Are you looking to ensure the safety and efficiency of your utility equipment? It's essential to implement robust safety protocols that not only protect your team but also enhance operational reliability. In this article, weâll explore practical strategies and key considerations that can help safeguard your workplace from potential hazards. So, letâs dive in and discover how you can elevate your safety standardsâread on!
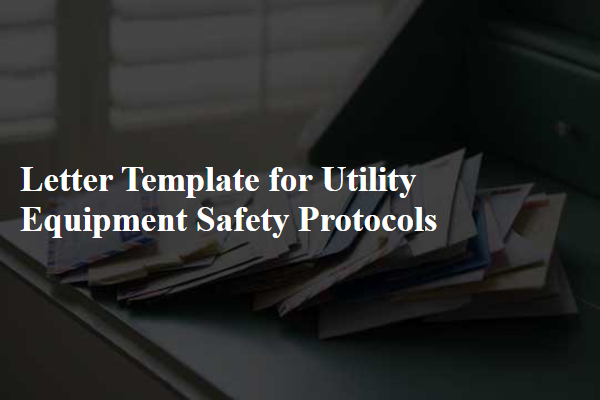
Clear Objective and Purpose
Utility equipment safety protocols are critical for minimizing risks and ensuring the secure operation of machinery, such as transformers and power lines. Establishing clear guidelines enhances the safety of personnel, with a focus on preventing accidents and injuries during maintenance and operation. Key components include mandatory personal protective equipment (PPE) such as hard hats, insulated gloves, and safety glasses. Regular training sessions are essential, reinforcing the understanding of safety practices and emergency procedures. Additionally, thorough inspections of equipment should be conducted to identify potential hazards, ensuring compliance with industry regulations. These protocols foster a safety-first culture within organizations, significantly reducing the likelihood of accidents and ensuring the well-being of all involved.
Detailed Safety Guidelines
Utility equipment safety protocols are critical for preventing accidents and ensuring a safe working environment. Personal protective equipment (PPE) such as hard hats, safety goggles, and gloves must be worn at all times to minimize injury risk in hazardous locations like construction sites (often above 40% of accidents occur without PPE). Regular training sessions should cover emergency procedures and equipment handling practices, updating staff on the latest safety regulations stipulated by organizations like Occupational Safety and Health Administration (OSHA) that govern workplace safety standards. Inspection checklists should be utilized before equipment operation, ensuring that machinery such as generators, transformers, and hydraulic systems are functioning properly to reduce failure risks. Clear communication systems must be established to alert personnel of potential hazards, with designated safety officers responsible for overseeing compliance and conducting periodic audits on safety practices. Proper maintenance schedules should be maintained for equipment, ensuring longevity and operational efficiency, which is vital given that improper maintenance can account for up to 30% of workplace injuries.
Employee Responsibilities
Utility equipment safety protocols are essential for maintaining a secure and efficient workplace. Employees must adhere to specific guidelines, including wearing personal protective equipment (PPE) like helmets, gloves, and steel-toed boots, to minimize injury risks during operation. Regular inspections of machinery, such as generators and transformers, should occur at least weekly to detect potential hazards early. Understanding emergency procedures, which include location-specific evacuation routes and first-aid protocols, is critical in workplaces like electrical substations or water treatment facilities. Employees must also report equipment malfunctions immediately to supervisors to prevent accidents and ensure a prompt response from maintenance teams. Continuous training sessions, mandated quarterly, reinforce safety awareness and protocol adherence, contributing to a culture of safety and responsibility.
Emergency Procedures
Inutility equipment operations, adherence to safety protocols is paramount for protecting personnel and preventing accidents. Emergency procedures must include immediate cessation of all equipment activity in situations such as equipment malfunction or hazardous material spill. First aid kits should be easily accessible within designated areas, typically no further than 30 feet from the equipment. The emergency contact number, such as 911 for fire or medical emergencies, must be posted prominently at each workstation. Additionally, personnel must receive training on shutdown procedures, ensuring all operators understand the significance of emergency stop buttons located on machinery (usually red) for swift action in emergencies. Emergency evacuation routes must be clearly marked and regularly practiced to prepare employees for swift and safe exit during critical situations.
Contact Information for Support
Utility equipment safety protocols are critical for ensuring the safe operation and maintenance of machinery used in various sectors, including construction and industrial settings. Adhering to these protocols can prevent accidents and injuries, such as those resulting from equipment malfunction or operator error. Key safety measures involve regular inspections (quarterly recommended) of critical components like hydraulic systems, electrical wiring, and protective gear. Training sessions must be conducted at least semi-annually to ensure that all operators are familiar with emergency procedures and proper equipment handling techniques. In the event of equipment failure, established contact information for support teams, such as the designated safety officer (John Smith, contact number: 555-1234) and equipment manufacturer technical support (TechCo, phone: 1-800-555-0199), should be readily accessible. Proper documentation, including maintenance logs and incident reports, is essential for accountability and safety compliance.
Comments