When it comes to ensuring quality and consistency in your supply chain, a well-structured corrective action plan is essential. This letter template serves as a helpful guide for suppliers who need to address any issues that may arise. By clearly outlining the necessary steps to rectify problems, you can foster strong communication and collaboration. So, letâs dive into the specifics of creating an effective supplier corrective action plan that will set you up for success!
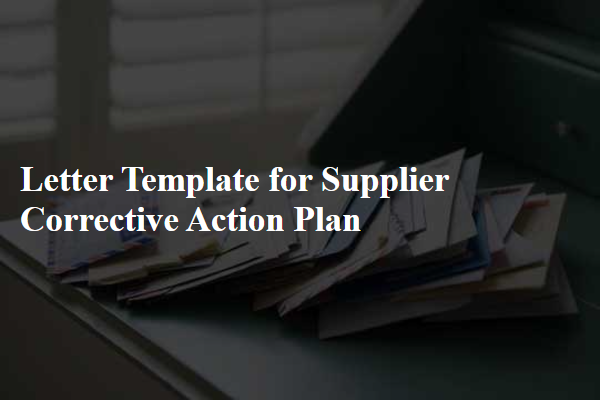
Introduction and Purpose
Introduction to the Supplier Corrective Action Plan (SCAP) focuses on addressing non-conformance issues identified in recent audits or performance evaluations. The purpose of this plan is to establish a structured approach for suppliers to rectify deficiencies, enhance product quality, and ensure compliance with specified standards. This initiative aims to foster strong partnerships and promote continuous improvement within the supply chain ecosystem. Effective implementation of the SCAP involves clear identification of root causes, development of measurable objectives, and commitment to timely resolution, ultimately contributing to enhanced operational efficiency and customer satisfaction.
Problem Description
Inadequate quality control at manufacturing facilities, such as those producing consumer electronics, has led to a rise in defective products, with return rates exceeding 15%. Specific issues include incorrect assembly processes and subpar materials used, particularly in components like circuit boards. These defects have resulted in significant customer complaints and a negative impact on brand reputation. For instance, a recent product launch in March 2023 highlighted failures in performance, causing frustration among over 10,000 users. The supplier's inability to meet established quality standards raises concerns about compliance with industry regulations and end-user safety. Addressing these problems promptly is crucial to restoring stakeholder confidence and ensuring product reliability.
Root Cause Analysis
A supplier corrective action plan hinges on an effective root cause analysis (RCA) to identify underlying issues leading to product or process nonconformance. Conducting RCA typically involves methods such as the 5 Whys technique or Fishbone diagram, utilized to dissect problems related to quality, delivery delays, and compliance issues. The analysis aims to pinpoint issues like defective materials (for example, goods failing quality control standards), inadequate training of personnel (which can lead to operational errors), or equipment malfunctions (such as machinery experiencing downtime). A thorough understanding of these contributing factors, strengthened by data (like defect rates, production yield percentages, or specific timeframes of incidents), empowers suppliers to create actionable steps for remediation. Implementing corrective measures, tracking progress through performance metrics, and setting up periodic reviews ensure the prevention of recurrence, ultimately fostering a robust supply chain relationship.
Corrective Action Plan
A Corrective Action Plan (CAP) outlines specific measures to address and rectify identified non-conformities in supplier operations, focusing on essential quality control processes. The plan typically includes a detailed assessment of the issue, such as the non-compliance observed during the supplier audit at the manufacturing facility in Shenzhen, China, in August 2023. Key components of the CAP comprise immediate corrective actions, preventive measures, responsible personnel assignments, and timelines for implementation, often requiring industry-standard documentation to ensure traceability. Furthermore, it emphasizes continuous monitoring protocols and follow-up audits to verify effectiveness, fostering a culture of compliance and quality assurance within the supply chain.
Implementation Timeline and Responsibility
A supplier corrective action plan outlines critical steps to address identified quality issues. The implementation timeline specifies deadlines, typically ranging from immediate actions (within 24 hours) to longer-term solutions (up to 90 days). Accountability details highlight the responsible parties, often identified by their role, such as Quality Assurance Manager and Supply Chain Coordinator. Milestones include regular progress reviews (weekly or bi-weekly) to ensure alignment with set timelines and resolution of issues. Communication channels must also be established for effective updates and escalations. Documentation of actions taken and outcomes achieved confirms compliance with standards, enhancing supplier relationships and performance.
Comments