Hey there! If youâve ever grappled with the complexities of material specifications from suppliers, you know how essential clear communication can be. Making changes to these specifications is not just about paperwork; itâs about ensuring quality and maintaining strong partnerships. In this article, weâll explore effective strategies for drafting a letter that conveys the necessary adjustments while preserving your professional relationships. So, letâs dive in and discover how to articulate your needs with confidence!
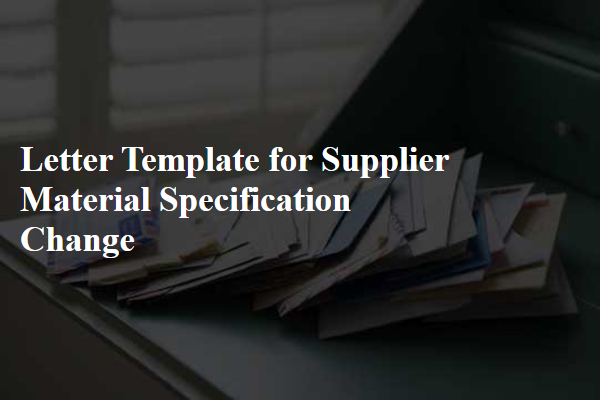
Clear identification of the material and current specification details.
Material specification changes are crucial in supply chain management, particularly for products such as Steel Alloy (ASTM A36). Currently, our specifications state a yield strength of 250 MPa and a tensile strength of 400 MPa. The dimensions are 10 mm thick plates, with a width of 200 mm and a length of 3000 mm. This material is sourced from Osaka Steel Manufacturing in Japan. Proposed changes include increasing the yield strength to 300 MPa and the tensile strength to 450 MPa, with the same dimensions. Such adjustments aim to enhance structural integrity for construction projects in Tokyo and meet evolving industry standards while ensuring compatibility with existing engineering designs.
Detailed description of the proposed changes and reasons for modification.
Proposed changes to the material specifications include alterations in the composition of the polymer used in the product's outer casing, specifically transitioning from PVC (Polyvinyl Chloride) to HDPE (High-Density Polyethylene). This modification aims to enhance durability, as HDPE is known for its high impact resistance, withstanding temperatures between -40 degrees to 120 degrees Celsius without deforming. Additionally, HDPE offers better environmental resistance, making it suitable for outdoor applications, especially in regions with fluctuating climate conditions common in North America. The switch also reduces the product's carbon footprint by utilizing a recyclable material, aligning with sustainable manufacturing practices and corporate social responsibility goals stated in the 2025 Sustainability Initiative. Furthermore, preliminary testing indicates improved performance in stress tests, with HDPE exhibiting a tensile strength increase of approximately 20%, ensuring longer product life and customer satisfaction.
Impact assessment and quality assurance for the changed specification.
Material specification changes can significantly influence supply chain effectiveness and overall product quality. When adjusting specifications, it is crucial to assess potential impacts on sourcing high-performance materials like Aluminum Alloy 6061 or Polypropylene (PP), commonly used in various industries. Detailed analysis must include supplier capabilities (e.g., consistency, production capacity), compliance with international standards (such as ISO 9001), and compatibility with existing manufacturing processes. Quality assurance protocols must ensure that altered materials maintain safety and durability requirements, adhering to regulations set by governing bodies like the FDA for food-related products or ASTM for construction. Documentation should include results from testing phases, performance evaluation metrics, and subsequent feedback from stakeholders, ensuring an agile response to any issues raised during material transitions.
Timelines for implementation and any transition period.
Material specifications, such as those for steel grades or plastic compositions, can often undergo changes due to evolving industry standards or manufacturing requirements. For instance, a shift from ASTM A36 to ASTM A992 standards in construction materials may require a transition period of approximately 60-90 days to properly implement. During this time, suppliers can assess current inventory levels, notify existing clients, and update production processes. The timeline must also account for testing and validation stages to ensure compliance with new specifications. Proper communication ensures that all stakeholders are aligned with expectations and transition timelines.
Contact information for further inquiries and collaboration.
Supplier material specifications often require updates due to various factors, including new regulations and advances in technology. It is essential that suppliers provide comprehensive documentation outlining any changes to materials utilized in production, such as polymers for automotive parts or metals used in electronics. Details must include the specific material name (e.g., ASTM A36 steel, ABS plastic), compliance certifications (such as ISO 9001), and any potential impacts on product performance or safety. Suppliers should maintain open lines of communication, providing contact information specific to inquiries regarding these changes, including phone numbers, email addresses, and responsible representatives for efficient collaboration and resolution of concerns.
