When it comes to maintaining safety standards in our operations, clear communication with our vendors is essential. Incidents can arise unexpectedly, and it's vital to document the details effectively to prevent future occurrences. A well-structured incident report not only keeps everyone informed but also fosters a culture of safety and accountability. Curious to learn how to create a comprehensive vendor safety incident report? Dive into the full article for tips and templates!
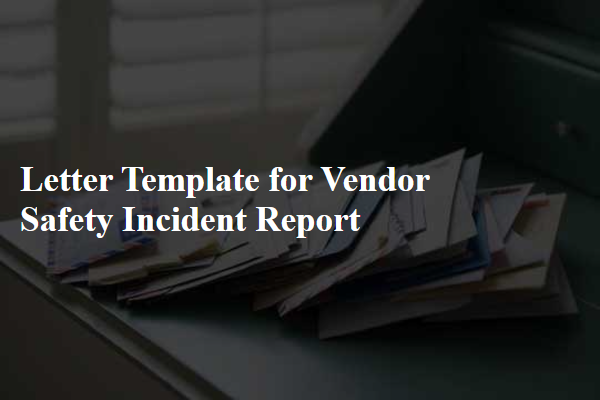
Incident Details
A safety incident report details occurrences that compromise safety standards in a workplace. Such reports include critical information like the date, time, and location of the incident, which can occur in various settings such as manufacturing plants, construction sites, or office environments. Specifics about the incident, such as "slip and fall" injuries, chemical spills, or equipment malfunctions, provide context for the event. In addition, the report should identify the individuals involved, indicating whether they are employees, contractors, or visitors, along with the severity of injuries sustained, if any. Furthermore, root cause analysis may be included to determine underlying factors contributing to the incident, enhancing future safety measures to prevent recurrence. The elements of the report culminate in creating an understanding of safety issues that arise within the organizational framework, emphasized by adherence to OSHA (Occupational Safety and Health Administration) regulations.
Vendor Information
Vendor information is crucial for effective incident reporting. It typically includes the vendor's name (such as "ABC Supply Co."), contact details (phone number, email address), physical location (complete address including city and zip code), and relevant company identification numbers (such as D-U-N-S number or tax ID). Furthermore, vendor-specific data may encompass safety certifications (like OSHA compliance) and historical incident reports that outline previous safety issues or corrective actions taken. This information helps in assessing vendor accountability and compliance with safety regulations, ensuring a thorough investigation into any incidents that may arise.
Safety Measures Taken
Following the recent vendor safety incident, immediate measures were implemented to enhance worker protection and reduce hazardous risks. Safety audits across all operational areas were conducted, pinpointing critical zones where safety protocols lacked adherence. Workshops on emergency procedures were organized, ensuring all employees are equipped to respond effectively to potential incidents. Personal Protective Equipment (PPE), including safety helmets, gloves, and masks, were distributed to all staff members, aligning with Occupational Safety and Health Administration (OSHA) standards. Safety signage was prominently displayed at strategic locations within the facility, reminding workers of potential hazards and necessary precautions. Furthermore, safety drills were scheduled monthly to reinforce readiness and compliance with safety regulations.
Witness Statements
In-depth witness statements during vendor safety incidents are critical for accurate assessments and timely resolutions. Eyewitnesses, often employees present at the scene, provide detailed accounts of events leading to accidents, such as machinery malfunctions or safety protocol breaches. These statements should include specifics such as the date (e.g., September 21, 2023), time (e.g., 2:15 PM), and location (such as the warehouse area near loading docks at Supplier LLC's main facility). Witnesses may describe the sequence of events, including equipment involved (e.g., forklift model Toyota 8FBE), actions taken by individuals (like the supervisor, John Smith), and immediate responses to the incident. Observations of environmental factors, such as wet floors or insufficient signage, play a significant role in understanding contributing factors. Comprehensive statements are essential for identifying root causes, improving future safety measures, and ensuring compliance with industry regulations.
Corrective Actions Proposed
Corrective actions proposed for vendor safety incidents typically encompass a series of systematic measures aimed at preventing recurrence and ensuring compliance with safety standards. Immediate actions might include conducting a thorough risk assessment of the facility, evaluating equipment and machinery used during the incident, and reviewing compliance with OSHA (Occupational Safety and Health Administration) regulations. Training sessions for employees on safety protocols and emergency response plans are crucial, ensuring that all team members are aware of best practices. Implementation of a detailed incident investigation process can help identify root causes, while establishing a regular maintenance schedule for equipment can prevent potential hazards. Additionally, promoting a culture of safety through open communication and reporting channels allows employees to voice concerns, contributing to a safer workplace environment. Continuous monitoring and evaluation of these corrective actions will ensure long-term effectiveness and adherence to safety policies.
Comments