Are you ready to take your logistics process to the next level? In todayâs fast-paced world, tightening the screws on your logistics operations can lead to significant improvements in efficiency and cost-effectiveness. While it may seem daunting, reviewing your existing processes can uncover hidden opportunities for growth and optimization. Join me as we dive deeper into the essential steps and strategies for conducting an effective logistics process review!
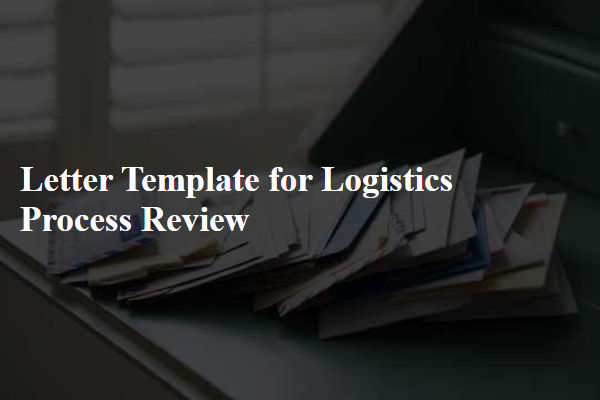
Introduction and Objective Statement
The logistics process review aims to evaluate the efficiency and effectiveness of the current supply chain operations within the company. This analysis encompasses various stages including procurement, transportation, warehousing, and distribution, focusing on identifying bottlenecks (points of congestion) and assessing performance metrics (such as delivery times and inventory accuracy). The objective is to streamline operations, enhance customer satisfaction, and reduce costs associated with logistics activities. This review will be informed by data from recent projects, industry benchmarks, and feedback from team members across all relevant departments (including operations, sales, and customer service), ensuring a comprehensive understanding of the logistics landscape.
Overview of Current Logistics Process
The current logistics process encompasses several critical steps, including inventory management, warehousing, transportation, and order fulfillment. Inventory management involves tracking stock levels, minimizing overstock, and ensuring timely replenishment, particularly in high-demand periods. Warehousing includes storing goods in strategically located facilities, optimizing space utilization, and facilitating quick order picking and packing. Transportation refers to various modes of delivery such as road freight, rail, air cargo, or maritime shipping, which must be coordinated for efficiency and cost-effectiveness, with an emphasis on timely shipment and reducing transit times. Order fulfillment is the final stage where customer orders are processed swiftly and accurately, reflecting the effectiveness of the entire logistics network. Each of these components must work synergistically to enhance overall operational efficiency and meet service-level expectations.
Identified Strengths and Weaknesses
A logistics process review reveals critical strengths and weaknesses that significantly impact overall efficiency and effectiveness. Streamlined inventory management systems, such as Just-In-Time (JIT) methodologies, enhance order fulfillment speeds by minimizing stock levels at facilities like distribution centers. Advanced tracking technologies, including RFID (Radio-Frequency Identification), provide real-time visibility, aiding in accountability and reducing losses during transit. Conversely, weaknesses such as high transportation costs, often inflated by fluctuating fuel prices, impede profit margins. Additionally, inadequate communication channels between suppliers and warehouses can lead to delays, ultimately affecting customer satisfaction. Addressing these issues is essential in optimizing logistics performance and ensuring timely deliveries.
Proposed Changes and Recommendations
The logistics process review identifies inefficiencies within current operations, particularly in inventory management systems and delivery routing methods. Streamlining the inventory management system through automated software solutions, such as cloud-based platforms like SAP Integrated Business Planning, can significantly enhance data accuracy and reduce human error. Additionally, optimizing delivery routes using advanced analytics tools, such as Route4Me, can cut down transportation costs by as much as 20% and improve delivery times. Implementing real-time tracking systems, specifically GPS-based technologies, allows for enhanced transparency in shipment statuses, fostering better communication with stakeholders. These recommendations aim to enhance overall operational efficiency, reduce costs, and improve customer satisfaction in supply chain management.
Conclusion and Call to Action
A logistics process review reveals critical inefficiencies impacting operational flow. Key metrics, such as delivery times (averaging 10-12 days instead of the industry standard of 7 days) and inventory turnover rates (notably below 4 times per year), indicate a need for immediate strategic adjustments. Elements like warehouse layout, distribution networks, and supplier partnerships require comprehensive evaluation. Identifying these pain points allows for targeted improvements, enhancing both cost-effectiveness and customer satisfaction. Stakeholders must prioritize the implementation of optimized processes, leveraging technology solutions such as automated tracking systems and data analytics tools to streamline operations. Immediate action is essential to reap long-term benefits in logistics performance and competitive advantage.
Comments