Letter Template For Supplier Material Specification Change Samples
Letter template of notification regarding changes in material specifications for suppliers
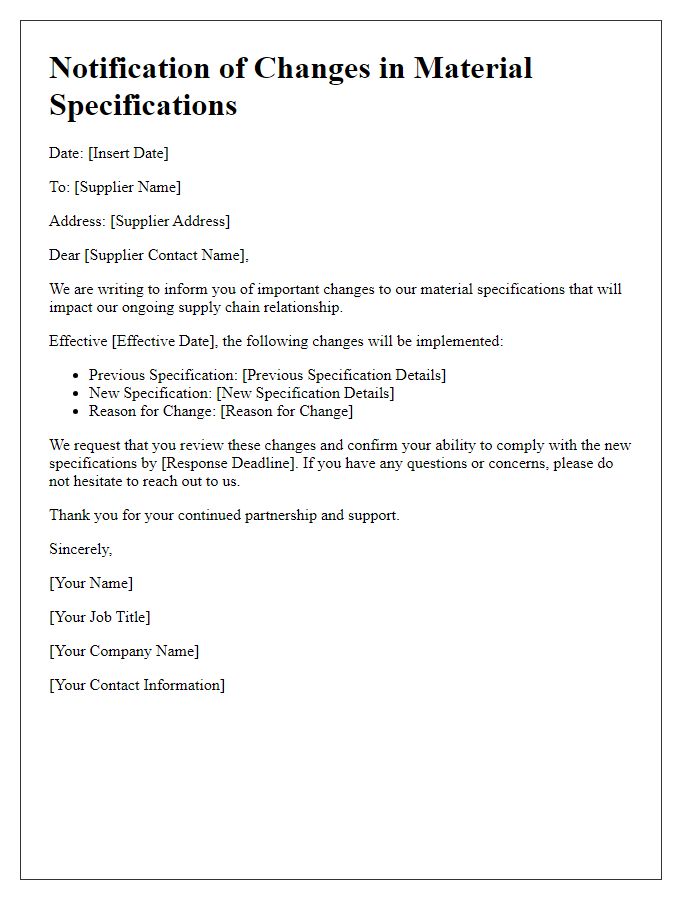
Letter template of formal communication for material specification revisions
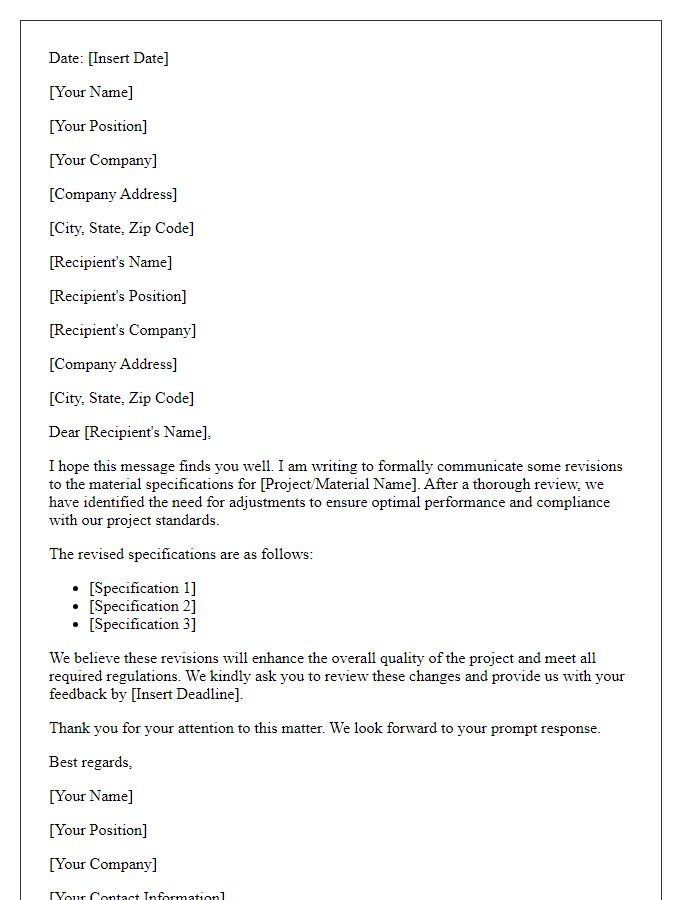
