Accidents in industrial settings can have far-reaching consequences, affecting not just the individuals involved but the entire workplace community. Whether you're a safety officer needing to report an incident or a manager looking to improve workplace protocols, understanding the proper way to document these events is crucial. In this article, we'll explore a comprehensive template for crafting an effective industrial accident report. So, let's dive in and ensure we're all prepared to handle unexpected situationsâread on to discover the essential elements you need to include!
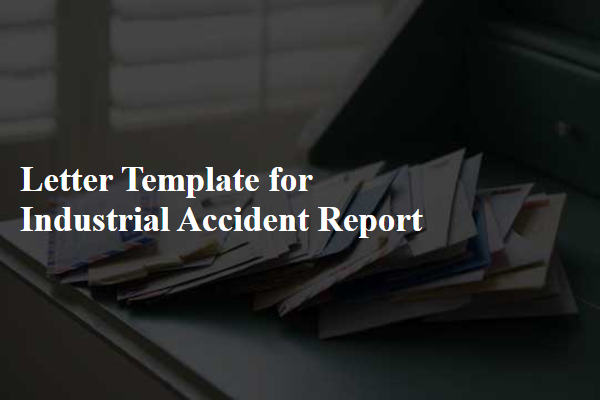
Incident Summary and Overview
An industrial accident report must capture the crucial elements of a workplace incident clearly and effectively. On June 15, 2023, at the manufacturing facility located in Springfield, a hydraulic press malfunction led to an unexpected discharge of hydraulic fluid. The incident occurred during the routine operation of the hydraulic press, which was designed for metal stamping tasks. The operators reported a loud noise followed by a loss of pressure, resulting in approximately 50 liters of hydraulic fluid spilling onto the factory floor. Emergency response teams arrived within 20 minutes to contain the spill and assess the situation. The accident resulted in the temporary evacuation of 80 employees for safety reasons, with no injuries reported. However, production downtime lasted for about three hours while cleanup operations were executed. An investigation is ongoing to determine the root cause of the equipment failure and to implement preventative measures.
Detailed Description of the Accident
An industrial accident involving heavy machinery occurred at the XYZ Manufacturing Plant in Springfield, USA, on October 15, 2023. During a routine operation, a forklift operator, John Doe, aged 35, was transporting steel beams weighing approximately 2,000 pounds each when the load shifted unexpectedly. This shift caused the forklift to tip over, leading to the machine's collision with a nearby storage rack. The storage rack, which contained various materials, collapsed, striking a fellow worker, Jane Smith, aged 28, who was standing within the designated safety zone. Immediate response from the plant's emergency medical team was enacted, leading to the transport of both employees to Springfield General Hospital. Preliminary investigations indicate a possible lack of proper securing of the load and potential mechanical failure of the forklift, both critical aspects that will undergo thorough examination in the follow-up investigations. The incident has highlighted the necessity for rigorous safety protocols and ongoing training for all operators handling heavy equipment in the manufacturing sector.
Immediate Response and Actions Taken
In the event of an industrial accident, the immediate response includes the assessment of the situation by emergency personnel. First-aid procedures are initiated to address injuries, stabilizing affected individuals (such as workers or bystanders) before professional medical assistance arrives. Emergency services, including paramedics, may be contacted urgently, especially if hazardous materials (like chemicals or heavy machinery) are involved. Additionally, the area is secured to prevent further injuries, with relevant safety protocols activated. A safety officer may initiate an investigation to document the incident's details, including location (factory site), time (specific reporting timestamp), and nature of the accident (e.g., machinery malfunction). Effective communication is crucial during this phase, ensuring that all team members remain informed and any necessary evacuations are carried out safely. The incident report generated afterward may include witness statements, photographs, or other evidence for future analysis.
Investigation Findings and Analysis
Industrial accidents can have severe consequences, impacting workplace safety and productivity. A comprehensive investigation into the incident revealed multiple factors contributing to the mishap. The accident occurred at the XYZ Manufacturing Plant, which operates heavy machinery, on October 12, 2023. Key findings indicate a failure in safety protocols, with a lack of proper training for operators on equipment such as the Model 500 Hydraulic Press. The absence of emergency stop mechanisms led to critical delays in response time. Additionally, inadequate signage regarding hazardous zones within the plant exacerbated the situation, leaving workers unaware of potential dangers. Analysis of the equipment maintenance logs from the past year highlights irregular servicing, with a gap of over six months between inspections, which is contrary to industry standards. Ultimately, the investigation emphasizes the need for stricter adherence to safety regulations, enhanced training programs, and regular maintenance schedules to prevent future incidents.
Recommendations and Preventive Measures
In the wake of the industrial accident at Plant X on March 15, 2023, where machinery failure led to significant injuries among workers, it is imperative to implement comprehensive safety recommendations. First, regular maintenance schedules should be established for all equipment, ensuring prompts for inspection every 30 days to mitigate potential failures. Training sessions on machinery operation must be conducted bi-annually, reinforcing protocols among employees. Furthermore, emergency response drills involving local safety officers should be held quarterly to prepare staff for efficient evacuation procedures. Enhanced signage indicating safety hazards must be installed throughout the facility, particularly in high-risk areas such as the loading dock and assembly line. Finally, the establishment of a safety committee composed of workers from diverse departments will facilitate ongoing dialogue regarding potential risks and review safety practices, fostering a culture of safety within the organization.
Comments