Are you looking to enhance your vendor partnerships and drive quality improvements? Crafting a quality improvement roadmap can be a game-changer in ensuring that your suppliers align with your standards and expectations. In this article, weâll explore effective strategies to communicate your vision clearly to vendors, fostering collaboration and commitment to excellence. Join us as we dive deeper into the essential components of a successful vendor quality improvement roadmap!
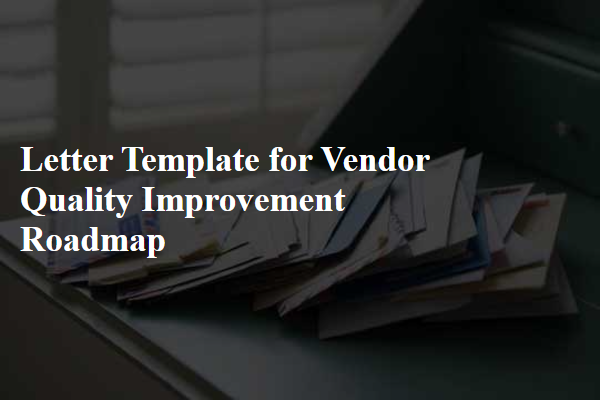
Introduction and Purpose
The vendor quality improvement roadmap serves as a strategic framework designed to enhance the performance and reliability of suppliers in various industries. Its primary objective is to systematically identify and address quality deficiencies through structured assessments and continuous improvement initiatives. This roadmap will outline the critical steps required to foster collaboration between vendors and stakeholders, ensuring high standards are met in product and service delivery. Key metrics such as defect rates, on-time delivery percentages, and customer satisfaction scores will be monitored to track progress. By incentivizing vendors to adopt best practices and innovative solutions, the roadmap aims to significantly reduce costs associated with quality failures while improving overall supply chain efficiency and customer trust.
Current Quality Assessment
Current quality assessment of the vendor's production processes reveals several areas requiring immediate attention. Manufacturing inconsistencies noted include a defect rate of approximately 8% in recent batches, significantly exceeding the industry standard of 2%. Inspections conducted at the facility in Shenzhen, China, highlighted issues with material specifications, particularly regarding the sourcing of components that fail to meet ASTM standards. Additionally, customer feedback indicates recurring complaints about product reliability, with a notable 15% of users reporting malfunctioning units within the first six months of use. An in-depth analysis of the quality control procedures currently implemented shows inadequate documentation practices, resulting in a lack of traceability for defects. Overall, these findings underscore the necessity for implementing a comprehensive quality improvement roadmap to enhance overall product integrity and customer satisfaction.
Improvement Goals and Objectives
A vendor quality improvement roadmap outlines strategic goals and objectives to enhance product quality and service delivery. Key improvement goals may include reducing defect rates by 15% within a six-month period, enhancing on-time delivery performance to 98%, and achieving compliance with industry standards like ISO 9001. Specific objectives could involve implementing a robust vendor quality assessment program, conducting biannual audits, and providing training sessions for vendor staff on best practices. Additionally, collecting data through customer feedback channels and utilizing quality management tools like Six Sigma can be instrumental in driving continuous improvement. Regular reviews will ensure alignment with overarching company standards and customer satisfaction benchmarks.
Action Plan and Timelines
A vendor quality improvement roadmap outlines essential action plans and timelines to enhance product quality and compliance with industry standards. Each action item, such as conducting comprehensive supplier audits, implementing quality control training programs, or establishing key performance indicators (KPIs), should be clearly defined with targeted completion dates. For example, initiating supplier audits might be scheduled for January 2024, while training sessions could take place in March 2024, and ongoing KPI assessments should occur quarterly starting in April 2024. Timeframes should account for all necessary steps, including planning, execution, and evaluation, ensuring every action is aligned with strategic business goals. Engaging stakeholders revisiting quality metrics in regular review meetings will facilitate accountability and continuous improvement.
Performance Monitoring and Evaluation
The vendor quality improvement roadmap emphasizes the significance of performance monitoring (continuous assessment of efficiencies and outcomes) and evaluation (systematic determination of quality standards) in ensuring optimal product delivery. Regular performance reviews (quarterly assessments) target key metrics, including defect rates (aiming for less than 2% in manufacturing), delivery timelines (ensuring 95% on-time shipment), and customer satisfaction scores (striving for an average of 8 out of 10). Utilizing benchmarking techniques (comparison against industry standards), the process identifies areas for enhancement and drives accountability. Scheduled quality audits (biannual checks) facilitate adherence to compliance standards (ISO 9001 or similar certifications), fostering a culture of continuous improvement within vendor operations (management practices that align with customer expectations). Overall, this structured approach underscores the importance of collaboration and transparency in achieving optimal performance outcomes.
Comments