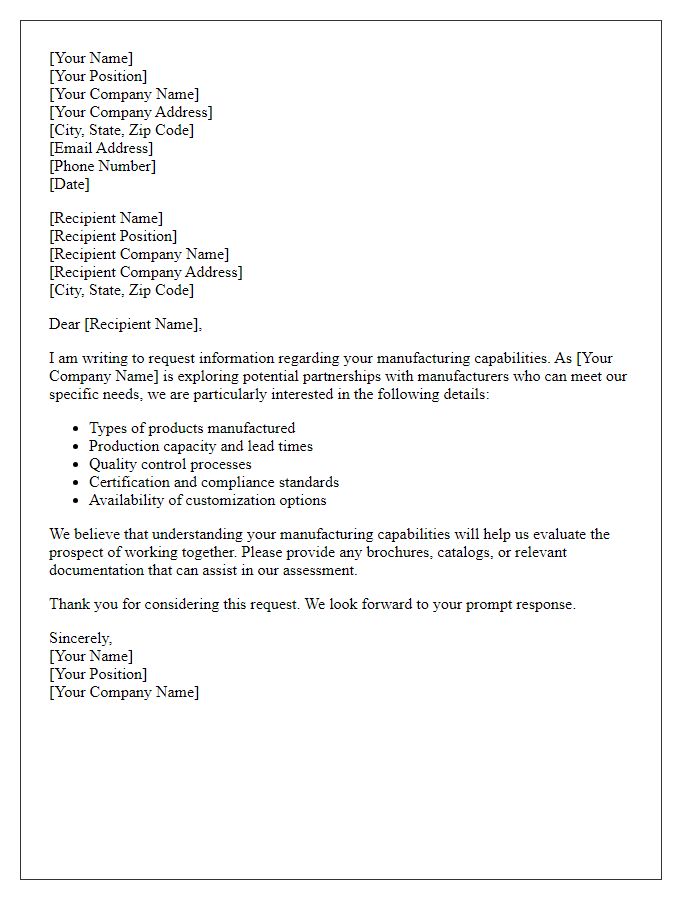
Letter template of request for details on vendor's manufacturing processes
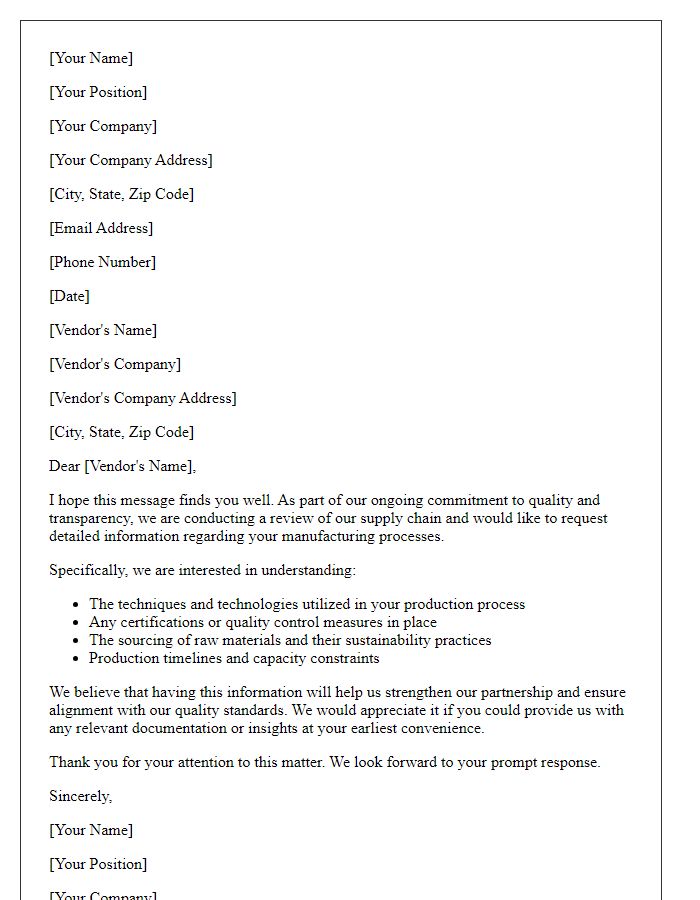
Comments