In today's fast-paced business landscape, maintaining strong relationships with suppliers is crucial for success. Feedback plays a vital role in nurturing these partnerships, helping both parties grow and improve. Whether it's highlighting strengths or addressing areas for development, providing constructive supplier performance feedback can pave the way for collaborative solutions. So, if you're looking to enhance your supplier interactions, keep reading for practical tips and a helpful template!
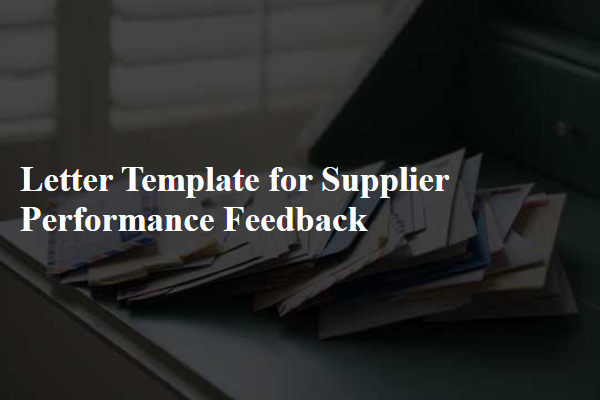
Clear Subject Line
Supplier performance feedback plays a crucial role in maintaining strong business relationships. In the context of supply chain management, feedback must be constructive and timely to ensure continuous improvement. Specific metrics such as on-time delivery rates (ideally over 95%) and product quality standards (typically less than 2% defect rate) are key indicators to focus on. Each quarter, suppliers should be evaluated to identify trends in performance, such as delays in shipping (notably in peak seasons like the holiday period), disruptions due to unforeseen events (like natural disasters or pandemics), and overall responsiveness to queries about order status. Regular communication reinforces these expectations and builds a cooperative atmosphere for mutual success.
Polite Greeting
Supplier performance is critical for maintaining quality standards in production, impacting overall operational efficiency. Comprehensive evaluations of delivery timelines, product quality, and customer service are essential for identifying areas of improvement. In recent assessments, feedback indicated shortcomings in timely deliveries, with delays averaging seven days beyond the agreed schedule. Quality inspections revealed a 15% defect rate in shipments, particularly concerning the raw materials provided. Customer service interactions also demonstrated a lack of responsiveness, with response times exceeding 48 hours for urgent inquiries. Consistent performance monitoring and regular communication can enhance supplier relationships and ensure product excellence.
Specific Performance Metrics
Supplier performance metrics, such as On-Time Delivery (OTD), Quality Assurance (QA) scores, and Cost Efficiency (CE) ratings, are critical indicators of overall supply chain effectiveness. OTD evaluates the percentage of deliveries made by suppliers, with an optimal benchmark of 95%, ensuring timely availability of goods. QA scores, typically rated on a scale from 1 to 100, reflect the quality of products received, with scores above 90 indicating superior performance. Cost Efficiency measures the actual spending against projected budgets, highlighting areas where suppliers excel or need improvement, ideally maintaining costs within 10% of estimates. Monitoring these metrics regularly can foster stronger supplier relationships and enhance procurement strategies, ultimately contributing to improved operational stability.
Constructive Feedback
Supplier performance feedback is crucial for maintaining and improving quality standards in supply chain operations. Constructive feedback should address specific areas where the supplier, such as Acme Corp., may excel or require improvement. In recent supply periods, Timely Deliveries indicated a significant drop (90% adherence to schedules, down from 98%) which affects overall production timelines at our facility in Houston, Texas. Quality Control also reported an increase in non-conformance issues with raw materials, particularly in batch numbers 12456 and 12457, leading to increased waste costs of approximately $5,000. On a positive note, communication regarding changes in inventory levels has improved, ensuring better inventory management. Future performance can be enhanced by establishing regular check-ins to ensure alignment on expectations and addressing potential challenges proactively.
Positive Reinforcement and Future Expectations
Supplier performance evaluations highlight the importance of strong partnerships in business. Consistent quality products (measured at a 98% satisfaction rate) from ABC Supply Company enhance our inventory management efficiency. Timely deliveries (averaging 95% on-time shipments) have boosted our project timelines, especially during the busy summer months when demand peaks. Communication has been excellent, facilitating seamless collaboration during urgent requests. Looking forward, continued commitment to sustainability practices will strengthen our brand alignment, particularly in response to increasing customer demand for eco-friendly options. Expanding your product range will also provide us with opportunities for new project developments, ensuring mutual growth within the competitive market landscape.
Comments