Letter template of amendment notice for supplier material specifications
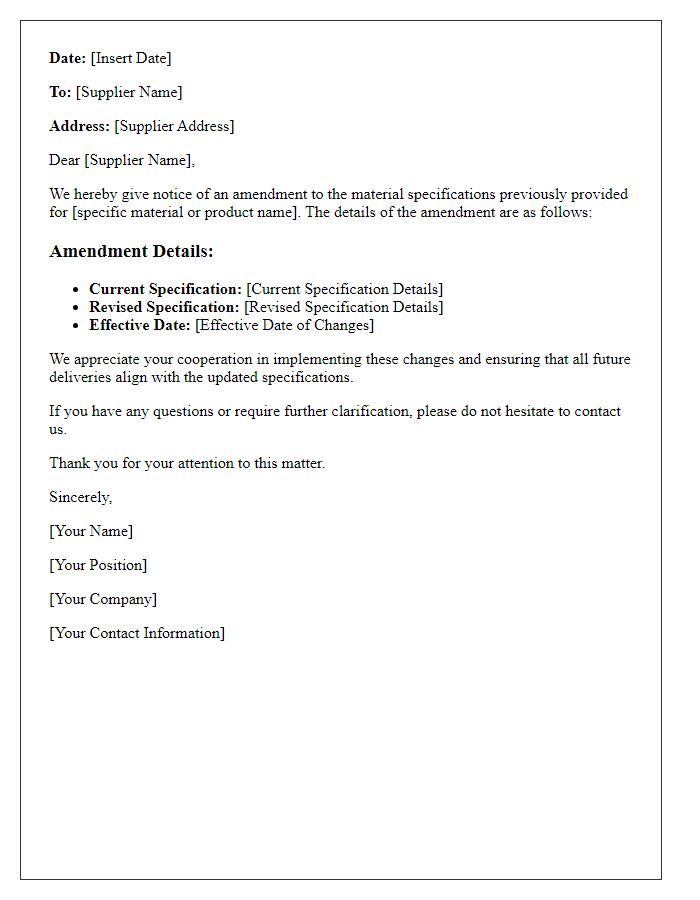
Letter template of procedural update for supplier material characteristics
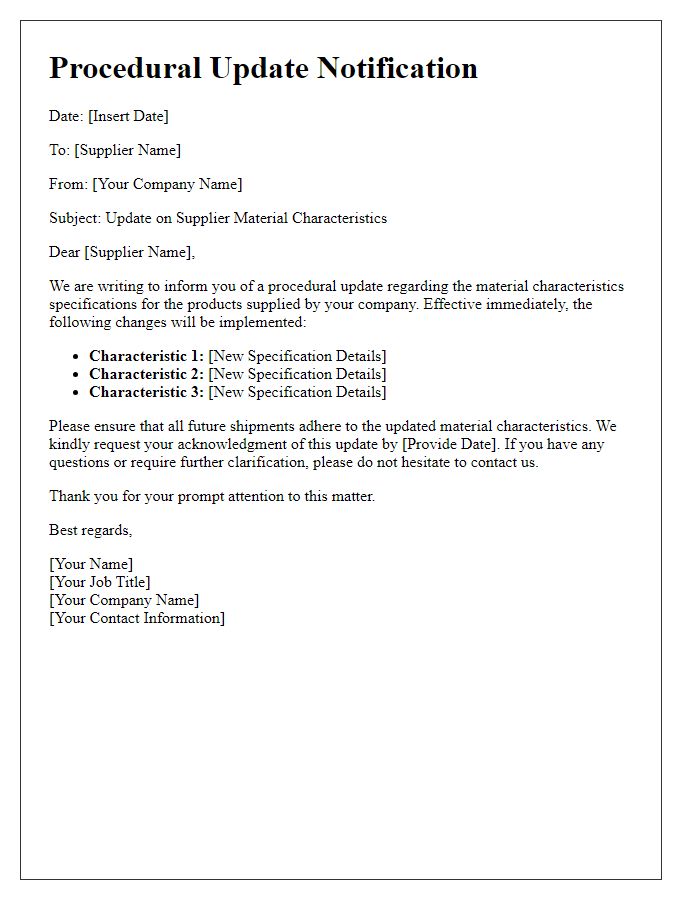
Letter template of advisory on new material specifications for suppliers
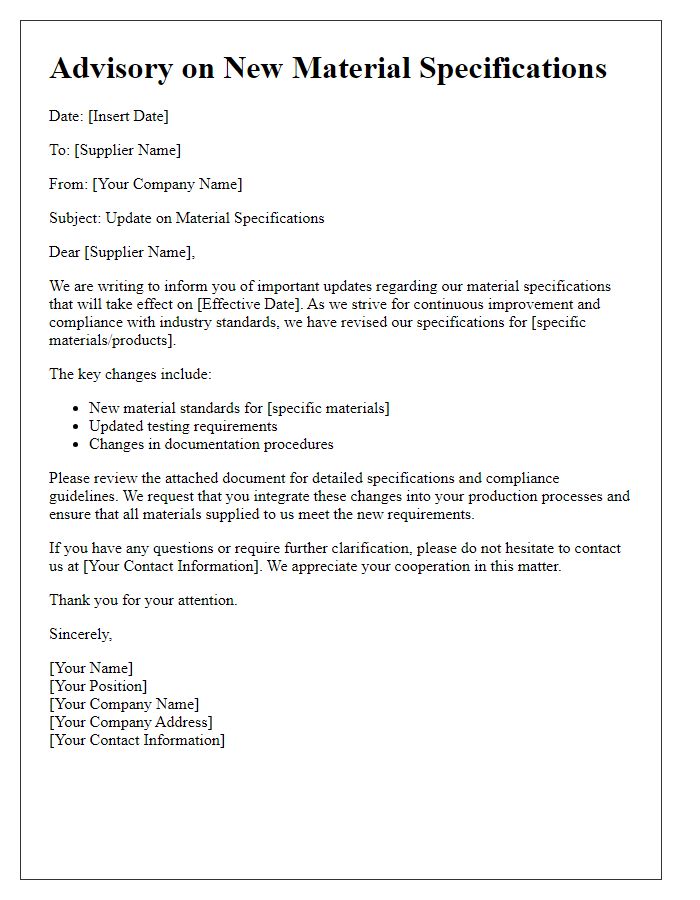
Comments