In todayâs bustling business environment, maintaining strong supplier relationships is crucial for success. However, there are times when a supplier may not meet the agreed-upon standards and compliance, which can impact the overall workflow. This article will guide you through the necessary steps to issue a non-compliance warning effectively and professionally. So, letâs dive in and explore how to ensure your supplier stays on track to meet your expectations!
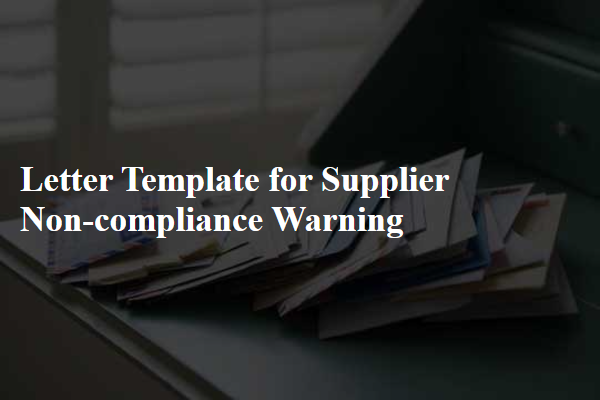
Supplier Information
Supplier non-compliance can adversely affect the supply chain efficiency and operational integrity. Non-compliance instances may include failure to meet contractual obligations, discrepancies in product quality standards, and delays in delivery schedules, which can lead to production halts. Specific documented examples could be the failure to deliver on time for critical components (e.g., steel parts needed for automotive manufacturing), resulting in production line stops that lead to estimated losses of thousands of dollars daily. Continuous non-compliance without corrective measures can strain supplier relationships and potentially affect future contracts. Ensuring adherence to supply chain agreements is essential for maintaining operational flow and customer satisfaction in industries like electronics and automotive manufacturing.
Description of Non-Compliance
Non-compliance incidents often involve deviations from standards or contractual obligations, which could lead to significant risks or losses for companies. Examples include late deliveries exceeding the agreed timeframe by more than seven days. Quality issues may arise, such as product defects exceeding 5% of the total shipment due to inadequate quality control measures at the supplier's facility. In cases of labeling errors or improper documentation, shipments may arrive without necessary certifications, compromising compliance with regulatory requirements. These issues can disrupt supply chains, resulting in financial penalties, lost business opportunities, and a deterioration of the relationship with the supplier involved. It is critical to address non-compliance promptly to ensure adherence to contractual obligations and maintain operational efficiency.
Relevant Contractual Terms
A supplier non-compliance warning may reference crucial contractual terms that outline the obligations and expectations between parties. Specifically, the agreement may include sections detailing delivery timelines, quality standards, and compliance with legal regulations. For instance, the "Delivery Schedule" section, typically specifying dates and deadlines, can clarify the repercussions of late deliveries, like penalties or reduced payment. Additionally, the "Quality Assurance" clause often mandates adherence to specific product standards, such as ISO certifications, which ensure safety and reliability. Furthermore, "Legal Compliance" requires adherence to local and international laws, including environmental regulations. This contractual framework is essential for maintaining the integrity of the supplier relationship and ensuring accountability.
Corrective Action Required
Suppliers exhibiting non-compliance with agreed contractual obligations can face significant repercussions. Such non-compliance may arise from delivering substandard materials, failing to meet specified deadlines, or neglecting quality assurance protocols. The corrective action process must be initiated immediately to rectify these issues. This entails a detailed evaluation of the deficient areas, comprising a root cause analysis for persistent problems, and the formulation of a comprehensive action plan to address these deficiencies. Failure to comply could lead to penalties outlined in the supplier agreement, which could include financial consequences or loss of future contracts. Prompt communication regarding these concerns is crucial in maintaining a productive relationship while ensuring adherence to industry standards.
Deadline for Resolution
A non-compliance warning issued to a supplier highlights critical issues regarding adherence to contractual obligations. An initial assessment can reveal a lack of quality control processes, resulting in a significant percentage of defective products, notably exceeding the agreed-upon threshold of 2% defects. The warning may specify a resolution deadline, often set within 14 days, during which the supplier must rectify the violations to avoid further sanctions, including potential contract termination. This document serves to reinforce quality standards and maintain supply chain integrity, emphasizing the necessity for compliance with industry regulations and expectations established in the operational agreement.
Comments