Are you looking to streamline your hardware procurement process? In our latest article, we break down the essentials of effective hardware procurement procedures to help you make informed decisions and save time. We'll cover everything from identifying your hardware needs to evaluating vendors and managing your budget efficiently. Dive into our guide and discover strategies that can transform your procurement processâlet's get started!
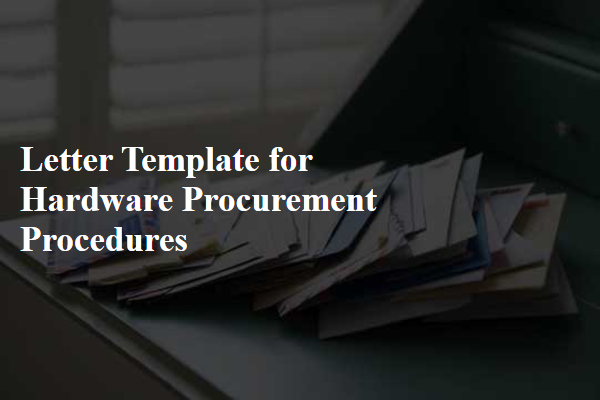
Clarity and specificity in item description
Effective hardware procurement procedures rely on clarity and specificity in item descriptions. Detailed specifications for electronic components, such as resistors rated at 1/4 watt, compatible connectors (RJ45 for Ethernet), or storage devices (SSD with 1TB capacity) ensure accurate fulfillment of orders. Supplier qualifications, including ISO certification or adherence to industry standards, play a crucial role in supplier selection. Clear timelines for delivery (e.g., within 14 business days) and warranty conditions (minimum of one year) should be established upfront to prevent misunderstandings. Documenting procurement requirements in a centralized system, such as ERP software or procurement databases, enhances efficiency and traceability throughout the purchasing process.
Budget and funding source particulars
Hardware procurement procedures require thorough documentation of budget and funding sources to ensure compliance and financial accountability. The budget typically includes specific amounts allocated for each hardware category, such as computers, servers, or networking equipment, often segmented into detailed line items reflecting quantities (e.g., 10 laptops, 5 servers) and unit costs. Funding sources may consist of grants from organizations like the National Science Foundation, institutional budgets, or departmental allocations, which require clear identification (e.g., Grant ID or Department Code). Effective procurement involves adhering to organizational policies, securing necessary approvals, and maintaining records for auditing purposes, ensuring that all expenditures align with the planned budget and approved funding mechanisms.
Supplier evaluation and selection criteria
Supplier evaluation and selection criteria play a crucial role in hardware procurement processes, ensuring that organizations acquire goods from reliable and high-quality providers. Key factors include financial stability, which often requires an assessment of annual revenues exceeding $1 million, indicating sufficient resources. Product quality, derived from customer reviews and warranty claims, should meet industry standards such as ISO 9001 for quality management systems. Delivery performance is essential, with suppliers needing to demonstrate on-time delivery rates of at least 95% to avoid project delays. Technical capability assessment involves reviewing certifications, such as Certificate of Compliance, to ensure alignment with specific technological needs. Additionally, pricing structure and the total cost of ownership, including maintenance and operational costs, must be evaluated to ensure cost-effectiveness. Sustainability practices and adherence to environmental regulations, such as the EU's REACH guidelines, can also influence supplier selection, as companies increasingly prioritize corporate social responsibility.
Compliance with company policies and regulations
In hardware procurement procedures, compliance with company policies and regulations is crucial. Each organization, such as Fortune 500 companies or tech startups, outlines specific guidelines that must be adhered to when acquiring equipment. These regulations ensure that purchases align with budget constraints, typically set at an annual cap for capital expenditures, like $200,000 for small businesses. Vendors must meet criteria outlined in the procurement policy, which often includes background checks and performance evaluations. Additionally, adherence to environmental regulations regarding e-waste disposal is required to comply with local laws, such as those enacted in California under the Electronic Waste Recycling Act. Ensuring compliance protects the organization from legal repercussions and enhances operational integrity.
Timeline for procurement and delivery schedule
In the hardware procurement process, establishing a clear timeline is essential for ensuring timely acquisition and delivery of essential equipment, such as servers, networking components, and peripherals. The procurement timeline typically includes critical phases, starting with the requirements gathering stage (usually 2 weeks), followed by vendor selection (3 weeks), order placement (1 week), and anticipated delivery period (4 to 6 weeks depending on supplier). Vendors are often selected based on criteria like pricing or past performance, which plays a vital role in optimizing delivery schedules. Thorough communication with suppliers and setting milestone deadlines for each phase are integral to the success of this procurement strategy. Ensuring a buffer period (1 to 2 weeks) for potential delays and unexpected circumstances is also advisable to maintain project timelines effectively.
Letter Template For Hardware Procurement Procedures Samples
Letter template of hardware procurement request for internal departments
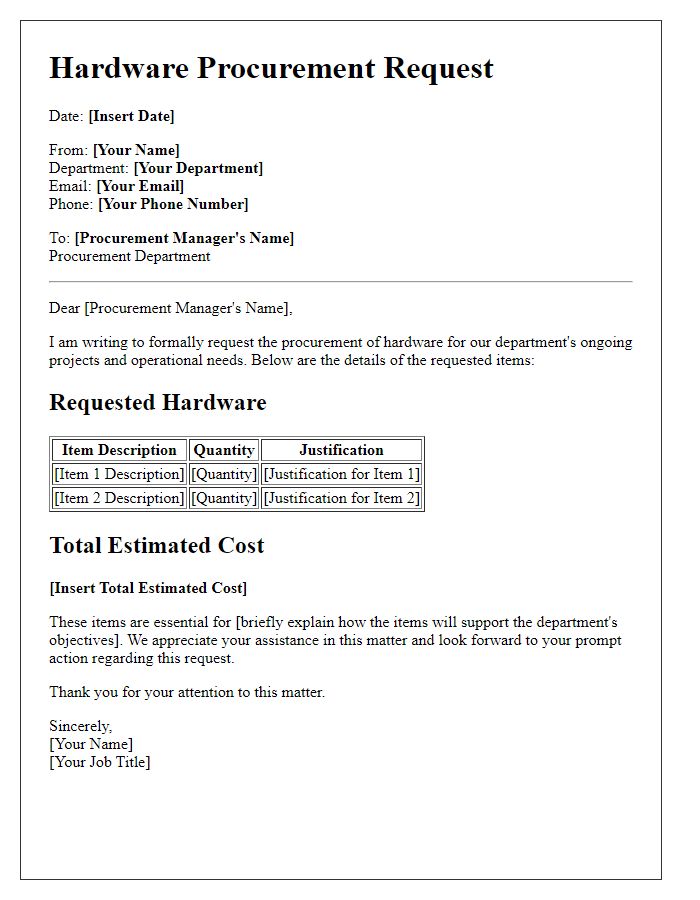
Comments