When dealing with a defective shipment, itâs crucial to approach the situation with clarity and professionalism. This letter template will guide you through articulating your concerns, ensuring that the recipient understands the nature of the issue and the desired resolution. By addressing the problem directly and providing essential details, you can facilitate a swift response from the supplier. Ready to craft the perfect letter to address your defective shipment? Letâs dive in!
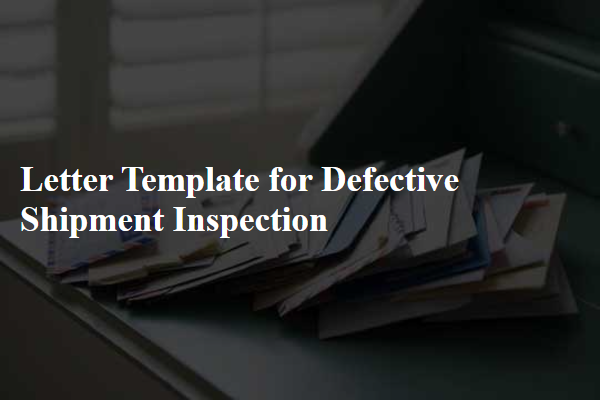
Detailed product description and defect identification
Inspecting defective shipments requires meticulous documentation to ensure clarity and actionable insights. Each product must be described with precision, including specifics such as model numbers (e.g., Model X1234), quantities (e.g., fifty units), and shipment batch codes (e.g., Batch 2023A). Defect identification should list observable issues like physical damage, missing components, or functional failures, such as non-operational features (e.g., a malfunctioning display screen). Highlighting relevant manufacturing details, including factory locations (e.g., Guangzhou, China) and production dates (e.g., June 2023), provides context for quality control assessments. This comprehensive inspection process aids in the efficient resolution of defects and helps maintain supplier accountability.
Shipment and order reference numbers
Defective shipments can severely impact business operations and customer satisfaction. Incidents involving mislabeling or damaged goods often necessitate inspections to assess the extent of the issue. Shipment reference numbers serve as unique identifiers for tracking packages in logistics systems, while order reference numbers help to verify purchase details from buyers. Accurate records help streamline the inspection process, allowing teams to identify discrepancies and facilitate returns or replacements. Furthermore, adherence to standard operating procedures during these inspections is crucial to maintain inventory accuracy and uphold the organization's reputation for quality service.
Exact condition upon delivery
Defective shipment inspections require a thorough examination of the goods received, ensuring that each item matches the specifications outlined in the purchase order. Upon delivery, it's essential to document the condition of the packaging, noting any visible damages such as tears, dents, or moisture exposure that could signify mishandling during transit. Each product must be inspected for adherence to quality standards, assessing factors such as functionality, appearance, and compliance with relevant industry regulations. Photographic evidence of defects should be captured, including serial numbers and lot codes for accurate tracking in inventory management systems. Detailed notes on discrepancies should be recorded for reporting to the supplier, facilitating a smooth resolution process and maintaining quality assurance.
Photographic evidence of defects
Photographic evidence plays a crucial role in documenting defects during shipment inspections, ensuring an accurate record of issues faced. Clear images of identified defects should be taken in high resolution to reveal details such as scratches, dents, or damages on products and packaging. In commercial settings, like warehouses or shipping docks, timestamps can further validate the timing of the defects, while labels, barcodes, or SKU numbers provide essential identification of the products involved. Additionally, images should encompass various angles and distances, highlighting the severity and extent of the defects to facilitate transparent communication with stakeholders. Properly organized documentation aids in claims processing and can help in reducing future shipping errors or quality control problems.
Requested action or resolution
Inspecting defective shipments requires a thorough examination of the goods to identify any visible damage or discrepancies with purchase orders. Shipping discrepancies can lead to significant delays, especially in logistics hubs like Los Angeles and New York. Distorted packaging may indicate mishandling during transport, potentially affecting items such as electronics or fragile goods. Quality control protocols necessitate checking product specifications against reports and photographs detailing the damage. A swift resolution is crucial, often involving refunds, replacements, or adjustments in shipping processes to mitigate future risks. Proper documentation, including inspection reports and inventory adjustments, is essential for accountability and ensuring the delivery of premium products to customers.
Comments