Hey there! We all know that delays can be a real headache, especially in production. Whether itâs unexpected supply chain issues or other unforeseen challenges, itâs crucial to keep everyone in the loop. In this article, weâll explore how to craft the perfect production delay notification to maintain transparency and trust with your stakeholders. So, letâs dive in and discover the best practices for communicating delays effectively!
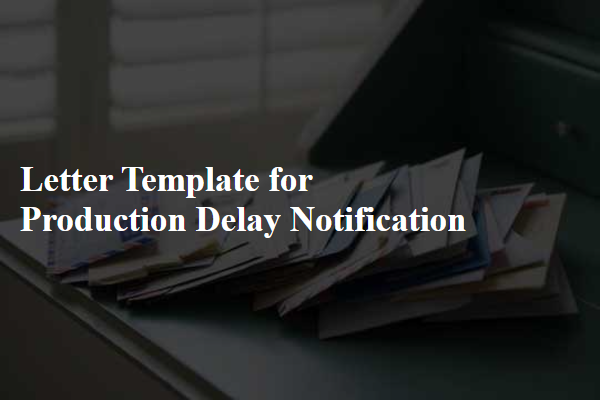
Clear subject line
Production delays can significantly impact the delivery schedules of consumer electronics, especially in industries like smartphone manufacturing. A common cause of these delays is supply chain disruptions, which can stem from global events such as natural disasters (like hurricanes) or geopolitical tensions (such as trade disputes). For instance, a factory in Zhengzhou, China--one of the largest assembly hubs for popular smartphone brands--may face shutdowns due to regulatory changes or labor strikes. Such interruptions can postpone production timelines, thereby affecting product availability in various markets worldwide, leading to potential revenue losses. Furthermore, consumers may experience dissatisfaction due to longer wait times for new device releases.
Apology statement
Apologies for the production delay regarding your order, initially scheduled for delivery on October 1, 2023. Unexpected machinery malfunctions at our manufacturing facility in Springfield have disrupted output. We are aware of the inconvenience this postponement may cause, and we deeply regret any disruption to your plans. Your order is now expected to ship by October 15, 2023. We are committed to resolving these issues swiftly to ensure the highest quality and timely delivery of our products. Thank you for your understanding and patience during this time.
Explanation of delay
Unexpected production delays can significantly impact supply chains, particularly in manufacturing industries such as automotive or consumer electronics. Factors contributing to these delays often include shortages of raw materials like steel or silicon, labor shortages due to health crises, or disruptions in logistics networks exemplified by the recent global shipping container shortage. For instance, the 2021 Suez Canal blockage caused major delays in the delivery of goods worldwide, emphasizing the fragility of interconnected supply chains. Communication with stakeholders becomes essential during these challenges, as transparency regarding anticipated timelines and affected orders can help mitigate frustration and maintain trust in business relationships.
New timeline or estimated completion date
Production delays can significantly impact project timelines and client satisfaction. A manufacturing company may encounter setbacks due to unforeseen circumstances, such as supply chain disruptions or equipment malfunctions. For instance, if a critical component like an engine part is delayed, the overall production schedule for a vehicle assembly line can be affected. The new estimated completion date may shift from March 15, 2023, to April 30, 2023, affecting delivery commitments to clients. Clear communication regarding these changes is essential for maintaining trust and managing expectations effectively. Organizations may use email or official letters to inform stakeholders about revised timelines and the reasons behind these delays.
Contact information for questions
Production delays can significantly impact supply chain operations, especially in industries relying on just-in-time deliveries. Key stakeholders, including suppliers, manufacturers, and customers, should be promptly informed about such delays to mitigate potential disruptions. For inquiries regarding the specific reasons, timelines, or alternative solutions related to production delays, stakeholders are encouraged to reach out to the designated contact person or department. Official contact channels, including email and phone numbers, should be clearly provided to facilitate efficient communication. Ensuring clear and transparent lines of communication can enhance collaboration and trust among all parties involved in the production process.
Letter Template For Production Delay Notification Samples
Letter template of production delay informing of quality control issues.
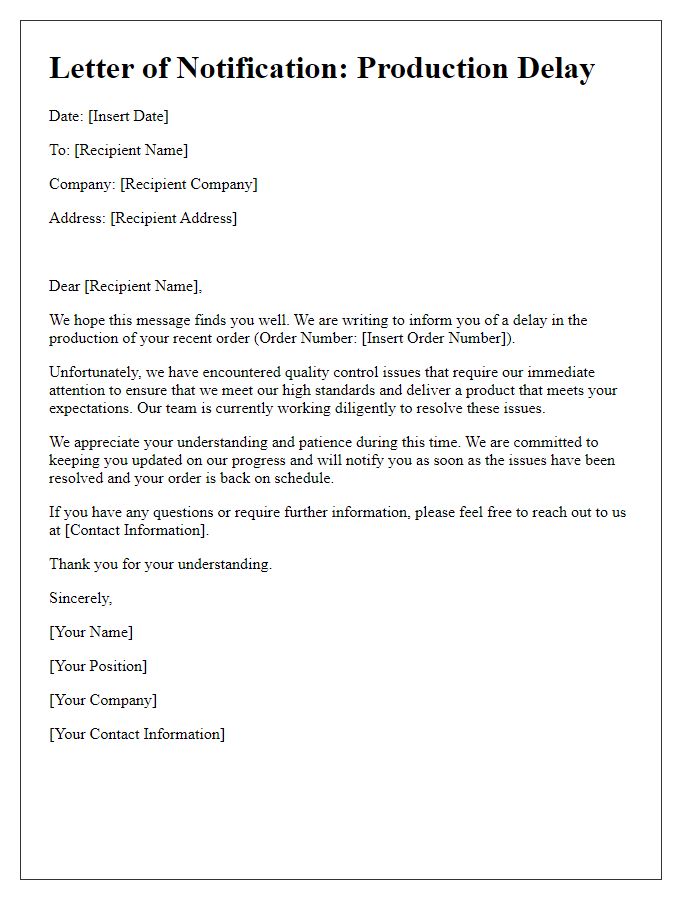
Comments