In the world of business, maintaining high-quality standards is essential for success, which is why addressing supplier quality concerns is crucial. By openly communicating issues, we can work together to find solutions that enhance both product quality and customer satisfaction. This collaboration not only strengthens our partnership but also fosters a culture of continuous improvement. If youâre ready to delve deeper into how to effectively notify suppliers about quality concerns, read on for some useful tips and a practical letter template!
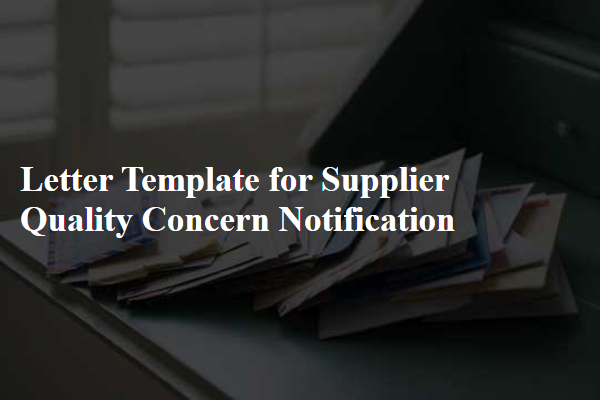
Supplier Information
Supplier quality concerns can significantly impact product integrity within manufacturing processes. For example, if a component from a supplier in Guangdong, China, demonstrates inconsistent quality, such discrepancies can lead to defective final products. In 2022, approximately 15% of production in the electronics sector was delayed due to supplier quality issues, resulting in financial losses exceeding $3 billion for companies. Affected materials, such as steel or semiconductors, require thorough evaluation to prevent operational disruptions. Addressing these concerns promptly is essential to maintain the overall supply chain efficiency and uphold customer satisfaction.
Detailed Concern Description
In recent months, a significant rise in defects has been observed in the components supplied by XYZ Corporation, particularly affecting the quality of the steel fasteners used in automotive assembly. An internal review conducted in September 2023 revealed that 15% of the fasteners failed to meet the required tensile strength specifications, with the standard set at 900 MPa. Instances of rusting were noted in 10% of the shipments received between June and August 2023, raising serious concerns regarding the corrosion resistance properties stipulated in the contract. The manufacturing issue appears to stem from inconsistent processing conditions at the supplier's facility in Los Angeles, which may have compromised material integrity. As a result, this increased defect rate poses potential risks to product safety and longevity, necessitating immediate corrective actions to address the underlying quality assurance shortcomings.
Impact on Business Operations
Inadequate product quality from suppliers can significantly disrupt business operations for companies in manufacturing sectors. Issues such as defective components or material inconsistencies can lead to production delays, affecting timelines and delivery schedules. For instance, a recent case involving a major automotive manufacturer revealed that subpar parts contributed to a 20% increase in assembly line downtime. This interruption not only strained relationships with clients but also resulted in a financial loss estimated at $5 million over a three-month period. Ensuring quality control measures and regular audits at supplier facilities is crucial for mitigating risks associated with product defects and maintaining operational efficiency.
Required Corrective Actions
Supplier quality concerns require immediate attention to ensure product integrity and compliance with industry standards. A detailed analysis of the issue, including defect types, frequency rates, and affected batch numbers, must be conducted. Corrective actions should include a comprehensive root cause analysis to identify underlying problems, followed by a clear action plan addressing process improvements and personnel training. A robust verification method should be established to monitor effectiveness, ensuring that recurrence of the issue is prevented. Documentation of all findings, actions taken, and results must be maintained for future reference and continuous improvement. Regular audits should be scheduled, evaluating supplier compliance and product quality to enhance overall supply chain performance.
Deadlines and Follow-up Procedures
Supplier quality concerns can significantly impact production timelines and product reliability. Effective communication regarding these issues should inform relevant parties about specific quality metrics that need addressing, including defects per million opportunities (DPMO), which ideally should remain below 1,000 to maintain optimal supply chain efficiency. Notifications must establish clear deadlines, such as a 14-day window for initial feedback from suppliers, ensuring timely follow-up procedures are in place. Additionally, schedule regular progress meetings, possibly weekly, to assess corrective actions taken and review any quality reports generated, including non-conformance reports (NCRs) that identify specific deficiencies. This systematic approach not only fosters accountability but also facilitates improved quality assurance across the entire supply chain.
Comments