Navigating the delicate waters of supplier relationships can be challenging, especially when issues arise that require constructive feedback. It's essential to approach such conversations with a spirit of collaboration rather than confrontation, ensuring both parties understand the impact on overall success. By expressing your concerns thoughtfully, you can foster a productive dialogue that paves the way for improved performance and mutual benefit. Curious about how to craft the perfect message to address negative feedback? Letâs dive into our comprehensive letter template!
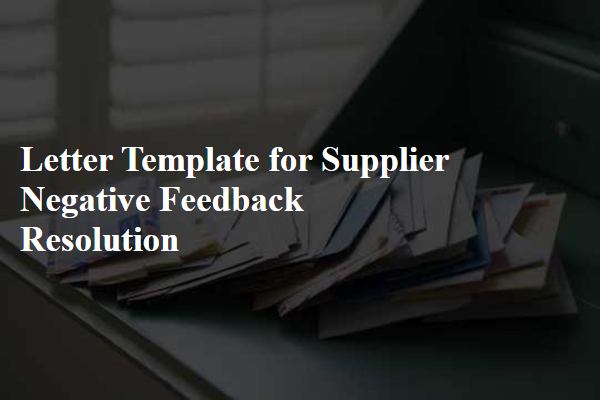
Clear identification of the issue and its impact
Supplier delivery delays can disrupt the supply chain efficiency for companies like TechCo Corp. Recent instances of late shipments have resulted in project scheduling setbacks, impacting client satisfaction and revenue projections. For example, a shipment of critical components intended for the new production line in Houston, Texas, arrived three weeks late, leading to a production halt and significant financial loss, estimated at $50,000 per week. This issue not only strains relationships with clients but also undermines the overall reliability of the supply chain, prompting the need for immediate resolution strategies.
Acknowledgment of receipt and prompt response
Acknowledgment of receipt of negative feedback from the supplier is essential for maintaining a constructive relationship. Immediate communication regarding complaints demonstrates commitment. Recognizing the specific issue, such as delivery delays or quality inconsistencies, can facilitate effective resolution. It is crucial to investigate the matter thoroughly, involving teams like quality assurance and logistics for comprehensive understanding. A timeline for follow-up actions, addressing root causes, and implementing preventive measures not only resolves the current concern but also strengthens future collaboration. Maintaining transparency throughout this process fosters trust and encourages continued partnership.
Empathetic tone and reassurance of resolution
A recent evaluation of our supply chain performance highlighted significant delays in delivery timelines. For instance, a shipment initially scheduled for June 1, 2023, arrived two weeks late, disrupting our production schedule at the Springfield facility. The unexpected delays primarily resulted from logistics issues in the transportation department of your company. We understand that challenges can arise, and we appreciate your ongoing efforts to improve your processes. However, we must emphasize the importance of timely deliveries to maintain our collaborative relationship and meet customer demands. We are optimistic about your commitment to resolving these issues and look forward to implementing a more effective communication strategy for future orders. A proactive approach will help us avoid similar scenarios and ensure a smoother partnership moving forward.
Detailed plan for corrective actions
When suppliers fail to meet quality expectations, a well-structured plan for corrective actions is essential. First, conduct a thorough audit of the supply chain process, identifying specific lapses in quality control measures. Next, issue a formal communication outlining the reported issues, such as inconsistent product specifications or delayed shipments, with clear examples from recent transactions. Implement a timeline for executing improvements, such as scheduled training sessions for supplier staff on quality standards by the end of the month. Engage in regular follow-up meetings to discuss progress and challenges, ensuring transparency. Establish key performance indicators (KPIs) to monitor compliance, with a focus on metrics like defect rates and on-time delivery percentages. Additionally, consider enhancing the supplier relationship through collaborative workshops aimed at fostering open communication and joint problem-solving strategies. This structured approach will not only address immediate concerns but also lay the groundwork for sustainable quality improvements.
Request for confirmation or additional feedback
In response to the recent supply chain issues experienced with Company XYZ, concerns regarding delayed shipments and inconsistent product quality have come to the forefront. The recent shipment (Order #12345), delivered on October 15, 2023, arrived two weeks late, resulting in production downtime and additional costs exceeding $10,000 for Company ABC. Additionally, product defects, including 15% faulty items, have compromised our operational standards and customer satisfaction ratings. Effective communication is vital; hence, a request for confirmation of corrective measures and any additional feedback regarding improvements to prevent future occurrences is essential. Urgent action is required to restore confidence in the business relationship and ensure streamlined operations moving forward.
Comments