Are you looking to streamline your expenses and bolster your bottom line? Crafting a well-structured cost reduction strategy can make a significant impact on your organization's financial health. In this article, weâll explore practical ideas and effective approaches to help you identify areas for savings without compromising quality. So, grab a cup of coffee and join us as we dive deeper into strategies that can enhance your operational efficiency and profitability!
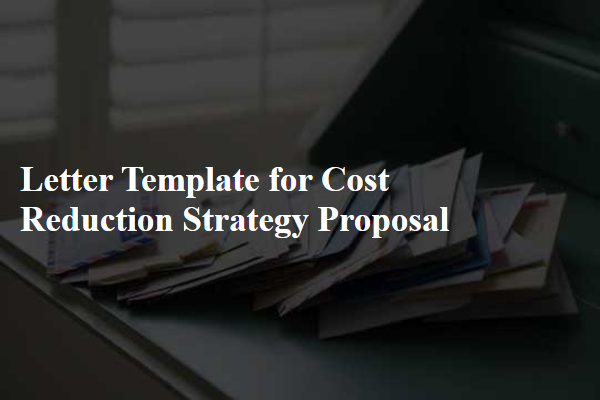
Objective of Cost Reduction
The objective of cost reduction in business operations aims to enhance profitability and efficiency by eliminating unnecessary expenses while maintaining product quality. Implementing strategies such as process optimization, resource management, and supplier renegotiation can lead to significant savings. Companies often focus on areas such as production costs, administrative overhead, and logistics expenditures. For instance, leveraging technology for automation in manufacturing can reduce labor costs, while exploring alternative materials can lead to decreased raw material expenses. By establishing clear benchmarks, regularly reviewing expenditures, and encouraging a culture of cost-awareness among employees, organizations can achieve sustainable financial improvements.
Key Areas for Savings
A cost reduction strategy proposal can identify key areas for savings, including operational efficiency improvements and renegotiating supplier contracts. Streamlining processes can enhance productivity in departments such as manufacturing and logistics, potentially reducing operational expenses by up to 20%. Implementing energy-saving measures in facilities can lower utility bills significantly, with certain businesses reporting savings of around $10,000 annually. Additionally, examining technology expenditures may reveal opportunities to adopt more cost-effective software solutions, impacting overall budget allocations positively. Evaluating employee benefits and restructuring these can also contribute to substantial savings, potentially reaching 15% of total HR costs.
Proposed Actions and Initiatives
Proposed actions and initiatives for cost reduction strategies encompass various approaches aimed at enhancing operational efficiency and reducing overall expenses. Implementing process automation, such as robotic process automation (RPA) solutions, can significantly streamline repetitive tasks, delivering potential savings up to 30% in labor costs. Reviewing supplier contracts, especially in sectors like manufacturing and procurement, may reveal opportunities for bulk purchasing discounts or renegotiated rates, potentially cutting costs by 15% to 20%. Investing in energy-efficient technologies, such as LED lighting and Energy Star-rated appliances, can lead to significant reductions in utility expenses, estimated at 10% to 35% annually. Additionally, evaluating workforce optimization through improved scheduling and remote work policies can enhance productivity while reducing overhead costs like office space rent. Implementations of these initiatives in a phased approach can ensure smooth transitions while monitoring savings effectively.
Impact Analysis and Benefits
A cost reduction strategy proposal analyzing financial impacts can significantly benefit organizations aiming to enhance operational efficiency. Identifying key cost drivers, such as supply chain expenses, labor costs, and overheads, can lead to informed decision-making. Implementing strategies like process automation in manufacturing facilities, renegotiating contracts with suppliers, or adopting lean management principles can enhance productivity while minimizing waste. The analysis should project potential savings, highlighting percentage reductions in expenditures and overall impact on profit margins. Additionally, incorporating metrics such as return on investment (ROI) or break-even analysis can substantiate the proposal's effectiveness, illustrating long-term benefits for stakeholders and reinforcing the organization's competitive position within the market.
Implementation Timeline and Monitoring
An effective cost reduction strategy requires a detailed implementation timeline and robust monitoring mechanisms to ensure successful execution and long-term sustainability. The first phase involves identifying key areas for cost savings, such as operational inefficiencies (e.g., excessive energy consumption or outdated software systems) measured by specific performance metrics. Following this assessment, an action plan will be developed, outlining responsibilities and deadlines for each team member across departments like finance, operations, and IT. A tracking system will be established, utilizing tools like performance dashboards or project management software, to monitor progress in real-time. Regular review meetings, scheduled bi-weekly, will assess adherence to the timeline and analyze the impact of changes on organizational costs. Adjustments will be made as needed to optimize results, ensuring alignment with overall business objectives. Successful implementation could lead to significant savings, potentially reducing costs by 15-20% within the first year.
Comments