In today's fast-paced business world, ensuring the health and safety compliance of our vendors is not just a regulatory requirement, but a fundamental aspect of our commitment to creating a safe working environment. By collaborating with reliable partners who share our values, we can mitigate risks and foster a culture of safety that benefits everyone involved. Our comprehensive vendor health and safety compliance letter template serves as a guide to help you communicate expectations clearly and effectively. Interested in learning more about how to streamline your compliance processes?
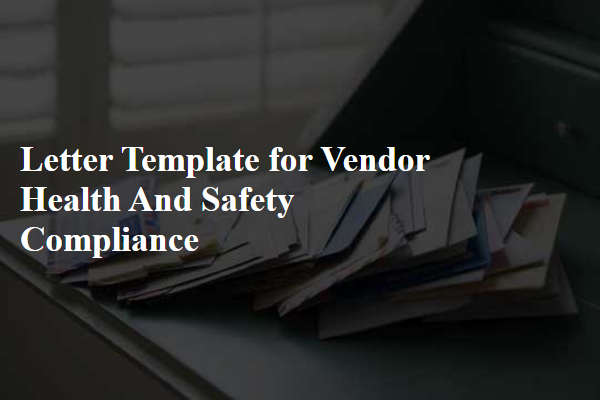
Regulatory Requirements
Vendor health and safety compliance is essential for adherence to regulatory requirements set by authoritative bodies such as the Occupational Safety and Health Administration (OSHA) in the United States. Compliance involves ensuring that facilities, equipment, and practices align with established safety standards, including proper labeling of hazardous materials and the maintenance of safety data sheets (SDS). Regular audits and assessments are critical for identifying risks associated with workplace hazards, including exposure to chemical substances like asbestos or lead. Additionally, maintaining employee training programs on safety protocols is a legal obligation that fosters a safer work environment and promotes the well-being of workers. Compliance not only mitigates legal liabilities but also enhances operational efficiency and fosters trust between vendors and clients.
Risk Assessment Procedures
Vendor health and safety compliance includes stringent risk assessment procedures to ensure workplace safety. These procedures involve identifying potential hazards in environments such as factories and construction sites. Assessors evaluate factors such as chemical exposure levels, machine operation risks, and ergonomic hazards linked to repetitive tasks. Standards set by organizations like the Occupational Safety and Health Administration (OSHA) provide frameworks for conducting thorough evaluations. Regular audits may occur quarterly or annually, depending on the vendor's operational scale. Additionally, training sessions for staff focus on emergency protocols, including evacuation routes and safety equipment usage. Implementing these procedures minimizes accidents and enhances overall workplace safety.
Training and Certification
Vendor health and safety compliance requires comprehensive training and certification programs to ensure all employees are knowledgeable about safety protocols and regulations. Effective training programs, often aligned with OSHA standards (Occupational Safety and Health Administration), include components such as hazard recognition, equipment handling, and emergency response procedures. Certifications, such as CPR (Cardiopulmonary Resuscitation) and First Aid training, are critical to maintaining a safe work environment. Regular audits and refreshers on safety practices, occurring at least annually or as required, help reinforce the importance of adherence to safety standards across industries. Additionally, maintaining accurate records of training sessions and certifications is vital for compliance verification and promoting a safety-first culture among vendors and contractors.
Incident Reporting Protocols
Incident reporting protocols are essential for maintaining health and safety standards in workplace environments. Organizations must establish clear guidelines that outline the procedures for reporting incidents, encompassing accidents, near misses, and unsafe conditions. Detailed steps should include notifying supervisors immediately, completing incident report forms, and documenting witness statements. Training sessions should occur regularly to ensure all employees understand these procedures. Furthermore, compliance with Occupational Safety and Health Administration (OSHA) regulations requires timely reporting of serious incidents, especially those resulting in hospitalization or death. Engaging vendors to collaborate in refining these protocols enhances a culture of safety across all operational levels. Maintenance of records is crucial for ongoing evaluation and improvements in safety practices.
Evaluation and Auditing Process
Health and safety compliance evaluations and audits in vendor partnerships play a critical role in ensuring the well-being of employees and adherence to regulatory standards. Comprehensive audits should follow protocols established by organizations such as OSHA (Occupational Safety and Health Administration) in the United States, focusing on identifying potential hazards, assessing risks, and evaluating safety management systems. Key components of the auditing process include on-site inspections, review of safety training programs, analysis of incident reports, and verification of personal protective equipment (PPE) availability and usage rates. Additionally, maintaining compliance with the ISO 45001 standard, which outlines requirements for occupational health and safety management systems, enhances the effectiveness of evaluations. Regular audits also facilitate identification of improvement opportunities and promote a culture of safety awareness among vendors, reinforcing commitment to health standards and ultimately securing a safer working environment for all employees involved.
Comments